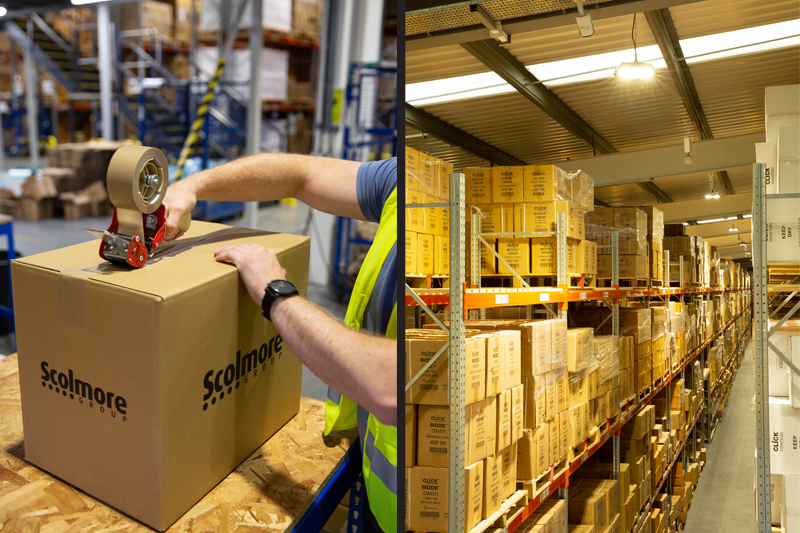
At a time when green credentials and sustainability remain high on the agenda for businesses, Scolmore is pleased to announce a number of initiatives the company has undertaken to limit the environmental impact of its warehouse operation.
One of the key aims for the business was to reduce the overall amount of packaging used in the warehouse. The first step was to review the use of all the boxes and packaging in which products are received into the warehouse. Instead of this packaging material being sent off for commercial waste recycling, it is now shredded on site and used for the subsequent packing up of products for distribution to customers.
An additional measure has seen the replacement of the original cardboard cushioning used to protect the products in boxes, with an alternative 100% recycled polymer pillow packing solution which is 80% recyclable. This has enabled the company to save the amount of protective packaging used, as well as the cost of the provision.
In a further endorsement of its green credentials, Scolmore has had confirmation that the company supplying the boxes and cardboard tubes used to package products – Sandland Packaging – has recently become the first UK sheet plant to become fully carbon neutral. According to its announcement statement, “Sandland Packaging has continued its pioneering environmental journey to become the first corrugated sheet plant in the UK to become fully carbon neutral by measuring and offsetting all carbon emissions across Scope 1 and 2 and all 15 categories in Scope 3. This means all boxes produced by Sandland Packaging are certified carbon neutral and crucially are emissions free for their customers.”
The use of plastic tape to seal up boxes was another area for consideration. As well as being less recyclable than paper and taking longer to break down, plastic tape may also rely on more complex resources and energy systems in the creation process. Scolmore now uses the eco-friendly paper tape alternative.
Commenting on the measures taken and resulting savings made, Lee Taylor, Operations Manager for Scolmore Group said: “Sustainability has been at the forefront of our operations for as long as I can remember, and we are continually taking measures to address our environmental impact. With the focus on packaging reduction, we have not only saved on the amount of packaging and waste we use as a business but have also made significant cost savings in the process. Our switch to paper tape means that we have saved 769,000 metres of plastic tape since the beginning of 2022.”
At the same time as overhauling its packaging solutions, Scolmore undertook a review of the lighting provision throughout the warehouse. This resulted in the replacement of the old incandescent light fittings with more energy efficient LED alternatives. The fittings chosen for the general warehouse areas were the Ovia Inceptor Hion 200W LED High Bay dimmable lights with microwave sensor and a total of 140 have been installed throughout the warehouse space. The microwave sensor version was selected as the best energy saving option, with lighting only being activated in areas that are occupied.
To provide energy efficient lighting under the mezzanine area of the warehouse, Ovia’s Inceptor U-Lite luminaires were chosen. Inceptor U-Lite is a slimline, non-corrosive utility LED luminaire. It features an integrated diffuser and gear tray anchored to the base, which allows for simple and hassle-free installation. A total of 15 Inceptor U-Lite luminaires have been installed, and the microwave sensor version was the preferred choice.
To find out more about Scolmore, click here