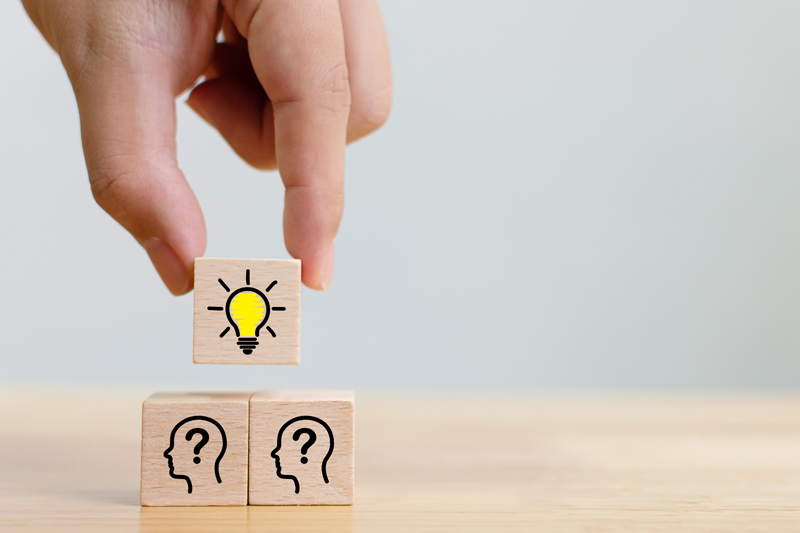
Richard Kemp, Head of Innovation for Ansell Lighting, explains how the company’s products make the journey from creative spark to safe, functional and eye-catching installations in locations such as hospitals, warehouses, schools and homes.
When Ansell Lighting creates a new luminaire design, a huge amount of work will have already been done before we embark on putting the design and production process in motion. At the centre of all our product development is the contractor who will install the luminaire and the customer who will be investing their money in it.
Encouraging customer input
We pride ourselves on being a company which listens to its customers and we openly engage with contractors and end users to help make our products easier to install, cost and energy-efficient, and aesthetically pleasing.
We actively encourage customer input and take the feedback we receive via our media platforms seriously. This approach enables us to apply more practical features into our product.
The circular economy is also a priority, so we look at how the design of our new light fittings can make them easy to repair, to extend their lifespan.
Value for money has always been central to the Ansell brand, but we believe it is the clever additions to our design process, directly informed by our customers, that makes us different. Take, for example, our Otto Evo high-performance LED CCT, an architectural suspended linear fitting for modern commercial office, retail and educational applications.
Collaborative design
Input from contractors was crucial to the design of the Otto Evo, which has been lauded for its quick, simple and versatile installation process.
Their on-the-ground experience and expertise informed a raft of labour-saving features, including the adjustable, sliding mounting bracket on the diffuser, dropped wire suspension cabling on the luminaire with centre pull clips which can be effortlessly manoeuvred to location grooves, as well as pre-set markings to facilitate fixing, spacing and alignment.
Upgrades or servicing can be carried out safely and conveniently thanks to a lift-away top section which allows instant access to internal components and wiring.
The design also delivers benefits for the end user, featuring optional functions such as an integral microwave sensor, corridor control and digital dimming for energy savings, and compatibility with Octo smart control for ultimate user control.
Robust design review
Our project engineers carefully review the market to ensure we are making products that are current and meet the latest legislation – and at competitive prices to please the professional electrical wholesale chain.
All products are carefully designed using 3D CAD to create initial drawings which form the template for a 3D plastic model. This is where we start to put our innovation to the test.
The prototype enables us to thoroughly investigate how the product will work in the real world – Is there adequate wiring space? Does it allow for future upgrades? – and ensure that our design translates into a workable and impactful product.
Usually, we will make a series of working samples. These are shown to Ansell’s internal technical committee for evaluation and initial feedback. Then it is on to the all-important contractor feedback.
This always provides valuable reinforcement of our designs. It can be a very grounding exercise but we’re always conscious that a well thought out product with good reliability is paramount. All feedback is good feedback, after all.
Quality and performance testing
Ansell Lighting has achieved LIA Laboratory Certification 003 for our luminaire testing facilities in Warrington – one of just six laboratories in the UK to have achieved the accreditation. This enables us to validate the quality and performance of all our new products in-house, using our state-of-the-art goniophotometer, the Gonio Tunnel.
Over a three month period our 3D design prototypes are run through a series of rigorous tests encompassing thermals, electro-magnetic compatibility, harmonics, ingress protection, impact testing and material ageing, to ensure complete accuracy and compliance with industry standards.
When we’re completely satisfied, we will pass the products to an accredited test house for final certification as an added assurance of quality.
Producing the goods
Good quality production is an area that we really understand, and one which we’ve invested in over many years. The result is a very skilled supply chain that works with us to ensure the latest materials and machinery are used.
Quality and continuity is a top priority and even after production has started, we monitor goods throughout the entire process. External auditors continually check our supply chain to ensure that our products are produced to A1 standard. Our loyal customer base expects nothing less.
From production line to purchase
At the end of the production process we’re always confident that we have a product that fulfills our criteria of meeting health and safety standards, installation needs, energy efficiency goals, functionality requirements – and is visually impressive.
The process up to this crucial point might have taken many months, during which time our marketing and sales teams will have been gearing up to swing into action. The product might find its way to one of our state-of-the-art showrooms, in Belfast, Warrington and Dublin, where its benefits can be demonstrated in-situ to wholesale customers, contractors, architects and consultants.
We’ll have marketed it across all media platforms to ensure our customers know there is a new product to look out for, while our Warrington and Belfast sales teams are fully informed and prepared to answer any questions our customers might have.
There is really just one final stage left, the purchase of the new Ansell Lighting product. That is down to our customers – the very people who have informed every aspect of its journey from concept to reality.
To browse the latest Ansell Lighting product catalogue, click here