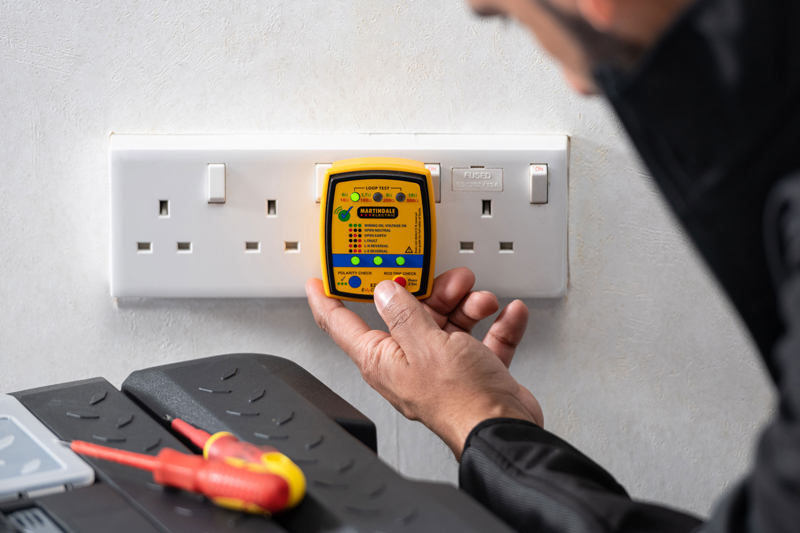
Steve Dunning, Managing Director of Martindale Electric, takes a closer look at how to choose and use the right socket tester.
Socket outlet testers (socket testers for short) have become very popular with electricians and contractors, but it’s extremely important to understand the limitations of this type of testing and the differences between the available types.
There are three main categories of socket tester: simple, advanced, and professional. All perform the basic tests to check that the earth, live and neutral, are correctly wired.
Test results are generally communicated to the user by LEDs and, in some units, by a buzzer. This not only indicates a ‘good’ or ‘faulty’ socket but should also use a combination of indicators to identify which fault type is present. All socket testers should show the absence of an earth connection; however, advanced or professional classified testers will also help verify the quality of the earth.
Advanced and professional categories measure and display ranges or numerical values for earth loop impedance, while the simple category will not show when earth fault loop impedances are excessive. For example, some recently introduced units will show you how good your earth is via resistance range indicators on the tester.
What is the difference?
Understanding the differences in the categories is important; some basic socket testers have been seen to show an earth as ‘good’, even when the impedance is exceptionally high. Sometimes this is even at a level that is typically considered suitable for insulation; it’s clear that, in this case, the ‘protective’ earth will not protect.
Earth loop values higher than a few ohms can cause problems, for example, a reliable earth loop impedance indication is vital to ensure that some over-current protection devices react fast enough to avoid electrocution. Socket testers capable of indicating earth loop impedance reveal a lot more about the electrical safety of an installation than just a simple LED wiring fault indicator.
There is one fault that a socket tester and, indeed, no other piece of equipment can easily find: the swapping of the earth and neutral wires. This is due to the earth and neutral being common at the substation (if not closer), so electrically, they’re indistinguishable.
Although all socket testers can identify wiring faults at the socket, they will not detect when the incoming supply polarity has been reversed. This serious fault condition requires an additional specific test to detect where L-NE connections have been reversed at the supply. This capability is included in some of the latest socket testers and is usually activated through a simple touchpad.
Other useful features available include an RCD test function to perform a basic trip test on a breaker associated with the socket under test. It should be remembered that this is a simple function test and doesn’t replace the RCD test as part of the 18th Edition regulations.
Many (even basic) socket testers include a buzzer to indicate the status of the socket. One advantage here is the tester can be used to help identify which socket is on which circuit, using the buzzer as an indicator while activating the circuit.
So far, we’ve looked at socket testers primarily for standard three-pin outlets, however, some manufacturers offer socket testers for the different types of sockets used in commercial and industrial applications.
Industrial socket testers tend to perform some of the same basic tests as a standard 13 A device, but with the variety of different pin configurations including four and five pin three-phase type outlets, different potential voltage levels, it’s important to identify the exact requirements needed for the application and to check the manufacturer’s specifications to identify which tests can be performed.
BS 7671 requirements
Always remember that BS 7671 requires new, repositioned, or repaired socket outlets not to be put into service until the necessary verification procedures have been completed.
These procedures include continuity testing of protective conductors and ring final circuit conductors, insulation resistance measurement, polarity checking and earth fault loop impedance. A safe approach is to use the appropriate individual instruments or multifunction installation testers.
It’s important to appreciate that socket testers are not an alternative to the complete verification of wiring installations. However, they do offer a fast and effective solution to identify potentially unsafe installations and wiring faults when correctly specified as a first-line indicator.
They can also be helpful as a service tool in identifying potentially dangerous conditions before carrying out work on existing electrical systems and equipment, before installing new appliances or performing an initial check on sockets prior to full installation testing.
Get more details about Martindale’s range of socket testers here
Find more industry technical articles here