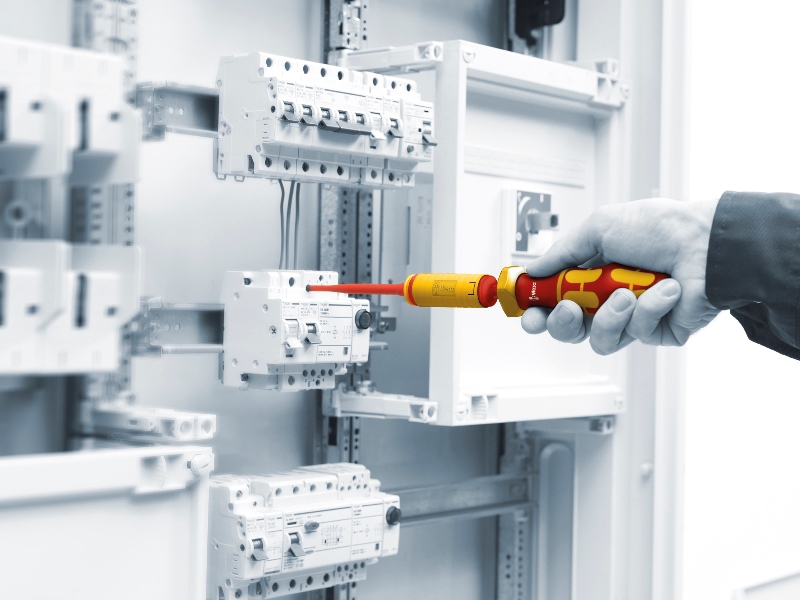
Caroline Crossland, from Wera, considers the importance of using high-quality torque screwdrivers to comply with Amendment 3 to BS7671 IET Wiring Regulations.
Regulation changes in the electrical industry can be met with confusion, doubt, and even distrust. Hard-working tradesmen having to shell out for another printed copy of the ‘regs’, and potentially feeling strong-armed into going on a tools and equipment shopping spree, often aren’t in the most receptive frame of mind.
There are few industries, however, where safety is so crucial. For an invisible, silent force, electricity packs a serious punch – when things go wrong, the consequences can be deadly. It is with this in mind that the electrical safety bodies must continually research and investigate standards, accidents, and developments within the marketplace. Then it is down to the IET, working with the BSI, to refine, remove or expand on the Wiring Regulations as necessary.
When they were amended in 2013, they stated that wherever electrical equipment manufacturers provided guidance regarding installation, it must be followed (134.1.1). Specifically looking at consumer units, this meant that if a torque value for a screw connection was specified, it must be adhered to. So to ensure conformity, a calibrated torque screwdriver must be used.
This wasn’t spurious ‘change for the sake of change’. Both over- and under-tightened connections can cause problems – those not tight enough can of course lead to hotspots and arcing, while over-tightened screws can damage the component, for example, deforming a terminal cage. All these high-resistance connections can over-heat, potentially causing the outer casing of the consumer unit to reach sufficient temperatures to ignite – an easy trigger point for a devastating fire.
Poor workmanship?
The IET found fire investigator reports of blazes originating in consumer units were growing in number, particularly those with thermoplastic enclosures. The cause was almost invariably found to be poor electrical connections, poor workmanship or lack of maintenance, including:
- Failure to tighten neutral conductor connections to the same torque as line conductor connections, due to a misconception that they carry less current
- Failure to check factory installed connections for tightness where required to do so by the manufacturer
- Tightening connections to an incorrect torque and/or with inappropriate tools
In a video interview with IET Chief Engineer Geoff Cronshaw, London Fire Brigade Investigator Charlie Pugsley said that the main fault that they had come across leading to the ignition of consumer units was loose connections.
The IET say “…the crucial importance of checking that all electrical connections are properly made, and of taking remedial action where necessary, should never be forgotten.”
Wera supports this view. Conforming to 134.1.1 cannot guarantee there will never be problems with over-heating (for one thing, high resistance connections can never be 100% eradicated), and there are a number of other issues electricians feel the safety bodies should be looking into urgently, but it is certainly an important step towards achieving higher safety standards.
So to ensure your work conforms to Regulation 134.1.1 (which was tweaked in 2015 by Amendment 3, but essentially remains the same), what do you need to do? You need an adjustable torque screwdriver. Unfortunately, consumer units can feature screw connections requiring up to five different torque settings, so fixed torque screwdrivers aren’t a viable option. You are strongly advised, of course, to use a properly certified VDE tool (conforming to EN60900:2012 – meaning each tool is tested in a water bath for safety at 10,000V, guaranteeing safety at 1,000V).
Better tools
When Regulation 134.1.1 was introduced there weren’t many options on the market, and those that were available weren’t realistic options for frequent, regular use – incorporating several separate component parts, and requiring disassembly and use of a special tool each time you needed to change the torque setting. These awkward, cumbersome tools represented a bygone era.
Of course, manufacturers were busy working on better solutions. The Kompakt VDE Adjustable Torque screwdriver from Wera was one – and remains a fantastic option in 2016. No special tools or disassembly are needed to change the torque setting, and it is compatible with the top-selling Kompakt VDE range of interchangeable blades. Being so quick and easy to change the torque setting, it’s ideal for installation of consumer units, with their multi-torque setting screw connections.
When choosing a torque screwdriver it’s important to do your research – user reviews and the knowledge of retailers can help to guide you to the ideal product for you, and don’t be afraid to contact manufacturers direct.
For Wera, the Kompakt VDE Adjustable screwdriver has proved hugely successful, and they are working with key players in the electrical industry to help spread the word about safer working. They are particularly focussed on working with colleges, and are again sponsoring the Sparks ‘Apprentice of the Year’ competition and associated ‘Meet the Lecturer’ events.