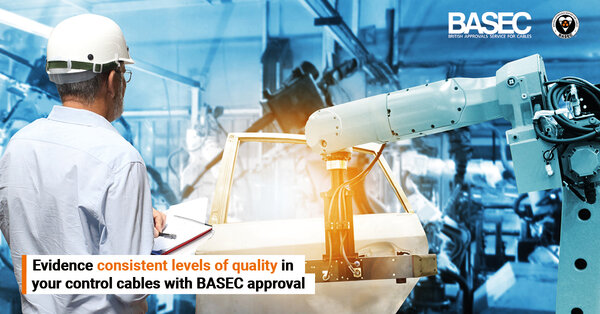
We learn more about why it is important to ensure you quality check the control cables you’re using.
Control cable products such as SY,CY and YY are used in a variety of applications, particularly those involving automation. There are varying cable designs and compounds available in the market, which highlights the question: how do you evidence consistent levels of quality in these types of cables?
Control cable certification helps you set a benchmark performance criteria and understand cable design requirements through complete cable assessments, driving cable reliability and offering peace of mind to specifiers, installers and end users.
Let’s look at the top reasons as to why you should always use approved control cables:
– Consistent braid density: control cables featuring a braided screen, such as CY and SY cable type, are assessed to ensure a sufficient number of spindles are used to demonstrate an adequate filling factor. You can, therefore, be assured that the braided screen will provide appropriate mechanical protection for the cable once installed.
– Confirm electromagnetic performance: to determine screening efficiency, electromagnetic performance, known as EMC, is measured by transfer impedance testing, specific to CY control cables in accordance with BS EN 50395. This helps to enable the reliability of transmitted signals to support efficient operation.
– Consistent insulation thicknesses: the insulation diameter within control cable products can vary greatly in the market, when not approved by a third party, which impacts cable performance. Certification outlines the parameters required for insulation thicknesses, setting consistent measurements that products must adhere to.
– Benchmarked quality: certification drives market standardisation, therefore in choosing BASEC approved products you can be assured of consistent quality across the range of approved manufacturers.
– Independent, third party testing: approved control cable products are rigorously tested by BASEC, within specialist cable testing laboratory facilities. Evidence conformity to the control cable specifications developed by the BASEC team of technical experts and access live approval certificates on the BASEC website and certification App.
– Ongoing surveillance: once certification is awarded to a manufacturer ongoing surveillance, in the form of routine audits, is undertaken to determine that the cable continues to perform, meets the specification and quality requirements.
– Comprehensive testing approach: gaining certification requires that cables undergo an all-inclusive testing programme to evaluate a complete range of characteristics. Testing includes flex, mechanical, material, constructional, electrical and fire resistance. You can be assured that approved products have been assessed thoroughly and ensure performance will be maintained across all relevant conditions.
– Insulation and sheath testing in accordance with EN 50363 series: full material testing is conducted to monitor these components within a comprehensive assessment schedule. This helps to evidence that the materials used provide suitable, long-term durability.
– British standard incorporation underway: the dedicated BA specifications developed by BASEC are being assessed to formalise the in-depth control cables certification.
– Peace of mind: assurance that by specifying and installing BASEC approved control cables you can prove your compliance to cable industry recognised quality standards that will also meet your project quality criteria. Why risk your reputation by using non approved products?
To be confident of quality always buy approved control cables, which have been independently assessed by BASEC, to safeguard your projects and end applications.
Get more details about control cable certification on the BASEC website.