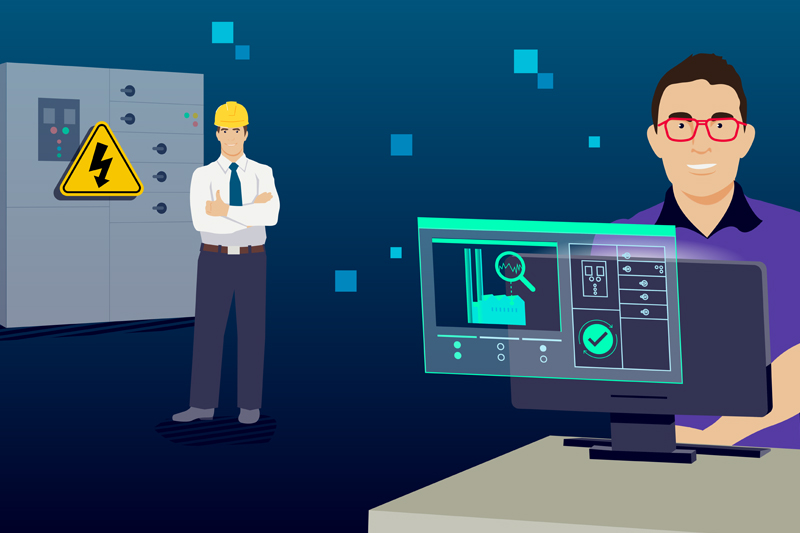
When it comes to power supplies, how many outages can you afford? Wolfgang Christ, an expert at Siemens Smart Infrastructure Electrical Products offers some key tips for electrical planners and operators.
Power cuts paralyze many businesses and can endanger human lives. On average, customers of distribution network operators (DNOs) in the United Kingdom experience power outages totalling about half an hour per year. But did you know that high equipment availability can be planned and financed?
It can be, if operators know their needs, plan for them in good time and implement them cleverly. Not every operation needs the highest availability down to the decimal places required by data centres. It’s all about learning how to make an electrical infrastructure resilient and fit for the future with a sense of proportion – and how to prevent human error.
No one can completely prevent power outages. But it’s important to know how much availability a business really needs and plan a demand-orientated electrical infrastructure that the operator can afford. Three points are particularly important here: determining the actual demand, adapting the electrical planning accordingly, and implementing it efficiently.
Determine demand
To find out how readily available equipment needs to be, electrical planners and their customers – the operators – need to work closely together. The electrical engineering, procurement, and construction companies (eEPCs) responsible for the installation should also have a say in this process.
For 2021, the online statistics platform Statista indicated an average power interruption duration between 29 and 51 minutes per customer in Great Britain, including planned and unplanned power cuts. Customer minutes lost were lowest for the Western Power Distribution network, while Scottish and Southern Electricity Networks had the highest number of minutes lost, at 51.4. The data was provided by the DNOs.
The German Federal Network Agency reported an average power cut duration of about 12 minutes per end user in Germany. Forty percent of these are unplanned and therefore avoidable power outages. Local outages are added to that. An operator must therefore be quite clear on one point: how many power outages (and the downtime that comes with them) can you afford?
Know the risks: power outages are the most common cause
Answers to this question vary. Data centres, for example, require a very high 99.999 percent system availability. After all, an outage here can cost £500,000 or more – per hour! Particularly interesting here is that problems with the power supply were the most frequent cause of failures in data centres last year, accounting for 44 percent of the total – and the trend is upward.
This was documented in the Global Data Centre Survey 2022 conducted by the New York-based Uptime Institute even though data centres invest in particularly extensive protective measures compared to other industries. At the same time, costs per failure are rising due to the growing global dependence on data.
Imagine you’re in a shopping centre when suddenly all the lights go out. The cash registers don’t work. Panic can break out. Visitors who experience such an event might well avoid that shopping centre in the future. In addition to the high downtime costs, an outage like this can cause enormous damage to the image of the shopping centre operator – damage that can’t be measured in monetary terms.
In critical infrastructures such as hospitals, human lives depend on the reliability of the power supply. Not least because of this fact, and in view of the current energy situation, the British government established a new Department for Energy Security and Net Zero Energy in February of this year. It focuses on long-term energy security and compliance with the UK’s carbon budgets and net-zero commitments.
Plan a reliable and available system
These examples show that we must do something to increase availability, especially in low-voltage power distribution systems. The good news is that something can be done, by planning equipment availability. But how do you actually achieve this?
If the scope of required plant availability is determined early in the planning phase, a holistic electrical design must be based on this factor. What you miss in electrical planning, you can’t make up later. I like to put it this way: If the first button doesn’t fit, the whole shirt is crooked. It’s therefore important to minimise the risk of man-made mistakes.
Use proven methods
For electrical designers, this means continuing to rely on proven methods. These include redundancies, selectivity, evaluation, and measures against external influences in combination with preventive maintenance. With these methods, you can achieve a high degree of availability in an electrical power distribution network. However, such work is expensive, since it entails more complex planning, additional operating resources, and increased space and maintenance requirements.
Added to this are costs due to the shortage of skilled workers and supply bottlenecks when failures occur. Assessing a fault, repairing it, and putting the system back into operation usually requires specialist know-how. The critical question is: are specialists and required spare parts available at short notice?
Implement digital solutions
Various digital solutions can complement this proven approach. Cybersecurity and communication capability are fundamental requirements here. Self-monitoring intelligent components, for example, detect impending malfunctions before failures occur. In addition to facilitating preventive maintenance, this enables operators to employ systematic ‘condition monitoring’.
In addition, planners can use intelligent end-to-end software including automatic and standardised interfaces for planning and execution processes that simplify the exchange of data between different programs.
Rely on high-quality technology
I like to emphasise two cost levers that are well-known yet have somewhat lost their prominence over time.
The first lever is high-quality, robust products. Cheap but often inferior goods increase the risk of failures and higher operational costs. If you buy cheap, you generally buy twice – and you run the risk of bearing high damage costs.
Secondly, experts also rely on high-quality and proven withdrawable and plug-in technology for quick repairs or conversions. Time is money and every lost minute can cost a fortune. If damage is unavoidable, it’s a matter of repairing it quickly and easily to safeguard operations. That’s where it can be very helpful if an auxiliary staff can also carry out repairs and the operator doesn’t have to wait for a specialist.
Promote know-how transfers
In addition, buildings these days are increasingly intelligent and will make high demands on electrical planning. No one can handle this planning alone, and there’s a growing risk that humans will make mistakes in the process. That’s why I think it’s extremely important to share our knowledge – and share it across company boundaries.
The Uptime Institute also cites “improving planning and training” as one of the “most effective and cost-efficient ways to reduce downtimes” in data centres. In fact, this applies to all industries. Putting effort into this area is particularly worthwhile, especially when you consider the high risks of power supply outages and their rising costs.
Free webinar
Siemens is taking a lead on this by providing free webinars. Our latest offering – Equipment availability can be planned – Tips for electrical planners and operators – provides practical information for electrical planners so they can reduce downtimes by ensuring optimised, needs-based electrical planning everywhere, especially in critical infrastructures, while at the same time limiting investment costs for their customers.
Taking place on May 8th, myself and my colleagues Natalia Marques and Thomas Grupa will be available to answer questions from all interested parties during the free live webinar.
Get more details and register for the webinar by scanning the QR code or visiting here