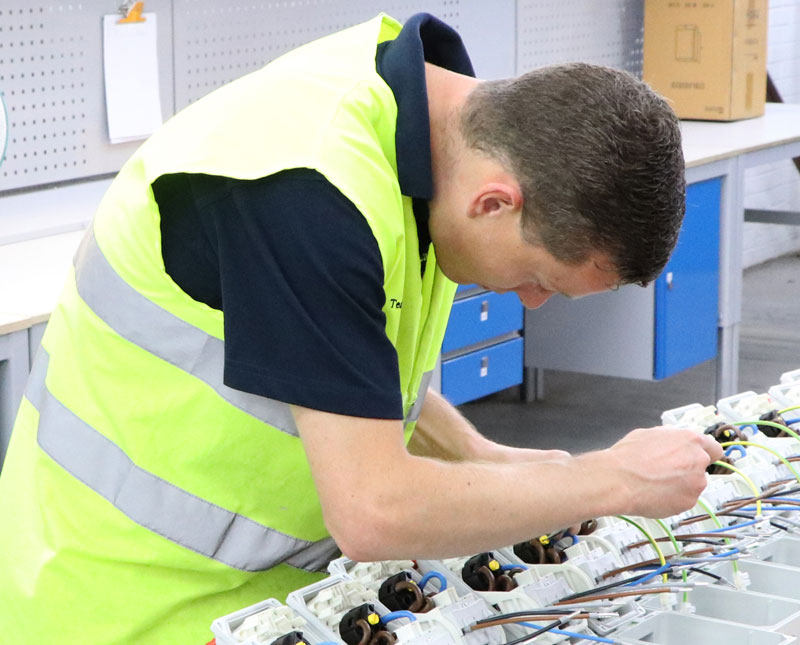
David Holloway, Product Manager at Europa Components, advises installers about the potential consequences of careless ‘torque’.
It’s well known that loose connections cause overheating and, in severe cases, could initiate a fire. Over-tightening of the connection can also produce similar effects by excess stresses on the terminal/screw which could lead to mechanical failure of the screw, the thread being stripped or the terminal body being stretched or fractured.
On tunnel/cage terminals where the conductor is in direct contact with the terminal, over-tightening could also result in damage to the conductor, especially where the terminal screw is in direct contact with the conductor. All of these effects could lead to loose connections, creating high resistance and resulting in overheating.
On larger cables where lug terminals are used, it’s still important to apply the correct torque to ensure the bolt is tightened properly and isn’t applying excess stresses to the bolt, lug and threads beyond the manufacturers design parameters of the switchgear.
What did we used to do?
Historically, by tightening the terminal by hand, you could feel if it was tight enough well before failure of the terminal or conductor. This relied, however, on experienced installers and was inconsistent, as everybody’s view on how tight a terminal should be differed.
The requirement to apply a torque to a connection has been around for some time, but with the use of powered screwdrivers, overtightening of the terminal has become more commonplace. Where a failure has occurred for this reason, in most cases the installer believes that the product is at fault.
Some power tools have a torque setting, but generally these haven’t been calibrated and the torque applied varies with how much the battery is charged and the speed of tool. Also, as the power tools are used frequently, the internal mechanical parts are subject to wear, which tends to produce a less consistent applied torque. Power tools can still be used in the installation but the torque setting must be well below the final torque value. The final tightening of the screw terminal can then be carried out using a manual torque driver.
“Power tools can still be used in the installation but the torque setting must be well below the final torque value.”
Where do the torque figures come from?
All torque figures should be stated by the product manufacturer. These are generally based on the values that were used when the product was tested to a British/European or International product standard. The tests that are carried out on the terminal include a mechanical test, where a known torque is applied to the terminal a number of times with no conductor.
The terminal is also tested with the smallest conductor and the largest conductor as specified by the standard or the manufacturer, with the conductors then inspected for damage. All of these tests are carried out using a calibrated hand held torque driver at torque settings specified by the relevant standard.
What is the best way to apply the correct torque value?
All torque values must be applied by using a calibrated torque driver. Small torque drivers are similar to screwdrivers with interchangeable bits and the latest designs are much more compact and slimmer than ever before. The changing of the torque value is also much easier and quicker on the new designs, when compared to the earlier types. Larger torque values are applied with a torque wrench that you might recognise if you’ve carried out any vehicle maintenance before.
All torque drivers must be calibrated at regular intervals, but this is dependent on how often the torque driver is used, so it’s best to get some guidance from the manufacturer regarding the frequency of calibration.