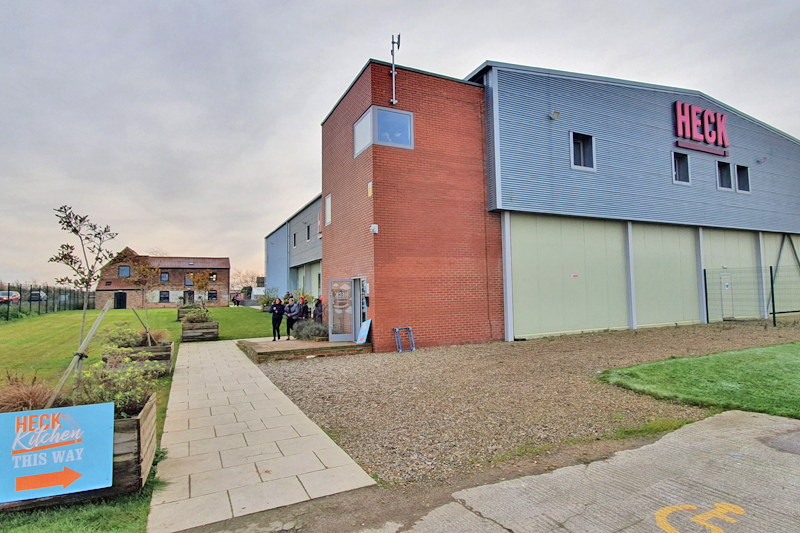
ITV viewers were recently given a glimpse inside the Heck Food factory as part of the channel’s Made in Britain series. Red Arrow look back on creating the factory’s energy saving LED lighting design.
Project: Design and supply LED lighting for Heck Food Factory, York
Contractor: Steve Betteridge
Lighting design and products: Paul Yarnell, Red Arrow
The brief:
Heck Foods, a family-run food manufacturer known for their premium and vegetarian sausages, needed an LED lighting system for a production area and two storage areas in their newly built York factory.
Heck was launched by a husband and wife team, Andrew and Debbie Keeble, in 2012. In just seven years the brand has shot to fame, appearing on supermarket shelves across the UK and featuring in an episode of ITV’s Made in Britain series – but the brand has not lost sight of its roots, with all manufacturing still taking place in Yorkshire.
The installation at the new factory needed to conform to commercial Part P building regulations – including energy saving and automation – as well as provide comfortable lighting for employees working at the premises.
Designing the installation:
As a factory environment, Red Arrow needed to create the best lumen output and colour rendering possible, with the correct IP ratings for a warehouse and food production area. The LEDs also needed to be suitable to install on to high ceilings and, in certain areas, be automated to dim or switch off when the space was unoccupied.
The biggest challenge was to create a uniform light output throughout the space while limiting the number of fittings, as requested by the contractor. As a result, Red Arrow recommended installing a reduced number of higher-output LEDs, regularly spaced to avoid hot spots and shadows.
In the warehouse and cold storage areas, two different types of dimmable Linear LED Hi-Lo Bays were chosen to create a 400 lumens output: a 12100 lumen and 23200 lumen model, both IP65 rated for a factory environment.
For the main production areas, a bright, consistent lighting effect was created with 1500mm, 4000K waterproof LED Non-corrosive fittings.
Microwave sensors were also added to the warehouse and storage areas. These were set to dim LEDs to 10% when the room was not in use and, after long periods without activity, turn off completely.
Products supplied:
Warehouse and cold storage
19 X HLB3100W-60 (12100 lumen)
30 X HLB5200/60 (23200 lumen)
Microwave detection sensors
Production
1500mm non-corrosive vapour proof fitting
End result:
The project met all specifications, conforming to regulations and meeting the contractor’s commercial cost and installation time requirements, without compromising on lighting quality and comfort for those working in the building.
“Lighting in commercial premises should do more than tick the right boxes,” says Paul Yarnell, Red Arrow’s lighting designer on the project. “With this installation, we worked with the contractor to deliver a design that didn’t just meet minimum standards but created a comfortable working environment for Heck employees. Businesses are really starting to see the importance of lighting quality for workplace wellbeing and with projects like this one, we’re advising our clients on how they can achieve the best possible lighting quality and consistency within their commercial remit.”
Steve Betteridge, the contractor leading the project, was happy with the result, especially ease of install: “I was pleased to see that the fittings came with suspension wires, as with other suppliers I have had to go and buy these separately. The presence detectors are perfect, and Red Arrow created a helpful lighting scheme, which was amended to suit changes to the projects when needed. The products lived up to specification and I would definitely use these products again in the future.”
To find out more about Red Arrow, please visit www.redarrowtrading.com