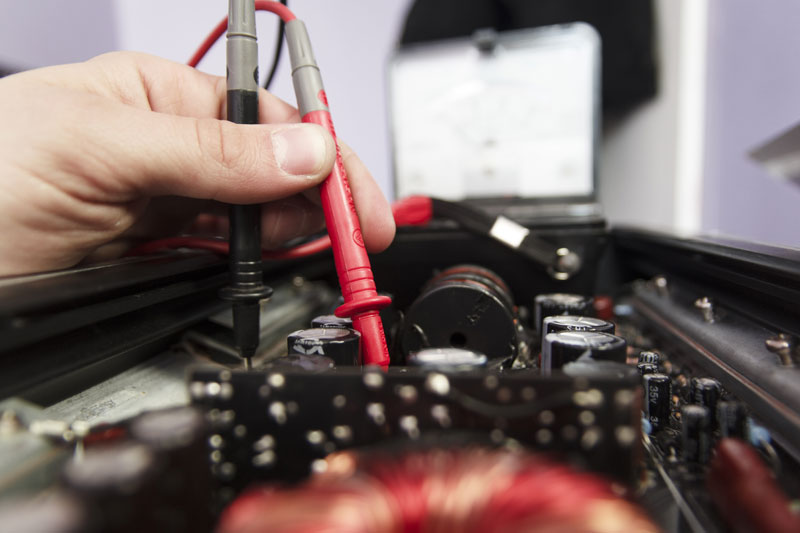
In the market for new test and measurement equipment? Steve Martin, Head of Specialist Groups at the ECA, offers some top tips to aid your selection process.
Vital to any electrical installation is testing, and contractors need to know that the equipment they’re using is reliable, safe and accurate. The industry therefore depends on having the correct procedures and equipment in place to verify the integrity of any installation.
While recent figures from the JIB and ECA show that electrical safety is now at its best since records began, there can never be any complacency. With this in mind, what are the key criteria for electrical contractors and installers when selecting test equipment?
Here are five important considerations when choosing your kit:
1. Usability
The ease (and speed) of testing when on-site remains paramount, particularly with many meters now gaining extended feature sets.
2. Toughness
Contractors should look to invest in a meter that will have a longer lifespan and can stand up to the knocks of daily use.
3. Reputation
The reality is that you get what you pay for. Using a manufacturer that provides full UK support (including technical, repair and calibration) provides assurances, while a full warranty with the product
offers extra guarantees.
4. Safety
Contractors should look for equipment which conforms or exceeds health and safety requirements, particularly given that pre-qualification requirements are becoming more comprehensive over time.
5. Whole life value
The running costs of the tester needs to be considered alongside the purchase price – its physical and electrical robustness are important factors.
“It’s also worth noting that the rise in new connected technologies, such as smart meters, electric vehicles and smart homes, means that contractors need to be aware of any additional regulatory requirements which may apply.”
Taking these steps will ensure that contractors use equipment which helps meet the requirements of building managers and clients, who are themselves becoming more aware of the need to utilise appropriate test equipment.
For instance, when it came to portable appliance testing, Carillion facilities management team running HM Winchester Prison realised the advantages of identifying all individual electrical appliances and other equipment using barcodes, allowing for the correct data to be stored automatically against each item as inspections are undertaken.
The FM services manager at Winchester Prison, Jeff Foster, notes that there is a ‘considerable time saving in being able to identify items, carry out tests, record results and make any notes as part of a fully streamlined process.’
It’s also worth noting that the rise in new connected technologies, such as smart meters, electric vehicles and smart homes, means that contractors need to be aware of any additional regulatory requirements which may apply.
As a result, installers will need test tools which have greater functionality and enable different tasks to be undertaken, particularly given that these technological advances increase expectations among clients for faster testing, and enhanced record keeping, among other requirements.
Here to stay
What remains clear is that contractors will always need testers. Given that the market is highly competitive and innovative products are now widely available, this leaves contractors in a strong situation. With manufacturers competing to deliver high quality products which provide clients with the solutions they need, contractors just need to consider the advantages and disadvantages of each product.
By following the five key steps outlined in this article, contractors will be in an ideal position to make such judgements on the range of test equipment available to them.