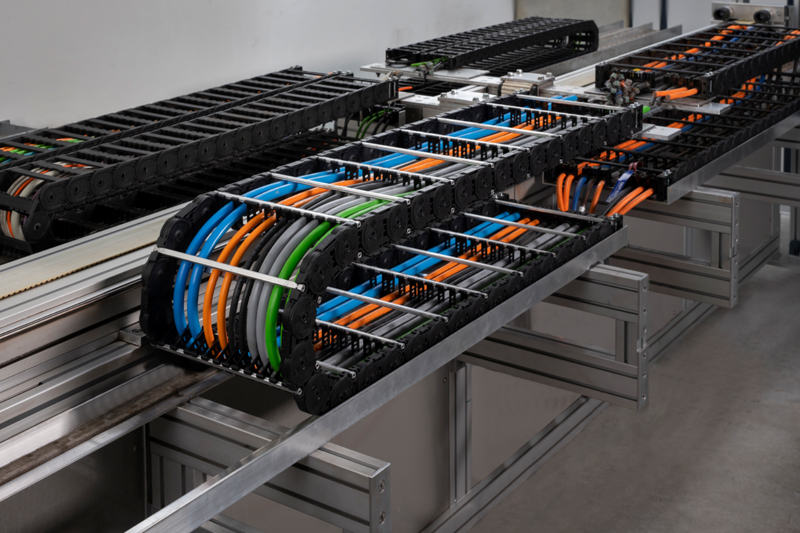
With more organisations opting to graduate from class 6 to fibre optic cables, HELUKABEL UK’s drag chain and cable expert, Liam Kinnally, offers his insight into the latest electrical cable innovation.
As machinery continues to evolve to operate at higher speeds, more companies have switched from class 6 copper-core cables to fibre optics. However, fibre optic cables characteristically tend not to perform well in continuous flexing and dynamic applications. That’s where the latest innovations come into play.
Current band-aid solutions
Car plants, for example, regularly replace class 6 server and encoder cables. This is because those cables aren’t designed to handle modern high-speed machinery. Cable coils are sat beside machinery ready to be replaced when required. While this format helps reduce downtime, not needing to change the cable as often will reduce it even more.
Meeting the demand of the people
The reason machines are evolving to operate at higher speeds is the increased demand for more products. Whether commercial, industrial, or domestic, everything is required at a higher rate. To meet this demand, machines need to produce more in the same space of time. However, not all components have evolved at the same rate.
According to Bain & Company’s 2024 Global Machinery & Equipment Report, “most machinery companies could improve productivity by 30% to 50% with a ‘factory of the future’ approach”.
Now, we’ve geared up and are innovating a solution for class 6 cable wear, allowing you to bring that ‘factory of the future’ approach to your application.
Cables tested for millions of cycles
With the requirement to switch from traditional copper core cables to fibre optics for higher data transmission speeds, contractors and installers are seeing how little fibre optics like to bend. Whether of glass optical fibre or plastic optical fibre, each has its limitations.
At HELUKABEL, we have dedicated testing facilities at our Windsbach R&D centre which allow us to diligently test the lifecycles of fibre cables and for their suitability within drag chain applications.
We understand the need for your components to withstand the operation without being subject to wear, kinks, breakage, abrasion, or other damage, so we want to lead the movement toward better, stronger, ready-to-use integrations.
Currently, our fibre optic cables are suitable for use across various steel and plastic drag chain ranges including the KOLIBRI range. These cables can flex to 10x Ø; however, our experts want to increase this further.
We want to remove the need for cable coils to be sat beside machinery by adapting current solutions that allow for component matching with improved bending radii at higher speeds.
Improved data transmission
Barely a decade ago, the concept of using fibre optic cables inside energy chains was dismissed due to a high rate of failures. Today, electrical installers can assess the suitability of these cables by reviewing data sheets and seeing the cycle capacity to which cables are tested.
Fibre optics are becoming a robust solution for a growing number of industries across the UK, from auto-line manufacturing to port applications. Where festoon systems held a monopoly, fibre optic and drag chain solutions will meet growing demands, harsh weather environments, and high-speed data transfer.
Glass fibre optic cables are a firm choice for data transmission over longer distances at more extreme temperatures while plastic fibre optics are a more cost-effective solution for applications requiring higher flexibility and better signal strength.
Strategic industry partnerships
Thanks to the acquisitions of Sangel Systemtechnik and EKD Systems, HELUKABEL is now able to offer ready-to-use system assemblies. As a leading manufacturer of high-quality cable solutions, we know the benefit of having the cable, the cable assemblies, and the drag chain pre-assembled and ready to implement when you need it.
Sangel Systemtechnik is a German-founded family-owned supplier of cable assemblies, industrial luminaires, and more. Since 2022, it has been a part of the HELUKABEL Group.
EKD Systems has been manufacturing drag chains since 1970. With over 50 years of expertise, it is a leading producer of industrial steel drag chain as well as injection-mould plastic chain while providing complete-installation services on a global level. Again, EKD Systems has been a part of the HELUKABEL Group since 2022.
Together, we are a trifecta that can help customers migrate from outdated systems to innovative future-state fibre optic solutions. Our ready-to-install cable solutions are available to businesses looking to decrease operational downtime, increase efficiency, and implement complementary components for long lifecycles.
Get more details on HELUKABEL UK’s high-performance electrical cabling solutions here
Find more industry feature articles here