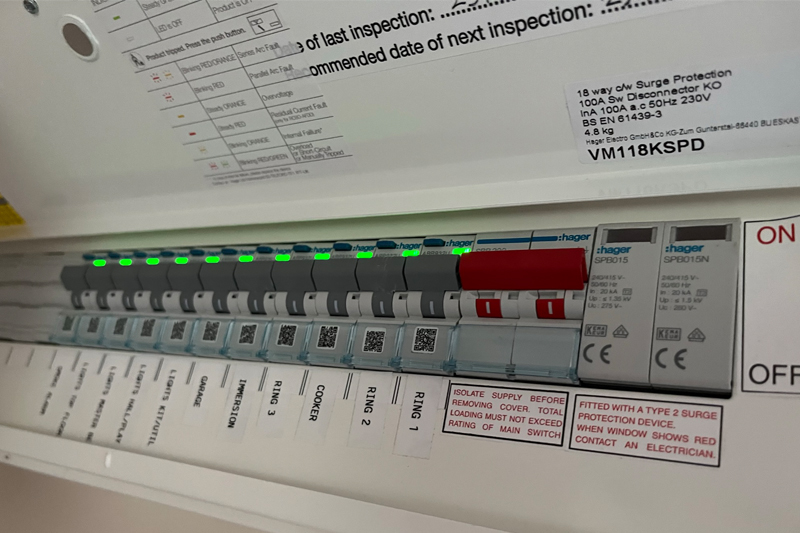
Following the launch of Hager’s new single module RCBO AFDD, we discover how the unit performed in a real-life domestic scenario.
Utilising existing feedback from over 5,000 two-module-wide units and an additional field trial with 300 single module devices, Hager’s new Arc Fault Detection Device (AFDD) with ProTools diagnostic software benefits from extensive field trials to guarantee best-in-class performance.
Real-life feedback
Offering real-life feedback from these installations, Hager was able to modify the algorithm to accommodate new product signatures prior to market launch to provide installers with the ‘fit and forget’ reassurance they’ve come to expect from Hager products.
Participating in the trial, Hager’s very own Country Marketing Leader, Ian Smith, had the latest single module device installed in his home.
With the property already benefiting from a Design 30 consumer unit installation, Hager’s technical team was able to upgrade the unit to include the new single module RCBO AFDD.
Typically, Arc Fault Detection Devices would be installed on socket circuits. However, for trial purposes, Ian’s Design 30 unit was fitted with an AFDD on each circuit, consisting of 5 x 6 A, 2 x 16 A and 4 x 32 A devices, that could be monitored throughout the trial, enabling device trips to be quickly detected and identified.
Unwanted tripping
Benefitting from the ProTools diagnostic software, the device quickly identified a fault on the 32 A device controlling the circuit connected to Ian’s garage. With ProTools – Onboard Diagnostics, the device detected a Series Arc Fault, with the LED display identifying the fault via a series of red and yellow sequences on the device indicator.
Following close monitoring of the circuit, the cause for the trip was quickly identified due to its repetitive nature; the same equipment, used at the same time of day was causing the device to trip. The cause behind the tripping was identified as Ian’s plug-in EV charger.
Upon charge completion and when attempting to disconnect from the vehicle, the electrical signatures generated by the charger caused a trip in the AFDD. In order to analyse the signature and update the algorithm within the AFDD, a trace box was fitted to record the circuit and waveform as the fault occurred.
Updating the software
With the trace of the circuit and waveform recorded, Hager’s technical team utilised this information in order to analyse the traces of the waveform. In doing so, this enabled the team to modify the algorithm, ensuring the AFDD was no longer susceptible to unwanted tripping when Ian’s vehicle disconnected from the charger.
After modifying the software, technical experts attended the site and, using the ProTools In-Situ Software Upgrades via the Hager Pilot App, were able to connect to the AFDD at Ian’s property using Bluetooth technology to send the updated algorithm to the device.
Following the software upgrade within the device, the unwanted tripping caused by Ian’s electric vehicle charger has since been resolved. This new algorithm has now been incorporated in the software in all Hager single module RCBO AFDDs and MCB AFDDs as standard to ensure that customers have the right tools at their disposal.
To browse the Hager single module RCBO AFDD bitesize guide, click here