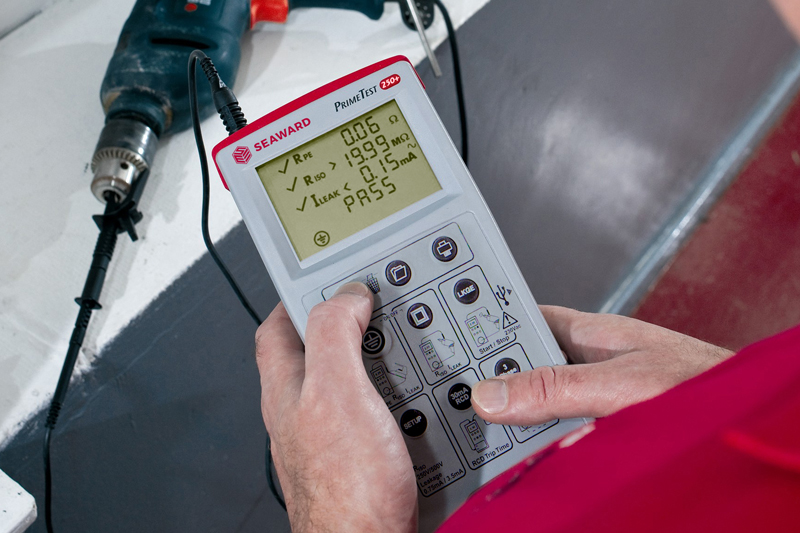
Darren Bakewell, Applications Engineer at Seaward, answers questions from professional electricians looking to carry out PAT tests for their customers’ or their own electrical tools and equipment.
Should I be PAT testing my power tools, and how often?
Working in the electrical sector as we do, we see the need for electrical safety every single day. But even some of us who know what should be done, don’t ensure the safety of the electrical equipment we’re responsible for; electrical equipment should be maintained in a safe condition. Through regular inspections, relevant tests and the keeping of records we won’t only reduce the risk, but also have proof that inspections have been carried out.
Most portable power tools can be tested with a standard Class I or Class II test, depending on the unit itself. Don’t forget to inspect any cordless tools, such as battery powered drills. Although the units themselves may not require testing, they have safety related components, such as guards, which can be checked at the same time. The frequency of the inspection and test should be based on a suitable and sufficient risk assessment and, of course, the battery chargers that connect to a power source require inspection and testing to be carried out in line with the risk assessment.
Should I be testing 110V transformers? And how?
The 110V transformer has 230V input voltage and carries risks like any other piece of equipment.
Providing the 110V Class I transformer has passed a visual inspection, plug the transformer into your PAT tester and make a connection to earth via the transformer socket outlet, using the test probe. Turn your PAT tester on, and carry out a Class I test to take the transformer through earth continuity, load, insulation resistance and alternative leakage tests. If it passes, apply your label.
Don’t forget to test all sockets on the transformer and plug an appliance into each socket to make sure they’re working correctly. It’s also worth remembering that 110V tools need to be inspected and tested in line with the risk assessment and that adaptors can be used to connect them to a tester that may not have a built-in 110V socket.
Should I offer fixed appliance testing? How easy is it to carry out a fixed appliance test?
Due to the competence required to safely isolate the supply to the fixed equipment and the higher charges being levied for testing fixed appliances, when compared to equipment connected by plug and socket, the professional electrician might find this an attractive service to offer.
The starting point for testing fixed equipment must be a thorough risk assessment. The inspections and tests that are carried out on fixed equipment are the same as those used for equipment connected by plug and socket, but the key challenges are in the areas of safe isolation and connection to the test equipment.
Once safely isolated you can then carry out a full visual inspection as detailed in the IET Code of Practice 4th Edition. Once visual inspection has been passed, make a temporary connection between the equipment and the PAT tester (best practice would be to use a point-to-point tester). Make sure the correct test connections are in place and there is no risk of shock during the test.
Seaward’s PrimeTest Series is ideal for electricians who aren’t testing hundreds of appliances at a time, but need an easy-to-use, accurate PAT tester that can easily handle power tools and 110V transformers.
To download a copy of Seaward’s ‘Guide to PAT Testing’ practical guide, click here.