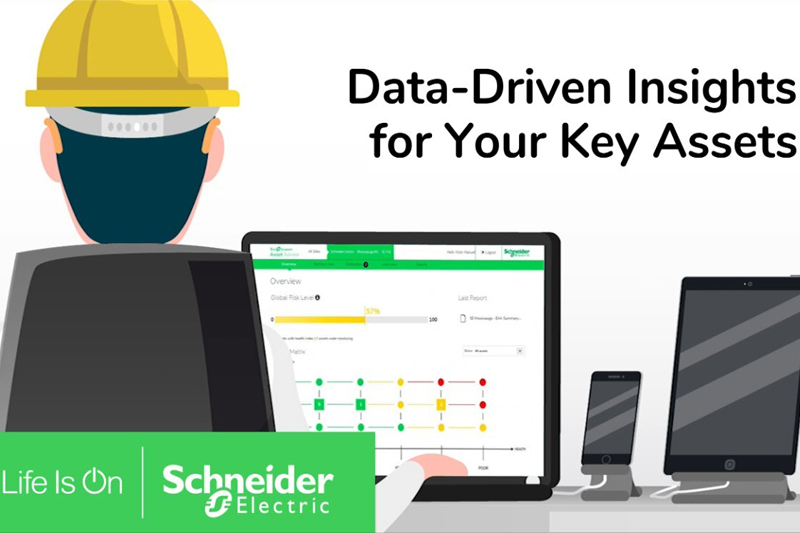
Schneider Electric, the leader in the digital transformation of energy management and automation, is launching new condition monitoring aimed at preventing up to 25 million electrical motor failures each year. EcoStruxure™ Asset Advisor for Electrical Distribution and Rotating Equipment, designed for any critical rotating equipment, such as motors, compressors and pumps, is a gamechanger with the ability to reduce downtime by an estimated 15 hours per week and boost productivity.
The failure of rotary manufacturing equipment can have a significant impact – 7% of rotating equipment failures lead to frequent and unplanned downtime and decrease production capacity by 5% per year at a severe cost to manufacturers. The average manufacturer suffers of equipment downtime, which equates to 15 hours per week and millions of pounds in losses.
Advanced monitoring for maintenance
EcoStruxure™ Asset Advisor (EAA) allows users to monitor equipment remotely for condition-based maintenance and safety. Data is fed into sophisticated cloud-based analytics tools and powerful digital insights help anticipate issues before machinery breaks down. In this way, potential electrical failure risks, unplanned downtime, operational losses, and the need for expensive maintenance interventions can be avoided.
MSCA:
The end of vibration analysis
The EAA platform uses Motor Current Signature Analysis (MCSA) in place of traditional vibration monitoring. MCSA has a number of key advantages which include:
- Cloud-based analytics: this powerful digital data allows the MCSA to detect percentage levels of upcoming failure, with minimal false positives.
- Ability to work in harsh environments: the new system is installed within control cabinets, not on the motor, which eliminates the potential of malfunctioning due to harsh environments.
- Identifying mechanical & electrical issues: In addition to measuring mechanical issues, data is provided on power functions and energy consumption providing the potential for energy saving and performance optimisation insights.
The science behind MCSA technology
Once installed inside the motor-controlled centre, the MCSA starts its learning phase and, through expert analysis, understands the system’s frequency patterns. This process takes around 2-6 weeks allowing the machine detect anomalies that may occur over time.
After the testing phase has been completed, the asset advisor is live 24/7. The system monitors and sends notifications when issues and potential failure modes are detected. Typically, months and weeks before failure occurs. This early detection and reliable warnings provide accurate condition-based solution methods.
“Schneider’s new EAA will help alleviate common electrical and mechanical failure risks that lead to unplanned downtime,” said John Flynn, Smart Factory Business Development Manager at Schneider Electric”. Once the analysis equipment has conducted its learning phase, anomalies and warnings provide the user with crucial data which they can act on. This, therefore, allows critical machinery to be repaired or replaced before failure”.
For further information about EcoStruxure Asset Advisor, click here