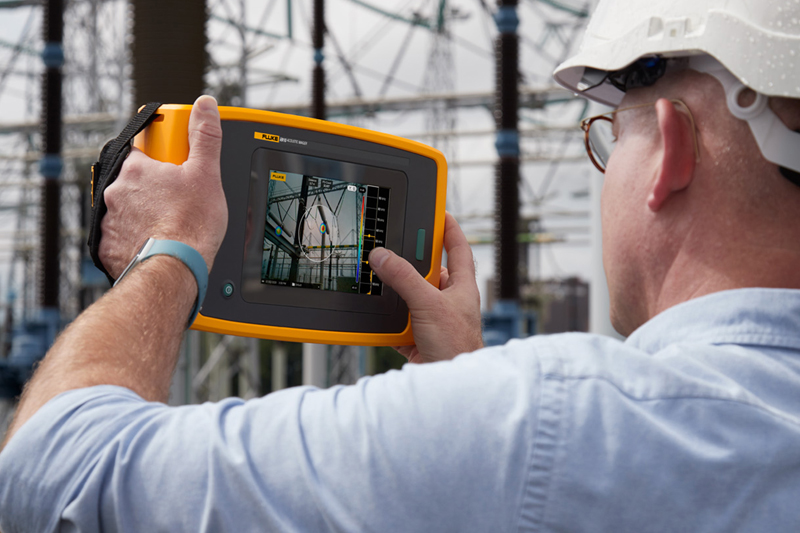
Kenter, a Dutch energy metering and management company, detects partial discharge using Fluke’s ii910 Precision Acoustic Imager to prevent the degradation of medium voltage applications which can impact SMEs and large multinational organisations
Kenter, a leading Dutch energy metering and management company with more than 30,000 customers, has transformed maintenance inspections through the fast and safe detection of partial discharge. Left undetected partial discharge can cause degradation of medium voltage installations which pose significant safety, efficiency and financial risks that are critical considerations in maintenance inspections.
Kenter is part of Alliander, the largest energy network operator in the Netherlands, and works to install, rent and maintain safe and reliable energy supplies to a wide range of businesses from small family-run bakeries through to electric vehicle manufacturers and large multinational chemical companies. Kenter offers innovative energy supply and measurement solutions to aid companies wanting to optimise their energy consumption. The company’s team of 300 maintenance specialists have greatly improved the speed and accuracy of scheduled maintenance inspections using an innovative handheld tool, the ii910 Precision Acoustic Imager from Fluke.
Managing maintenance schedules
Kenter provides 24/7 maintenance on the equipment required to deliver a safe and reliable power supply to customers nationwide. This service includes scheduled maintenance cycles which typically occur every three, five, six or 10 years. During scheduled maintenance, Kenter looks to coordinate a series of works to minimise disruptions to operations, including checking for partial discharge.
Partial discharge is typically caused by a minor defect which can result in thousands of smaller repetitive electrical discharges. The phenomenon often occurs around insulation on pieces of equipment, such as high-voltage lines, transformers, turbines, busbars and the inside of cabinets, and can impact energy supply due to mechanical, heat, and chemical damage to insulators and conductors.
Fast and accurate inspections
The Fluke™ ii910 Precision Acoustic Imager allows maintenance engineers to quickly scan a customer’s electrical assets from a safe distance whilst operational, and immediately identify areas impacted by partial discharge. The image can be quickly analysed to detect the type of partial discharge, enabling the team to undertake appropriate maintenance. Users benefit from the tool’s ease-of-use, speed and accuracy, while customers can continue operations during maintenance inspections without the need for a plant shut-down.
According to Martin Damen, Technical Engineer Manager at Kenter, Fluke’s ii910 Precision Acoustic Imager has revolutionised maintenance inspections and is a critical tool for maintenance.
“Being able to scan a whole installation in one go is a real game changer in regard to how quickly we can identify a partial discharge issue,” he said.
Dirk Kwik, Team Manager Service and Maintenance at Kenter, agreed: “Our engineers are focused on identifying issues and undertaking maintenance as quickly and safely as possible to minimise disruption to our customers’ businesses and avoiding costly unscheduled downtime.”
Benefits in application
A recent review at a customer’s site using Fluke’s ii910 Precision Acoustic Imager showed partial discharge was occurring on the switchgear installation. This had not been detected by staff as there was no distinctive smell or sound during the interim review and no malfunction issues had been reported. The customer was also reluctant to shut down operations for assessment using an oscilloscope. Failure to identify this issue could have significant consequences due to the ultimate risk of the switchgear failing. According to Damen, the cost to replace the switchgear could be in the region of €30,000 – and that’s without assessing the potential damage to the customer’s reputation, who work to tight deadlines, as a result of their business being offline.
The ii910 device has helped Kenter’s management team to deploy their workforce more effectively. More than 18 engineers are now fully competent using the ii910 with online training being rolled out to the national engineering team. The complexity of operating an oscilloscope resulted in a significantly higher amount of time required to train engineers to accurately detect partial discharge.
Innovative detection of partial discharge
The ii910 Precision Acoustic Imager was developed to help engineers quickly identify and locate partial discharges. The innovative detection tool has a seven-inch LCD touchscreen which overlays a SoundMap™ on a visual image for rapid identification of discharge or leaks between frequencies of 2-100 kHZ. The ii910 provides video recording of up to five minutes and has a battery life of at least six hours.
“The Fluke ii910 Precision Acoustic Imager was developed with the end-user in mind,” comments Tako Feron, Product Manager Acoustic Imaging at Fluke Corporation.
“A working group of electrical maintenance professionals from a range of companies helped to test and provide feedback on the product during its development. Their feedback was invaluable in helping us to address some of the pain points they face on a daily basis, and we continue to work with the group to add new features to the software.”
To find out more about Fluke’s ii910 Precision Acoustic Imager click here