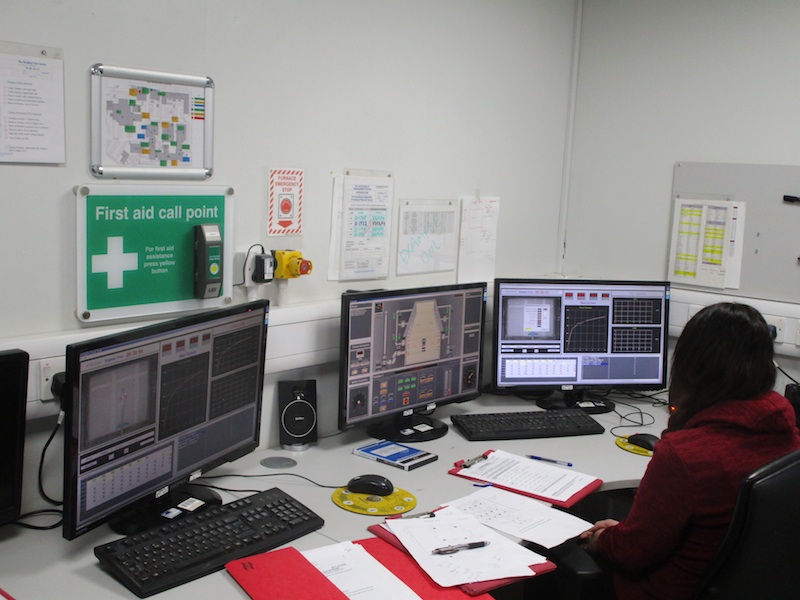
PE catches up with Paul Coy, the inventor of the Vexbox variable extension box, to find out why there was no playing with fire when introducing a new member to the product family.
It’s hard to believe that it was almost two years ago that PE first reported news that myself and the Vexbox team were working on a intumescent version of the original Vexbox system.
As you can imagine, gaining the relevant testing and safety approvals for any product related to fire safety is not a simple or quick process and since the original report went into the magazine we’ve had to make a few modifications to the product to meet both testing and production requirements, prior to subjecting the system to a fire resistance test, in accordance with EN1364-1.
What’s changed?
The two most significant changes we had to make were a) the design of a ‘backplate’, and b) an alternative method of applying the fibre glass tape, to prevent the flow of char into the wall void.
The principal purpose of the backplate (which is now called a ‘Vexplate’) is to increase the volume of intumescent material in the box, thereby allowing for a denser barrier of char to form in the box, in the event of a fire situation.
One of the benefits of having to introduce the Vexplate is that we now have a standalone product that increases the fire resistance of ANY correctly installed back box. Additionally, it’s a product that can be used to help installations comply with Building Regulations when boxes are installed on both sides of a stud wall, in the same compartment.
The method of wrapping the fibre glass tape around the template after the box has been formed is to make sure the tape is continuous around the entire perimeter of the template. When the tape was embedded in the compound, it had to be cut to allow the material to hinge. When cut, this allowed the char to escape at the corners into the wall void.
What testing took place?
It was established that the most appropriate fire resistance test for this product would be in accordance with EN1364-1, which can be very onerous to achieve.
To carry out a fire resistance test, a sample of a wall measuring 3m x 3m has to first be constructed within a steel framework, which is designed to clamp on to the furnace. The construction of the test wall has to replicate the construction of the actual wall, in which the product to be tested will be installed.
As there are numerous specifications for stud wall construction (dependant upon it’s location and purpose) it would be impossible to test every different type of construction. We decided, therefore, to select the most common wall type – two sheets of standard wallboard on either side of 70mm “C” section metal studs. The product to be tested is then fitted in to the test wall.
Again, in common with the wall construction, there are an infinite amount of ways a socket box can be incorrectly installed in a partition wall. To this end, we installed the Vexbox system at its full level of extension (35mm). As well as a variation in extension, there are variations in heights at which the outlets are installed.
The actual test requires that a sample is installed at a minimum height of 2,500mm from the bottom of the wall. This is where the furnace temperature is highest. In addition, we installed sockets at 1,200 AFFL and 450mm AFFL as these are both standard installation heights. As well as variations in heights and depths, we also installed half of the boxes in the ‘worst case scenario’ – back-to-back in the same compartment.
The wall is then clamped onto the furnace where the temperature is increased to 950 degrees C for the duration of the test. A standard test time is 30 minutes, or 60 minutes plus 10%.
Pass or fail?
There are three criteria which determine a pass or fail:
Insulation
The insulation test is to ensure that the temerature on any part of the external (unexposed) shall not increase by more than 140 degrees C.
Integrity
The integrity test stipulates that the structural integrity of the wall must be maintained and gives the maximum permitted sizes of any cracks that may form.
Lint cloth test
The lint cloth test is carried out if it appears that the cloth could be ignited by hot gases or embers escaping from either the wall or the product being tested.
On completion of testing, a comprehensive test report is written, detailing all of the parameters of the test. This includes wall construction, how/where the boxes were fitted and the temperatures of all the themocouples during the duration of the test.
Visit the Vexbox website by clicking here