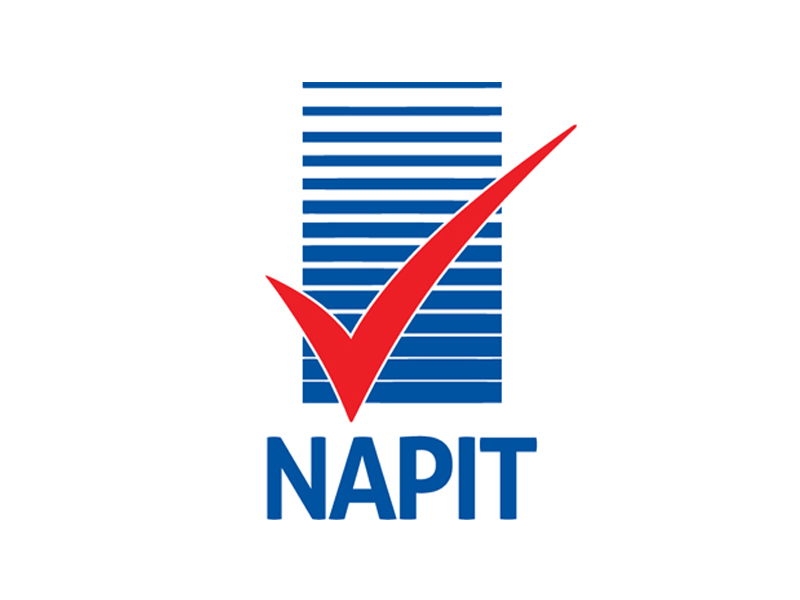
Technical Events Manager and Technical Author of NAPIT’s award-winning On-site Solutions, Paul Chaffers, takes a closer look at some of the important design considerations for distribution trunking.
Designers often need to consider which containment system is best suited to the proposed installation to ensure that the finished installation will be fit for purpose and able to provide years of service with minimum maintenance requirements.
This will include considering the installation’s intended use, site conditions, and likely external influences that will be present. In commercial and industrial locations, galvanized trunking is often selected and has proved to be an ideal containment system for many applications over the years.
These days, designers can take advantage of the many components which are now available, saving installation time (which is always welcomed) whilst providing a robust wiring system.
In this article, I will look at some of the important aspects of designing trunking containment systems that will conform to BS 7671.
Selecting the size
To size trunking correctly, all cable designs will need to have been completed because the type, size and number of conductors are all needed to choose the appropriate containment system.
Remember that when conductors are enclosed in containment, grouping factors are used and often call for larger conductors to be installed in order to have sufficient current-carrying capacity for the intended load.
There can be no adjustments if trunking is installed prior to cable calculations, which may happen on a smaller project where the electrician is the designer and gets carried away with the first fix. Usually, designs are completed prior to the start of a project, and therefore, the information needed is readily available. The actual conductor sizes are used to calculate what number of conductors the trunking can physically accommodate. Historically, 45% has been used as the space factor that shouldn’t be exceeded.
For initial sizing, manufacturers’ data should be used. Each size of cable is given a common factor, and each trunking size has been allocated a capacity factor (see example Tables 1 & 2, reproduced with permission from Legrand).
For each size of cable required to be contained within the trunking section being designed, multiply the number by the common factor. Add together the results of these calculations for all cable sizes to select the correct trunking size, which must have a capacity factor equal to or greater than this total.
Let’s try a worked example: using Table 1 calculate the total value needed for selecting the appropriately sized trunking from Table 2 for the following stranded conductors:
20 x 1.5 mm2 (@ factor 8.6) = 20 x 8.6 = 172
32 x 2.5 mm2 (@ factor 12.6) = 32 x 12.6 = 403.2
28 x 4.0 mm2 (@ factor 16.6) = 28 x 16.6 = 464.8
18 x 16.0 mm2 (@ factor 47.8) = 18 x 47.8 = 860.4
Answer = 1900.4
A study of Table 2 shows the nearest trunking capacity factor is 2091 resulting in the selection of 100 x 50 mm trunking size. Note: the trunking capacity factors take account of the space factor and trunking wall thickness.
Other sizing considerations
Depending on the type of installation, it may be desirable to select the next size up, allowing for future additions; however, this would need to be discussed with the client to ensure the benefits outweighed the extra cost.
It should also be noted that when making future additions, care must be taken to avoid changing the grouping factor of the original design, which could result in the de-rating of the existing conductors.
Cable trunking capacity tables can be used for each compartment within multi-compartment trunking. However, allowance should be made for sections where cables cross each other, such as in a tee or four-way cross, as extra space will be required.
In fact, a 50% reduction in capacity will apply at tees and four-way crosses unless offset fittings are used. Fig 1 shows an illustration of an offset tee and crossover.
Consideration must also be given to the practicality of laying cable within a trunking compartment, especially for larger cables that tend not to lie neatly and flatly.
Understanding IP requirements
Regulation 521.10.1 permits single insulated conductors to be installed into trunking systems providing the minimum degree of protection provided is either IPXXD or IP4X (see Fig 2 for an understanding of the differences between both levels of protection).
A further requirement is the lid must only be removable by deliberate action or the use of a tool.
The difference between the two ratings can be summarised as follows:
– IP4X provides protection against solid bodies greater than 1 mm in diameter entering the enclosure. The test uses a 1 mm diameter, 100 mm long test probe/wire.
– IPXXD uses the same test probe/wire of 1 mm diameter, but the top of the enclosure may allow entry of the 100 mm long test wire; however, the wire cannot touch any hazardous parts within the enclosure. Where insulation has been used to cover hazardous live parts, which can only be removed by destruction or use of a tool, the test probe is permitted to touch the insulation, as can be seen in Fig 2.
To meet IP4X requirements for trunking systems, designers will usually need to specify a manufacturer that can supply an IP4X system. There is a Note with similar advice that accompanies Regulation 521.10.1.
Any site manufactured bends or cut lengths of the trunking still have to meet the IPXXD requirement, therefore the contractor will have to ensure any joints have additional protection to ensure compliance.
Conclusion
Hopefully this article has reinforced the importance of working with proper materials whilst using manufacturers’ data to aid electrical installation designs. After all, this is one of the fundamental principles listed in BS 7671 Chapter 13, Regulation 134.1.1.
Get more details on NAPIT scheme registration by clicking here