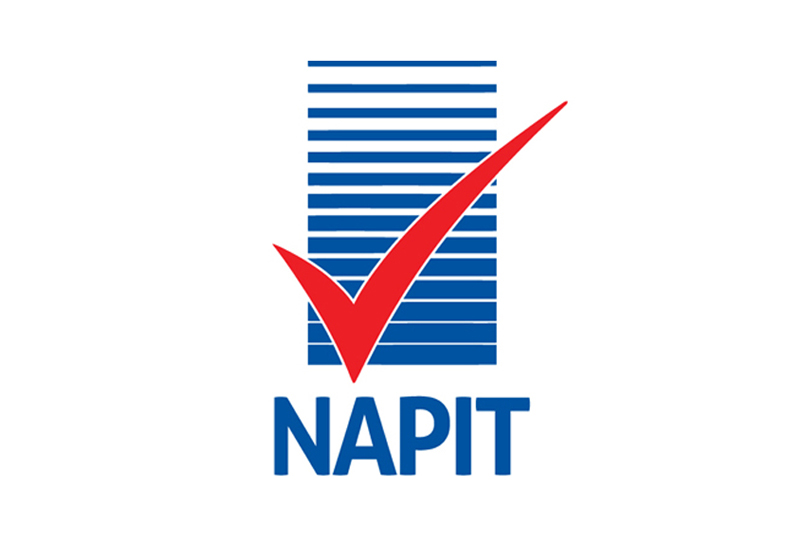
Frank Bertie, Managing Director at NAPIT, discusses bonding issues and extraneous-conductive-parts in electrical installations.
Bonding requirements of BS 7671
Whenever we have discussions, whether received on the NAPIT Technical Helpline, at NAPIT EXPO events, or on the NAPIT webinars, they normally involve main and supplementary equipotential bonding in all types of premises.
This article will examine the bonding practice in general and the requirements in BS 7671 for main equipotential and supplementary bonding.
So, what is bonding?
As we all know, bonding and earthing are not the same thing. Although the same green and yellow conductors are used in earthing and bonding, we should be aware that their functions are fundamentally different. The two are as different as chalk and cheese.
In BS 7671 Part 2 where the definitions are listed, earthing is defined as follows:
• Connection of the exposed-conductive-parts of an installation to the main earthing terminal of that installation.
It should be noted that bonding is not covered in its own right within the definitions, but the term ‘Bonding Conductor’ has been listed as ‘a protective conductor providing equipotential bonding’.
So, this leads us to ‘Equipotential bonding’, which offers a fuller explanation of the function of bonding, which is defined as follows:
• Electrical connection maintaining various exposed-conductive-parts and extraneous-conductive-parts at substantially the same potential (see also Protective equipotential bonding).
The use of protective earthing and protective bonding in electrical installations is one of the most widely used methods of giving protection against electric shock from the metalwork of an electrical installation that has become energised ‘LIVE’ due to the development of a fault.
This method is called Automatic Disconnection of Supply, which is abbreviated to ADS, and is described in Regulation 411.1:
(i) basic protection is provided by basic insulation of live parts or by barriers or enclosures, in accordance with Section 416; and
(ii) fault protection is provided by protective earthing, protective equipotential bonding and automatic disconnection in case of a fault, in accordance with Regulations 411.3 to 411.6.
As a simpler method of describing this, bonding is the process of connecting the metalwork associated with an electrical installation with metalwork that is not associated with an electrical installation with green and yellow protective conductors of appropriate size.
Such metalwork defined in BS 7671 as exposed-conductive-parts are integral to the electrical installation and include the metal casings of equipment, such as containment, distribution boards and a range of appliances. This would also include accessories such as metal switch plates and metal socket outlets but would not extend to non-metallic accessories with metal screws.
Where we have other metalwork, which is defined in BS 7671 as extraneous- conductive-parts, that would consist of metallic water pipes, gas pipes and ducting. A protective zone The objective of equipotential bonding is to create an area or zone within an electrical installation where there is a single voltage throughout (voltage was formerly known as potential). A person receives an electric shock by touching or being in contact with two different voltages at the same time.
It is this difference in voltage which causes an electric current to flow through a person, resulting in the person experiencing an electric shock.
The requirements for carrying out equipotential bonding seek to remove or at least to minimise voltage differences within the electrical installation by creating an equipotential zone within those areas. In simple terms, equipotential means one potential or one voltage. Therefore, it is evident that protective conductors used for earthing serve the purpose of carrying fault current.
Equipotential bonding conductors serve the purpose of providing protection by ensuring that all of the metalwork is of approximately the same potential.
Main protective bonding
Main bonding, or to give it its full title, main equipotential bonding, is required to be carried out on all metallic services and structures that fall within the BS 7671 Part 2’s definition of extraneous-conductive-parts, as shown in Fig 1.
BS 7671 Regulation 544.1 outlines the requirements for main protective bonding generally, with Regulation 544.1.1 specifying the conductor sizes for the main protective bonding.
Table 1 shows these requirements regarding the cross-sectional area (csa) of the main protective bonding conductors when linked to the sizing of the main earthing conductor for TT/TN-S systems.
In determining the csa of the main protective bonding conductors, we need to consider the type of supply, since there are differences between TT/TN-S and TN-C-S systems.
Although the reliability of TN-S systems cannot be assumed to be purely separate earths in the current situation, the csa of the main protective bonding conductors in TN-S systems should follow the requirements for TN-C-S as shown in Table 2.
There are different options for the installation of main equipotential bonding conductors where they can be separately installed to each extraneous-conductive-part, several examples of these can be seen in Fig 2.
Alternatively, they can be connected as a continuous main protective bonding conductor from the main earthing terminal to each extraneous-conductive-part without a break in the conductor.
As per Regulation 544.1.2, all main protective bonding connections shall be made as near as practicable to the entry point to the premises.
This also applies to the installation of meters, where the connection, where practicable, should be within 600 mm of the meter outlet union.
Conclusion
When sizing, installing, connecting and locating the main protective bonding conductors, it is imperative to consider the requirements of Regulation 544.1 in the design process.
For more information on NAPIT scheme registration, click here
Find more industry technical articles here