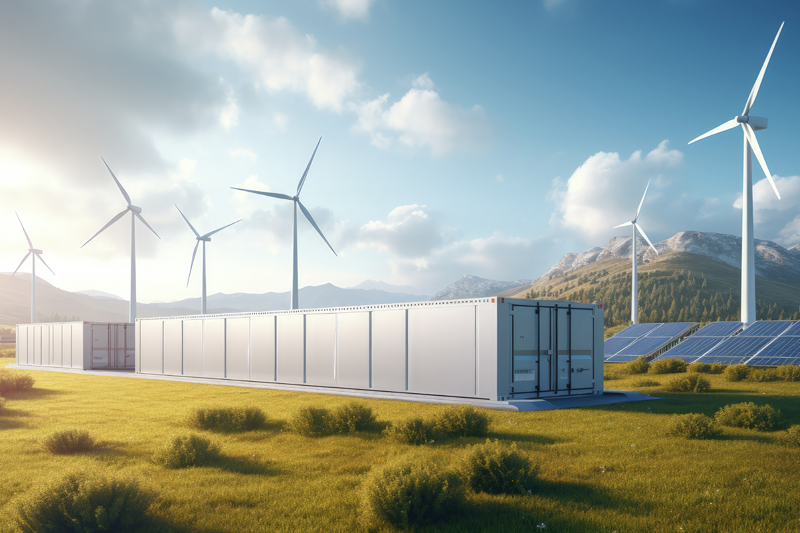
Paul Reeve, ECA Director of CSR, looks into the safety considerations installers should be aware of when dealing with Li-ion battery energy storage systems (BESSs).
In June, the Construction Leadership Council launched an industry initiative to drastically reduce the use of diesel on construction sites. Part of the initiative, headed by ECA, highlights safety considerations for the main alternatives to on-site diesel, including Li-ion battery energy storage systems.
Li-ion BESS does not routinely fail to danger but, as many social media viewers can confirm, when Li-ion goes into ‘thermal runaway’ the result can be dramatic, damaging and dangerous. A new information note from CONIAC* on the safety issues surrounding on-site Li-ion BESS cites the main operational hazards as:
- Electrical failure or contact
- Mechanical damage
- Heat stress – ambient overheating
- Charging stress – overcharging/poor charging practice.
Pent up electrical energy
Li-ion batteries, by their very nature, can hold significant electrical potential and if the terminals short-circuit (e.g. with an uninsulated object or due to mechanical damage) that electrical energy can be released rapidly.
As a result, and in addition to all the general electrical safety precautions such as keeping unauthorized personnel away, on-site Li-ion batteries need:
- protection against electric shock that aligns with BS 7671/IET Electrical Energy Storage Systems CoP, including adequate fault protection and proper consideration of the risk of DC arc flash;
- a clearly communicated safe system of work for battery fault-finding, O&M, replacement, commissioning and decommissioning; and
- clear communication of the electrical isolation procedures to competent staff/contractors, including regard for any battery-reliant critical systems.
Thermal runaway
In addition, faulty Li-ion batteries have become infamous for spectacular and dangerous thermal runaway. This can produce profuse toxic and flammable gases, energetic flame and even explosion, and it can cascade quickly in adjacent battery cells.
To help prevent dangerous runaway, Li-ion batteries typically require electrical management systems to ensure operation within controlled parameters e.g. voltages, temperature and charge states (which adjusts as battery cells age). But if the cells are stressed or damaged, degradation leading to runaway can be fairly immediate or (perhaps worse) develop some weeks later. By the time a Li-ion battery produces detectable smoke, dangerous runaway may have already begun.
However, earlier intervention after detecting initial ‘off gas’ as cell temperature and pressure rises can prevent dangerous runaway if there is a prompt shut down (even if it can’t prevent expensive battery damage). This makes effective BESS temperature monitoring a valuable precaution, whether by thermal imaging or thermometers or probes.
The hazards described here mean that only suitably trained and competent personnel should work with BESS or engage in BESS emergency measures. In particular, anyone involved in testing, connection, isolation and/or charging/discharging, should know safe operational practice and be sufficiently competent and trained (e.g. Level 3 Award in Design, Installation and Commissioning of Electrical Energy Storage Systems).
Planning for operational safety
In general, installing an on-site BESS needs a pre-site risk assessment (RA) which considers design and planning, transportation, installation and commissioning, operation and maintenance (O&M), emergency situations and end-of-service life. It will also need to consider additional measures for any BESS housed in a container.
Quality equipment required
An additional root of operational Li-ion battery failure is poor BESS design and/or manufacture. A BESS should be designed, manufactured and tested in line with UK-accepted product safety standards and component compatibility. Crucially, it should enable safe routine and emergency isolation. A BESS should also be tested promptly when it arrives on-site – cycling (charging/discharging) the battery cells as prescribed by a reputable supplier.
These and other safety measures highlighted in the CONIAC information note are essential when looking to bring BESS on-site, not just for safety and continuity reasons but, increasingly, to meet industry insurance requirements.
In a panel
Emergency planning
An on-site emergency control plan for Li-ion BESS should include:
- a battery damage plan to include how to safely move batteries (which may include damaged batteries)
- a fire emergency plan to include:
– equipment isolation/contained battery venting/personnel separation/evacuation – enabling a rapid call to the fire services (noting the risk of fire continuation or even escalation)
– essential information for the fire services
– initial cooling/flame fighting measures – avoiding/protecting against combustion products/fume inhalation. - a clear-up plan to include how electrolyte leakage will be safely cleared up and reported.
The CONIAC information notes add that it “may take tens of thousands of litres of water, applied directly to a battery, to fully extinguish and cool down a sizable Li-ion battery fire” adding “BEWARE POSSIBLE RE-IGNITION.”
Sources of further information
The CONIAC* (HSE-supported Construction Industry Advisory Council) ‘Safety issues and alternatives to diesel’ group is chaired by ECA. Its current information notes are at: www.coniac.org.uk/working-groups/managing-risk-well
Further reading
- IET Code of Practice for Electrical Energy Storage Systems
- Need to Know RE1 BESS: commercial Li-ion installations v1
- Need to Know RE2 Li-ion Battery Use and Storage v1
- National Operational Guidance at: www.ukfrs.com/guidance/search/rechargeable-batteries
Get more details about ECA membership and benefits here