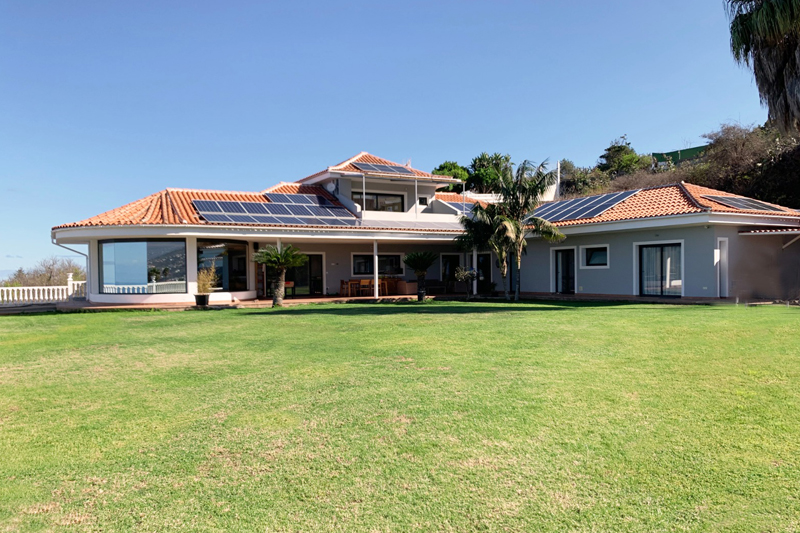
Alan Matthews, Managing Director at Automated Spaces, details the challenges his company had to overcome when commissioned to install smart home solutions at a property in the Canary Islands.
This project, based in the Canary Islands, was a major renovation which required stripping the existing plastered walls back to blockwork and completely rewiring the property, changing the layout of the ground floor rooms and adding several new rooms in the extensive basement level.
The client also decided to have a large solar panel array and battery back-up solution to provide the primary source of electrical power to the property. This meant there would be no connection to the local electrical Power Grid.
The client had several key initial requirements for the project:
1. A comprehensive security solution for the entire property,
2. The ability to listen to music throughout,
3. Great WiFi signal throughout, including in the substantial outdoor garden area.
We worked closely with the client to deliver a complete smart home solution with Control4 at its core.
KEY PROJECT STATISTICS
- 3 x floors
- 6 x bedrooms
- 5 x bathrooms
- 2 x kitchens
- 37 x zones of Control4 smart home control
- Over 11 km of pre-wire first fix cables
- 21 x zones of audio
- 2 x media rooms
- 93 x circuits of LED light fixtures
- 348 x indoor and outdoor Collingwood Lighting LED light fixtures
- 113 x custom engraved keypad buttons
A site survey with a difference
It’s not often that we have to board a plane and get to a location to carry out a site survey, but sometimes these special projects do come along. The good news is that, with the relevant export licences in place, we have the capability to successfully deliver projects in any location where our clients might need us to go.
The site survey really allowed us to understand some of the amazing features of this property which included stunning views of the Atlantic Ocean. The basement of the property was carved into the side of a cliff face and even had exposed rock visible in one of the basement rooms while the height of the ceiling in the basement rooms and other areas was nearly 4 m high.
Design phase
We were engaged by the client during an early part of the design phase and whilst the plans were still at the initial concept phases and on paper.
We had meetings on-site with the client and architect to discuss their requirements, the construction materials/methods as well as finishes, and how we could seamlessly integrate any smart home technology.
As we were providing a centralised smart lighting solution along with the specific LED light fixtures, we engaged with the Collingwood Lighting design team. They were able to provide some fantastic 3D renders that really helped the client visualise what the rooms in their finished home would look like when lit.
The Collingwood Lighting design also included some elements that the architect then decided to incorporate into the overall design e.g., the drop ceiling sections in the TV and sitting areas which he then used to conceal some of the ducted air-conditioning units.
We subsequently produced various types of design documentation, such as full system block diagrams, network schematics, power schematics, audio schematics, video schematics, head-end room layout, CCTV design, rack layouts, pre-wire cable summaries, etc.
First fix
The smart home design, as well as the physical size of the building and outdoor areas, required over 11 km of pre-wire first fix cables to be installed in this property.
With this amount of cables, it was agreed with the architect and the client that we should install basket trays around the property back to the central location that was identified as the ‘head-end’ location for all the smart home electrical equipment in the basement.
We next began the process of installing over 200 different pre-wire first fix cables, ranging from intruder alarm cables, outdoor category 6 A cables, standard category 6 A cables, HD coaxial cables, 4 core and 2 core speaker cables, fibre optic cables and smart lighting 4 core control cables.
We then installed the 4 x Control4 centralised lighting panels into the ‘head-end’ room and organised the associated LED light fixture power cables into the relevant panels.
Second fix
Initial soak testing of the equipment was carried out in the U.K. and then we shipped three pallets to the Canary Islands several weeks prior to commencement of the second fix activities on-site.
Ordinarily, we would carry out the majority of second fix activities off-site at our workshop facility but on this occasion, as we were transporting the server racks as flat pack items, it meant we would have to lace all the relevant patch cables into the 3 x 42U server racks on-site.
During the second fix we installed the relevant hardware into the server racks before running the patch cables between the server racks and patch panel utilising the overhead basket trays. We then laced the patch cables into their appropriate rack and to the relevant rack mounted equipment inside the rack.
After connecting the Pakedge router to the Internet, via a radio wave line of sight modem, we then installed the relevant software on to the rack mounted equipment and updated its associated firmware.
Third fix
During the third fix phase, we carried out the hardware installation around the property including:
- CCTV cameras
- Speakers
- Wireless access points
- Control4 touch screen
- Control4 EA1 controllers
- Control4 HDBaseT Balans
- Control4 door station
- Intruder alarm PIRs
- Intruder alarm keypads
- Intruder alarm sounder bell
We then commissioned all this hardware onto the network, before updating the relevant firmware and software patches to the latest releases.
After adding the equipment inside the engineer interface of the Control4 EA5 controller we then carried out the detailed programming of the controller to provide the functionality required by the client. This included programming numerous smart home scenes that combined the operation of many devices, at the same time, as the result of a single action by the client, such as a button press. These smart home scenes could also be triggered automatically by external events e.g., external lights turning on at sunset.
At this stage we carried out comprehensive testing of each of the sub-systems and the overall combined smart home elements. Once we confirmed that all the systems were operating as expected we then provided the client with familiarisation training.
Overcoming specific project challenges
As you can imagine, a project in a foreign country comes with its own special set of complexities and challenges, and this proved no different. Some of the obstacles that we faced included:
Export regulations: the Canary Islands are within the EU, however, they sit outside the EU customs territory and VAT area. This meant we had to have very exact adherence to U.K. export and VAT accounting rules.
A lack of locally based smart home distributors: we had to ensure we took all the correct specialised tools with us and that we shipped all the equipment and required connectors or consumables. We were able to do this because we had comprehensive design documentation that identified all the necessary equipment and interconnects.
Language and communication constraints: throughout the process we had to rely on limited translation services provided by the client and often referred to large format print-out versions of our detailed design documents.
Spanish construction and electrical standards: we found that sticking to our U.K. working practices often ensured that we surpassed the Spanish construction and electrical standards.
The finished article
Now that the client has furnished their home, everyone is delighted with the way that the smart home solutions seamlessly integrate with the property. A fantastic place in which to live their best lives! Automated Spaces is also happy to hear from electrical businesses that might be interested in mutual partnerships. Feel free to get in touch through the website.
All pictures used with this article © Automated Spaces
Visit the Automated Spaces website here