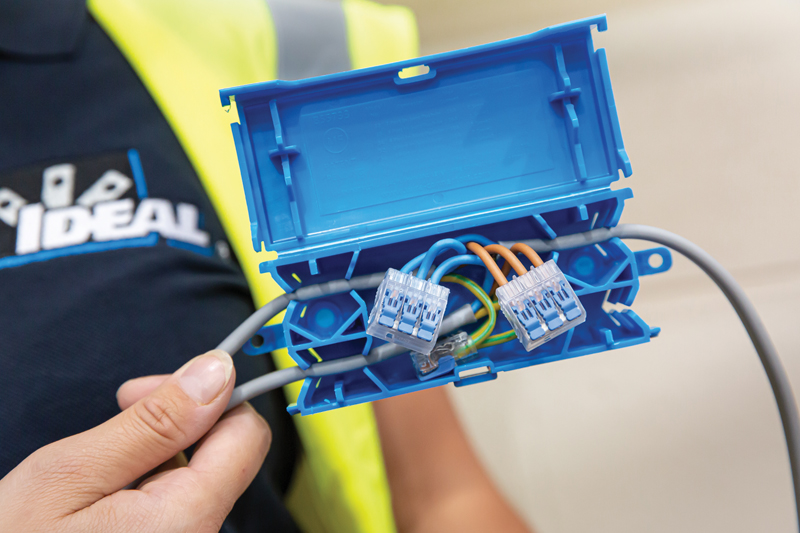
Mike Cullom, Northern Europe Sales Manager of IDEAL Industries EMEA, discusses the benefits of switching from terminal strips to lever or push-in connectors when it comes to managing time, reducing costs and maintaining quality.
The old adage ‘if it isn’t broken, don’t fix it’ is a widely used approach by those content to remain in their comfort zone, tackling jobs in the same way they’ve always done. But just because it isn’t broken, doesn’t mean we shouldn’t fix it!
As the UK construction industry seeks to recruit young talent to plug the skills gap, it represents a fantastic opportunity to overhaul traditional practices.
When it comes to the construction industry, there can be a tendency to ‘stick with what you know’, with traditional and proven methods often relied upon to get the job done. The problem is, without trying new tools and techniques, we’d never find out if jobs can be completed quicker, to a higher standard and with a greater level of consistency.
With each generation, however, comes more willingness to embrace new and innovative technologies, since younger adults are known to adopt and use a greater breadth of technologies than older adults.
A well-documented skills gap is currently threatening the UK construction and trades industry, with the UK Trade Skills Index 2023 report warning of “The Missing Million” – an alarming labour shortage that threatens the future stability of the industry unless more young people are recruited to plug the skills gap.
According to the report, to keep pace with demand, 937,000 new recruits are needed over the next decade, with nearly a quarter of a million – 244,000 – being qualified apprentices. A total of 104,000 electricians are required by 2032, which is the most of the 11 trades recognised in the report.
To tackle the skills gap, younger generations are being encouraged to consider a career in the sector, with campaigns aimed at school leavers and promoting the benefits of apprenticeships.
Fresh thinking brings new ways of working
As the electrical sector seeks to attract a younger – and therefore more tech-savvy – workforce, it’s likely that new recruits will be more open to new ways of working. Perhaps, in that case, it’s time to rethink some of the more traditional, tried and tested methods of electrical installation. Take the installation of terminal strips, for example. Many electricians and maintenance engineers will continue to use products and techniques they used when they first trained, particularly when it comes to routine tasks like making connections.
However, in a demanding sector where reconfiguration of electrical networks is a continuous requirement, it’s important to look out for better, faster and easier ways of carrying out the work.
Installing terminal strips during an electrical installation or upgrade may seem like the simplest of tasks using the most utilitarian of generic products, so switching from terminal strips to push-in or lever connectors might seem like taking a leap into the unfamiliar, but there are significant time, quality, cost and consistency gains to be had by those open to change.
Connectors: the who, what, when, why, where and how
Lever or push-in connectors typically allow electricians to secure cables in place in seconds through a simple strip, push and connect action, with no screwdriver or crimping required. This not only reduces installation time, but also delivers quality assurance for the completed installation.
Firstly, it ensures that installations are consistently safe and compliant with current wiring regulations. The 18th Edition requires that traditional terminal strip connections should be accessible for annual inspections in compliance with BS EN 60670-22, which makes it difficult to select a suitable location for terminal strip connections, leading to non-compliance for many projects.
Conversely, lever and push-in connectors are classified as maintenance-free when used in conjunction with an approved enclosure box, so can be part of a compliant installation anywhere within the facility.
Secondly, using connectors rather than terminal strips ensures every connection is consistent because there’s no variation in the tightening of the fixing screw that fastens the cable in place.
Choosing connectors with a stripping guide on the side to aid consistently accurate stripping of the cable prior to connection, along with a CPC port for relevant testing, ensures even greater accuracy and speed. This standardised approach to making the connections ensures lever and push-in connectors deliver a fit-and-forget solution.
What’s more, connectors remove any margin for error, even for inexperienced electricians. This means that routine connections can be given to less experienced operatives on-site, freeing-up the team’s most experienced professionals for more complex jobs.
Out with the old and in with the new
Connectors not only speed up installations, but they also reduce labour costs and free up the time of the maintenance team.
What’s more, making the switch provides peace of mind as connectors remove any inconsistency associated with the tightening of terminal strip screws, thereby building value into the cost of the connectors by reducing the need for quality assurance checks and eliminating the risk of issues on the electrical network.
Whether you’re an experienced contractor that has always used terminal blocks or a recently trained electrician open to exploring the latest tools and technologies, by simply switching to lever or push-in connectors it’s possible to save man hours and achieve a more consistent and compliant installation – one of the marginal gains that contributes to a competitive edge in these challenging times.
Get more details on IDEAL’s range of lever and push-in connectors here
Find more industry feature articles here