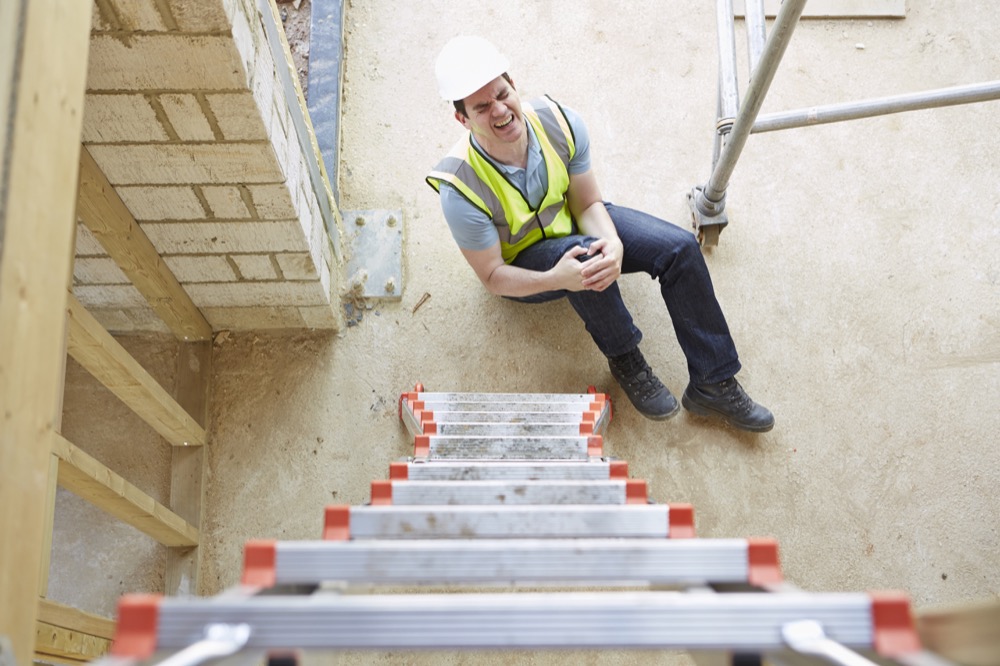
Paul Reeve, Director of Business Services at the ECA, provides a guide to contractor risk assessments.
Risk assessments and method statements are the lynchpin of higher-risk contractor activity in particular. Two basic types of risk assessment are often used, or asked for are ‘quantified’, giving a number that indicates the level of risk when carrying out an activity, or ‘qualitative’, expressed as ‘low’ or ‘medium’ risk. Either of these two types of risk assessments (RA) can be based on the following eight principles:
Step 1: Understand the activities required for the task/job/project
The starting point for any RA is to understand what the task/job involves. Put another way, what are the activities required for the job?
Step 2: What are the hazards associated with these activities?
Consider:
• the relevant hazards (‘hazards’ are the potential causes of significant harm); and
• who could be harmed, and how?
Step 3: Prioritise the hazards
When you have considered the various hazards linked to this activity, decide which hazards are the most significant (that is, which hazards could lead to significant harm). If you don’t do this, you may end up with a large list of insignificant hazards.
Step 4: Control measures to reduce the risk of harm
The ideal way to reduce risks is to eliminate as many significant hazards as possible, but if eliminating a hazard is not an option, you will need suitable risk controls to address the significant hazards associated with the work. If you don’t have suitable risk control measures in place, the risk of harm (to operatives or others) will be too high.
So, consider what control measures you will need. There is a wide range of control measures, and depending on what you are doing, these might range from permits to work, to safety barriers, site instructions or protective equipment. You might need to use several types of control measure at once, in order to control the overall risk.
Step 5: Identify your general risk controls for the activity
You are likely to have some general approaches to reducing the risk from the hazards you have identified. Note these first.
Step 6: Identify any further, job-specific issues
There may also be job-specific health and safety issues. Again, note these (they might range from using a new apprentice on a particular activity, to something different from normal for this type of work, such as working in a refrigeration room). If there are any job-specific issues, note what further risk controls you will use, beyond your general control measures.
Step 7: Clarify responsibility
Make sure you have identified who has supervisory responsibility for ensuring the control measures are 1) actually available and 2) actually used or followed by operatives/sub-contractors.
Step 8: Taking everything into account, assess the risk
Consider the potential for harm and the actual likelihood of harm occurring (‘likelihood x severity = risk of harm’). Consider what risk remains to people if all your required control measures are in place (the so-called ‘residual risk’). With your risk control measure in place, the remaining risk from this activity is the output of your risk assessment. It might be qualitative or quantitative, but either way, it will invariably need to be ‘low’ or better. You do not have to quantify the risk (put a number on it), though some buyers may ask you to do this.
Decide if the residual risk is sufficiently low. If not, then you need to re-visit what you are doing to control the risks from this activity, until it is. Your risk assessment, which can be general or job-specific, can then be used by a team, and/or passed to a main contractor or client etc.
Method statements
An activity-based risk assessment can then form the basis of a safety ‘method statement’, also known as a ‘safe system of work’. Note that a risk assessment is not a safe system of work – but it leads to it.
A method statement should be able to tell a team, and others, what measures are needed to ensure health and safety during the activity in question. Key features of the method statement are a description of how the work will be done safely, by implementing the control measures identified in the risk assessment, in addition to essential information such as the required PPE, training and emergency measures.
The eight basic steps above represent just one approach to higher risk contractor RA, and other ways may well be acceptable. Developing RA and method statements can be confusing and time consuming, especially for SMEs, and so to help its members the Electrical Contractors’ Association (ECA) has developed e-RAMS (electronic risk assessment and method statement).
The e-RAMS service, which is designed specifically for contractors, was developed from working closely with clients, ECA members and others to produce general guidelines and concise risk assessment and method statement templates.