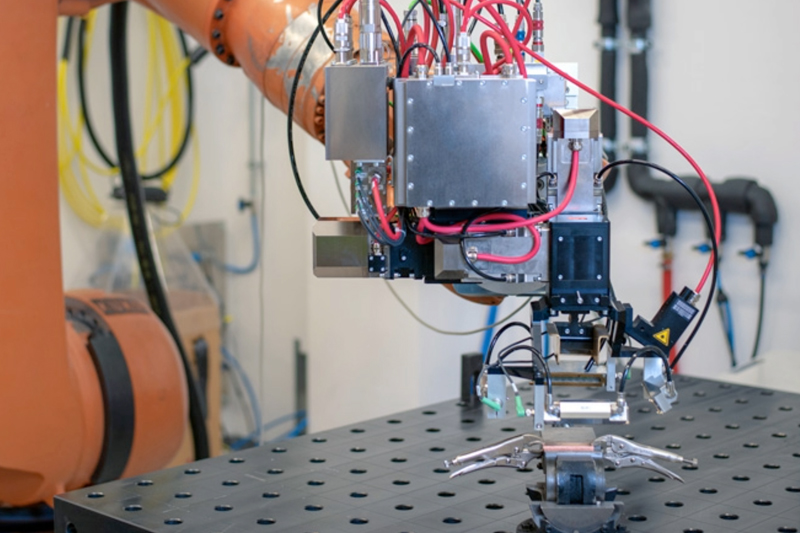
How can new technologies and ideas improve product quality, efficiency and output? The team at HELUKABEL provide us with a glimpse into the world of smart manufacturing.
Our HELUKABEL production site, based in Windsbach, Germany, was already at the height of modernity. But, now, it’s gone even further in the smart manufacturing journey.
The decision to add a collaborative robot (cobot) into the production of high-performance cables is one of many on the road to multi-faceted optimisation. Efficiency, production, agility, safety, sustainability, quality control, and savings – each is a pillar of smart manufacturing that robotic innovations continually improve upon.
Efficient production facilities
For years, robotics have been the solution to enhancing productivity and precision. The by-products of this include reduced production costs and increased output.
By powering up on the latest innovations in robotic technology, we maintain our ability to meet demands while focusing on the safety of our staff and the sustainability of our business.
HELUKABEL’s Project Lead, Peter Bluhm, explains: “Manually handling (cable) spools was not only monotonous but made keeping up with increasing production speeds exceptionally difficult. With the new cobot, our teams operating the braiding machines can work more ergonomically and efficiently, so we can save a lot of time and effort.”
State-of-the-art robotics
The story of robots in manufacturing is a familiar one. In the early ’60s, it was General Motors that integrated the first robotic device into an assembly line. Since then, strides in robotic innovation have paved the way for widespread adoption.
Today, industrial robots have a firm place in smart manufacturing. They’re one of the core components of fully integrated production systems with real-time response rates to changing conditions and global demand.
As these devices face constant evolution, they become more efficient, more precise, and more cost-effective across various industries. They’re no longer only suitable for the General Motors assembly line; they’re omnidirectional.
A decision on cobots
With approximately 15 categories of manufacturing robot in the modern market and thousands of specifications within each, the move to integrate a cobot in HELUKABEL’s production facility was highly deliberated.
In our mission to administer smart manufacturing processes, we carefully considered our existing processes and wider goals. For example, Peter Bluhm highlighted the monotony of spool movement; the ergonomic challenges staff faced could have led to the development of chronic pain.
Then, there are human speed limitations that robotic arms bypass. Finally, there was the need for the robotic integration to work in the same space or “cell” as our staff without risk of injury.
While we already have a fleet of robotic technologies operating throughout our production, testing, and warehousing facilities, the specific spool movement process required something new. Hence, the cobot.
This robotic device is designed to work alongside humans and ensure they don’t cause harm when they come into contact. For example, they feature lightweight materials, rounded contours, padding, sensors, and defined speed and force thresholds.
Powering robots with high quality cables
Our ranges of ROBOFLEX, industrial ethernet, and BUS cables are specially designed for robotic integration with properties matching your application. For example, we designed our ROBOFLEX range with resistance to oil, abrasion, notches, welding spatters, extreme bending radii, and more.
Modern robots, like the cobot, move in 3D space within a single cell. They complete repetitive tasks with continuous precision while maintaining quality; to do this, the cables inside the robots need to meet the highest standards.
For example, they must withstand rapid acceleration, rapid deceleration, torsion, tensile loads, bending movements, and more. Some also need to withstand mechanical, chemical, and thermal factors, depending on the application.
We manufacture and supply a variety of cables for robotic applications including control and motor cables in various dimensions, hybrid cables, and cables for sensor, network, and BUS technology.
Level up with HELUKABEL cables
HELUKABEL offers custom robotic cable solutions as well as free application assessments to ensure you receive tailor-fit cables. We’re also able to provide pre-assembled and ready-to-install systems that increase the protection your cable has across its service life.
Browse the HELUKABEL range of cables here
Find more industry feature articles here