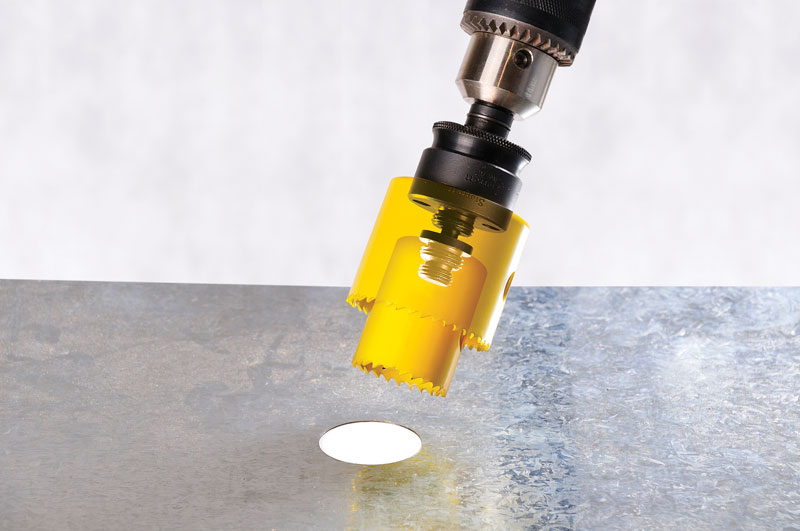
The rapid advancement of the materials and technologies in our homes poses challenges for tradespeople fitting new projects and refurbishing existing buildings. Here, John Cove, Marketing Manager at L.S. Starrett, looks at the top five hole saw hacks that can make these jobs a breeze.
1. Cutting porcelain tiles
The hardness of porcelain tiles makes it very difficult to cut using a simple tile cutter and porcelain tiles are also more prone to chipping during the cutting process.
When a job requires cutting holes to fit a tile around cables and pipes, or fittings need to be attached to a tiled surface, always use a hole saw with a diamond-grit coated tip. The diamond coating will easily cut through porcelain, glass, ceramics, brick and stone without chipping or breaking. When accompanied with proper water-cooling, you will be left with a clean cut and smooth surface finish.
2. Hole enlargement
Fitting 75mm downlights into the 50mm holes left by the previous lights presents a problem. In this case, consider replacing the pilot drill with a hole enlargement arbor. The arbor can be fitted with a hole saw that has the same diameter as the existing hole – this acts as the pilot – as well as a larger diameter hole saw, allowing the larger diameter to be cut in one single motion.
3. Cutting thick steel
A tool breaking unexpectedly is frustrating, yet rarely happens out of the blue. Cutting steel is a perfect example of the long-term wear on a tool that can lead to a sudden break. Although regular hole saws will do the job, cutting thicker steel can cause the tool to become hot, quickly increasing wear on the cutting surface and significantly reducing product life.
When cutting thicker steel, consider using a carbide tipped hole saw designed specifically for deep cutting of steel up to 25mm thick. This operates at a higher speed for a faster cut, preventing the saw from getting hot and wearing down.
4. Cut out unpleasant fumes
Composite and engineered wood, including medium-density fibreboard (MDF) provides a versatile, lightweight and strong building material. However, cutting it can produce really unpleasant fumes. The density of the fibreboard can cause the hole saw to heat up, potentially melting the glue adhesive in the composite itself.
When drilling MDF, engineered and composite woods that contain adhesives, as well as plastics and plasterboard, consider using a tungsten carbide tipped multipurpose hole saw. This will deliver cutting speeds that are up to five times faster than a typical bi-metal hole saw and the rapid cut will build up less residual heat, giving less time for the adhesive to reach a melting temperature.
5. Dust and debris
Although maintaining a clean working environment is a habit of all good tradespeople, it is inevitable that most jobs will produce excess dust and debris that needs to be cleaned up afterwards.
When sawing or cutting using a hand held power tool, a debris collector attachment that can catch the dust and debris created during the cutting process can make things so much simpler. Not only is this quicker it also eliminates the need to mask high-risk areas prior to sawing or cutting and prevents the ingress of dust and debris into your power tool’s motor housing.