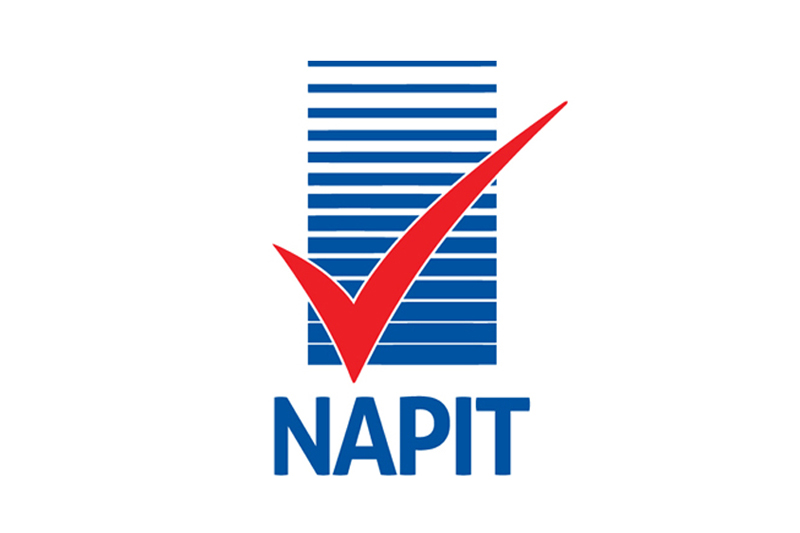
Steve Humphreys, Technical Commercial Manager at NAPIT, explores fire performance cables in detail.
A cable’s fire performance is a key area for designers of electrical installations to consider. Although electrical designers are generally not fire safety experts, they should ensure that the installation complies with applicable building regulations, standards and guidance.
This may result in the designer selecting fire performance cables and wiring systems based on the physical building, its layout and intended use.
The client’s requirements and the specification produced by the architect may also require cables to be selected with fire safety in mind.
Cables with very limited fire performance may in fact contribute to a fire or be the reason a fire spreads more quickly and produces toxic fumes or smoke. Any circuits that are intended for emergency warning or escape, such as fire detection and emergency lighting, should be designed to ensure that the system functions as intended.
Amendment 2 of BS 7671:2018 highlighted the importance of fire safety design of electrical installations within buildings. The fire safety of a building should now be documented, including details of the electrical system and the selection of cables with improved fire performance.
Types of fire performance cables
Thankfully, there is now a much wider choice for designers and installers when it comes to selecting an appropriate fire performance cable. As mentioned earlier, this will depend on its use and application.
Fire performance cables generally fall into the following three categories:
• Low smoke emission cables
• Flame retardant cables
• Fire resistant cables
Low smoke emission cables
High-density opaque smoke can seriously impact visibility during a fire, and this could have very serious consequences for evacuation and firefighting procedures. There is also an added risk of toxic fumes within the smoke causing occupants to choke, possibly leading to a fatality.
Low smoke emission cables are designed to emit minimal smoke and, in some cases, no halogen when exposed to fire. These cables are typically made with materials that contain low levels of halogens, such as fluorine, chlorine, bromine and iodine. These materials produce less smoke and toxic gas when burned compared to traditional cables, which often contain PVC (polyvinyl chloride) insulation and sheathing.
Where low smoke emission cables are used, they must be tested in accordance with BS EN 61034-2. A smoke density test assesses the level of light transmitted from one side of a chamber to the other with the cable under fire conditions. A minimum standard light transmittance level of 60% is required.
Most standard PVC cables, whether singles, sheathed or insulated, will have a low smoke emission variety. These are sometimes referred to as Low Smoke Halogen Free (LSHF) or Low Smoke and Fume (LSF) cables.
Designers still need to be careful, as there are key differences between LSHF and LSF cables. Some examples of how PVC, LSF and LSHF cables char when burnt are shown in Fig 1.
LSHF cables have no PVC or halogen compounds. These cables do smoke when burnt but will produce less than 0.5% hydrogen chloride gas.
During a fire, the cable will produce a small amount of light grey smoke, however, this has greater visibility than the thick black smoke produced by other PVC cables.
LSF cables are made up of a modified PVC compound. This compound produces less hydrogen chloride gas, around 20%, than standard PVC cables.
During a fire, the cable will produce thick black smoke due to the presence of PVC and halogen. This cable can sometimes be selected by mistake as it is assumed that it has the same fire performance properties as LSHF.
Flame retardant cables
Flame retardant cables are designed to be resistant to catching fire and restrict the spread of a fire by reducing the rate of combustion. They are constructed using materials that have inherent flame-retardant properties or by applying flame-retardant coatings or additives to the cable insulation.
These materials may include halogen-free compounds, fluoropolymers, or silicone rubber. In addition to producing very little smoke, these cables have self- extinguishing properties once the flame is removed. This prevents the fire from spreading further along the cable length.
Flame retardant cables are required to meet specific safety standards and regulations depending on the application and location. Standard testing relating to flame retardant cables is divided into a number of categories, such as single and bunch wired. These are highlighted in Table 1 and Table 2.
BS EN 60332-3-22 (Category A) is the highest level of flame-retardant cable standard testing.
It is worth pointing out that the primary goal of a flame-retardant cable is to minimise the spread of fire. During a fire, it might also maintain the integrity of the circuit, but only for a certain amount of time.
However, this type of cable should not be used if the circuit is required to maintain circuit integrity and continue to work for a specific time under fire conditions.
Fire resistant cables
Fire resistant cables are designed to maintain circuit integrity and continue to work for a specific time under fire conditions. Fire resistant cables are constructed using materials that can withstand high temperatures.
Common materials include mica tape, which acts as a fire barrier around the conductor, and insulation made from silicone, glass, or thermoset compounds. These types of cables will also have low smoke, no halogen and non-toxic properties.
These cables can endure extreme temperatures, often up to 750°C or more for short periods of time, without losing their electrical integrity. This makes this type of cable ideal for applications such as:
• Fire alarms and safety systems
• Emergency lighting
• Critical power supplies
Fire resistant cables must adhere to specific standards, such as the IEC 60331, BS 6387 and others, which define the testing methods for fire resistance alone, fire resistance with water and fire resistance with mechanical shock. These tests ensure that the cables can perform under real fire conditions.
BS 6387 CWZ is one of the most stringent tests of fire resistant cables as it consists of three test methods, such as those highlighted in Table 3.
Mineral insulated copper cable (MICC) is a good example of a fire-resistant cable. This type uses a copper conductor, a magnesium oxide insulator, and a copper sheath. It is highly fire-resistant and can withstand temperatures up to 1,000°C. Because the magnesium oxide is hydroscopic (will absorb moisture from the atmosphere) specialist glands and seals are used to terminate the cable, as shown in Fig 2.
Conclusion
When selecting cables for an electrical installation the designer needs to consider if fire performance cables are required for all or part of the installation. In light of fairly recent tragedies, such as the Grenfell Tower fire, it is more important than ever to select cables that meet fire safety standards and requirements.
There are now plenty of choices and types of fire performance cables to suit most applications and installations. BS 7671 clearly states that designers should work with other interested parties to ensure the fire safety of electrical installations is a prime consideration.
Integrating fire performance cables into buildings provides enhanced resilience, reduces the impact of fire incidents and, most importantly, safeguards lives.
For more information on NAPIT scheme registration, click here
Find more industry technical articles here