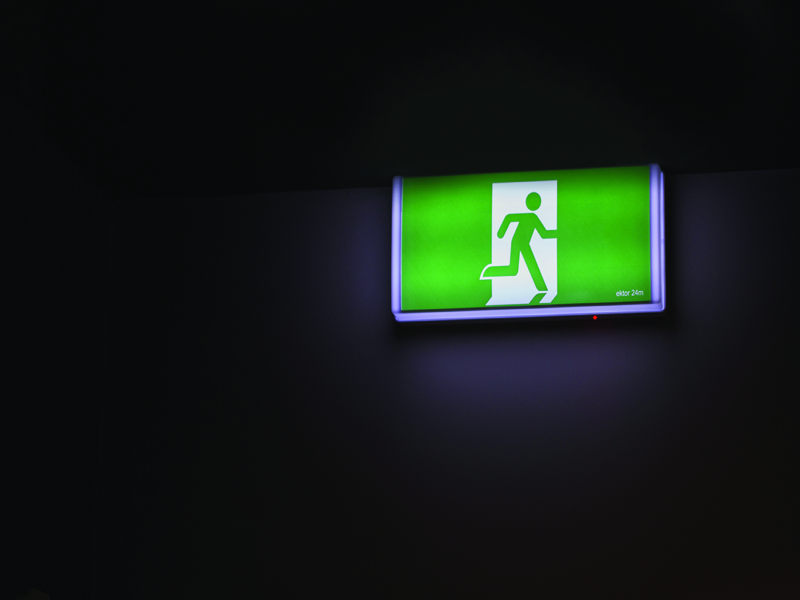
Amanda Speight, Business Development Manager at CFE Lighting, explains how emergency lighting systems are evolving and what this means for installers.
Emergency lighting – whether standby lighting which enables normal activities to continue in the absence of illumination from the mains power supply, or emergency evacuation lighting which includes escape route and open area lighting – is an essential element of health and safety provision.
Fully functioning emergency lighting is required in virtually every commercial and public building, not to mention high-occupancy buildings. And yet, sub-standard or outdated emergency lighting systems – which could lead to inefficient evacuation, bringing about injuries or even deaths – are all too commonplace in the UK.
As well as risking injuries or death, business or building owners also face prosecution and a heavy fine if they’re found to have inadequate emergency lighting in place, with one private landlord in Lincoln recently receiving a record £400,000 fine.
There are other financial consequences too; insurance companies can use non-compliance with fire safety legislation as a reason for not paying out, and that’s before we even consider the reputational damage that a business may suffer. Emergency lighting in a building can quickly fall out of compliance due to damage, lack of testing or maintenance, and evolving legislation.
And right now, with so many offices and shops finally reopening after a long period of closure, it’s more important than ever that systems are properly checked and maintained to ensure they’re working effectively.
This presents a real opportunity for electrical contractors across the country, so now’s a good time to share a few key points that should be helpful to those electricians working with emergency lighting over the coming months.
1. Have a plan
Knowing exactly what emergency lighting is required and where it needs to be placed is vitally important. Emergency lighting systems’ classification is often based on how the emergency light has its power supplied. Units will either be self-contained (single point) or central battery source.
It’s all about choosing the right system for the environment it’s being installed in, though we’re starting to see a trend in end users opting for central battery systems over self-contained units. While self-contained units are faster and cheaper to install, battery life is limited to a few years and testing requires the isolation and observation of individual luminaires, which can be problematic.
Central battery systems, while more expensive, make maintenance and routine testing far easier, with only one location to consider. Additionally, the life of a battery can be anything between five and 25 years, dependent upon type.
2. Know your standards
Emergency lighting is covered by a series of interdependent British and European standards and it’s important you’re familiar with these. Two of the most relevant are the BS EN 1838 Lighting applications which specify the illumination, colour and duration to be provided by emergency lighting, and BS EN 60598-1, which outlines general product requirements and testing recommendations.
3. Invest in quality systems
By investing in a quality, British-made system, you’re not only supporting UK manufacturers such as CFE Lighting, but you’re also giving yourself and your customers peace of mind for the future.
View the latest CFE Lighting brochure by clicking here