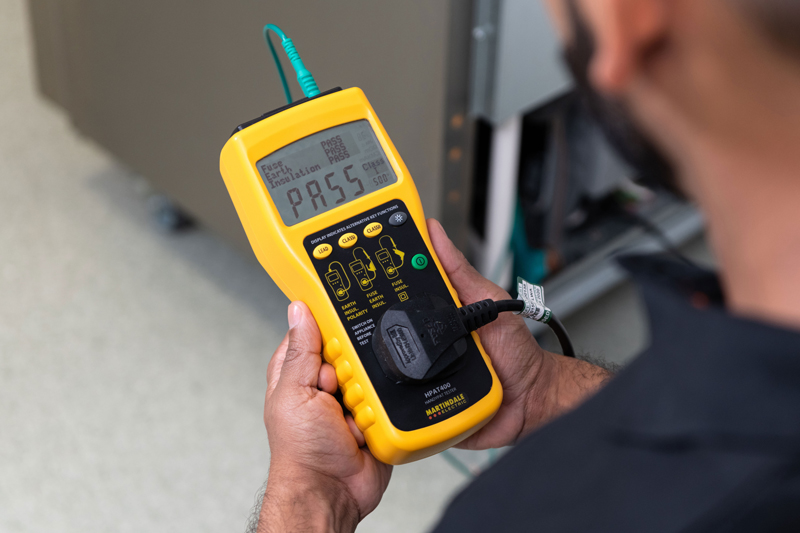
Steve Dunning, Managing Director of Martindale Electric, advises on how to ensure you are carrying out Portable Appliance Testing (PAT) correctly.
Every year, a significant number of electrical accidents, many involving portable appliances, are reported to the Health and Safety Executive (HSE) in the UK. In accordance with the Electricity at Work Regulations (1989), any electrical equipment that has the potential to cause injury must be maintained in a safe condition.
Designed to help raise the standards of electrical safety in the workplace, portable appliance testing ensures that electrical appliances and equipment which have been classified as “portable”, are safe to use.
For the purposes of PAT testing, portable appliances are defined as those that use a flexible cable or plug and socket. This means if an appliance has a plug connected to a wall socket or generator, it should be PAT tested. This definition includes either hand-held or hand-operated equipment, intended or likely to be moved (Refer to the Fifth Edition of the IET Code of Practice for full definition).
To help companies with their portable appliance testing strategy there are many commercially available PAT training courses. These are invaluable to help provide the necessary theoretical and practical knowledge to undertake testing and inspecting different electrical appliances.
While the Fifth Edition of the IET Code of Practice emphasises the need for risk assessment, partly to reduce unnecessary testing, it still requires that a competent person carry out Portable Appliance Testing.
When undertaking inspection and testing, a training course will provide a high level of knowledge needed and give invaluable information on the right test equipment to use, the ability to use it properly, and the ability to properly understand the test results. However, even for an experienced user of portable appliance testers there are 12 potential errors which need to be carefully avoided:
1) Lack of visual inspection
It may seem obvious, but before you measure the condition of an appliance, make sure that all its parts are there – and in good condition. Any signs of damage should be reported as well as any dents/scratches on the casing. These can indicate that the appliance has been dropped or handled incorrectly at some point in its life. If the cable shows signs of wear or isn’t plugged in properly, this should be recorded as it could indicate that the appliance is unsafe.
2) Not carrying out the tests in the required order
If on a Class 1 appliance you do the insulation test first, you don’t know if the conductive earth path is good (in Class 1 appliances most PATs use the earth wire as the return signal path, which is why you don’t need to use a probe for the insulation test). If the earth path isn’t tested and proven good, you can’t rely on the insulation test.
3) Forgetting to switch the appliance on
Think about the situation where the live wire is broken inside the appliance and touching the outer casing. When you do the insulation test, everything inside the appliance should be at 250/500 V. The tester detects (via a probe or the earth wire) any voltage escaping to the appliance housing. But if you haven’t switched it on the voltage can’t get through the live wire, nothing will escape and you could have an incorrect pass of a dangerous appliance.
4) Touching the appliance
The reality is that most appliances pass the insulation test, so you get into the habit of holding drills etc. to make it easier to hold the probe in contact. Then one day the appliance insulation fails and results in a shock.
5) Only conducting one earth bond test
If an appliance has multiple, apparently isolated, outer parts with separate earthed paths, each one needs to be separately measured (some of the earliest testers had standard test sequences that only expected you to do one earth test).
6) Taking an average reading
If you have multiple earth paths, don’t take the average reading – it’s the worst case that matters.
7) Trying to undertake an earth bond test on a Class II appliance
It will, of course, fail as Class II appliances have no earth. This is a very common problem and causes a large number of calls to technical helplines.
8) Only carrying out one insulation test
For the same reason as #5, this is a common fault. At how many places on a power tool could the insulation break down? Obviously at the chuck, but what about the ventilation slots, the trigger, the assembly screws, the speed control?
9) Not checking the fuse is conducting (see point #3)
You don’t have to carry out a separate fuse test – the function test will prove that the appliance is both on and the fuse is okay.
10) Failing to conduct a functional test (powering it up)
Some entry level PATs don’t have the ability to power up the appliance. If your PAT tester doesn’t then plug the appliance into the wall socket (after PAT testing) and make sure it works properly. Putting your initials on a PASS label for an appliance that doesn’t work or is obviously faulty is a bit embarrassing.
11) Not testing at the correct voltage
It’s very common for people to make the mistake of performing a 500 V test on surge protection extension leads. These require a lower voltage 250 V test, which is especially helpful when testing appliances with surge protected circuits, such as sensitive IT equipment at 250 V.
12) Not calculating the correct pass level
Many appliances use longer power cables than those specified by the manufacturer. The current pass level for an appliance with a longer power cable is calculated differently than the pass level for an appliance with a shorter power cable. The current pass level for an appliance with a longer power cable can be determined by a calculation available in the PAT code of practice.
Given the importance of PAT testing and the wide variation in operating environments and equipment to be tested, it is extremely important to ensure the right equipment is selected to suit the application. Often overlooked but vitally important when choosing a tester is to ensure all bases are covered not only on appliances but also with mains extension leads.
It’s also important to consider accessories early in the selection process such as labels and adaptors for appliances etc. Ideally, a unit will have a good range of readily available accessories for use across a wide range of applications.
Get more details on Martindale’s range of PAT Testing equipment here
Find more industry technical articles here