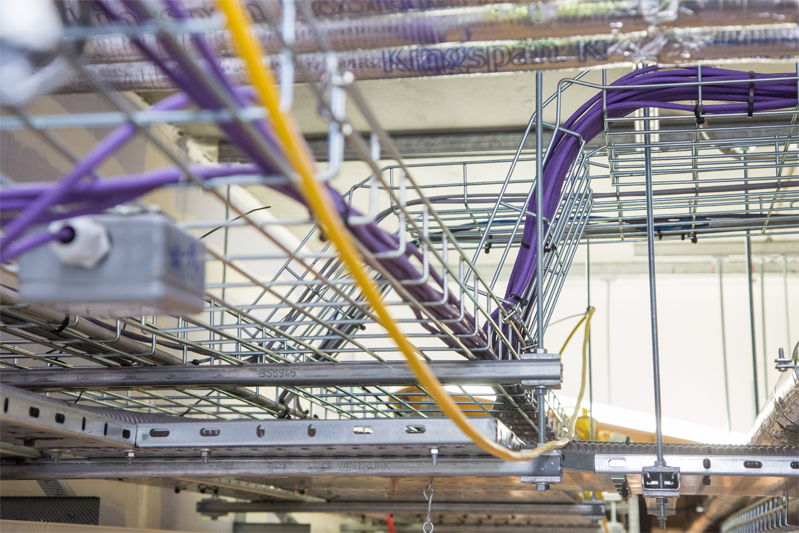
Tim Brown, National Sales Manager at cable management specialist, Unitrunk, shares insights from the company’s CPD on compliance and specification best practice.
When you consider the complexity of the cable management compliance landscape, it’s not surprising that electrical professionals aren’t always familiar with each and every requirement. That it said, it should be understood that these standards underpin safety and longevity, so due diligence when assessing the compliance of a cable management system is vital to the integrity of the finished installation.
As part of the Construction Products Directive (CPD), CE marking is necessary for all cable management systems to the relevant BS standards, as outlined in the table below:
Raw material | BS EN 10346: 2009 |
Stainless Steel material | BS EN 10088-2:2005 |
Trunking | BS EN 50085-1:2005, BS EN 50085 – 2-1: 2006 |
Underfloor Systems | BS EN 50085-2-2:2008 |
Cable tray, ladder & basket | BS EN 61537:2007 |
Cable ladder & tray | IEC 61537 |
Channel & support systems | BS6946 |
Installation standard | BS7671, IEE Wiring Regulations |
In addition to these mandatory standards, it is also advisable to specify a cable management system that has been manufactured to the highest quality assurance standards in an ISO 9001-2008 accredited production facility. Additional approvals, such as London Underground (LUL) also provide confirmation that the chosen cable management system is safe and robust, particularly with reference to fire protection.
Cable ladder and tray systems must also comply with the IEC 61537 international standard, which involves a wide array of testing from the manufacturer, the results of which must be available to specifiers and installers. These tests may include load testing for the containment and the bracket, including point load and SWL (safe working load) and flex testing of brackets under load. Corrosion resistance of the fabrication material may also need to be tested along with DIN 4102-2 E90 fire resistance.
Short circuit testing does not form part of the requirements of IEC 61537 but provides visual evidence of how the system performs under fault conditions. Similarly, shock testing visually indicates the level of impact, vibration and distortion the product will cope with.
Early engagement
Over-specification can be just as problematic as under-specification when it comes to cable management, potentially leading to wasted materials and lost value engineering opportunities.
Early engagement with the cable management manufacturer can help to avoid oversights in quality and compliance and help the specifier to reduce material costs and installation times, based on credible test data. For example, Unitrunk’s 60/300 EasyConnect RIS cable basket can carry 58kg/m at 1,500mm fixing centres. Consequently, rather than fixing the basket at 1,200mm centres for a 1,000m run of containment (as many specifications would advise), we would suggest installation at 1,500mm centres. This reduces the number of brackets required per 1,000m from 833 to 667. If we assume that each bracket is installed at a cost of £10 for materials and 20 minutes of labour (@£30/hour), equating to an installed cost of £20/bracket, this simple change of specification will save around £3,320 across the 166 brackets removed from the specification, representing a saving of £3.32 per metre!
Engagement with the cable management manufacturer can also help to identify practical steps that can be taken to aid ease of installation, thereby improving performance, while reducing labour costs. For example, both pendant and cantilever brackets allow the cable management and the cables to be installed more quickly, with no obstructions. The manufacturer may also be able to indicate the most appropriate size of cable tray or basket for the project by considering the installation challenges holistically. For example, cable basket can be formed to match the bending radius of the cable and the manufacturer can advise on specifying less material and fewer brackets.
The specifier should always interrogate the usual assumptions about what may be required, questioning, for example, whether cable ladder can be substituted for cable tray and whether cable tray can be switched to basket. It may also be possible for trunking and conduit to be substituted for basket, as well as reducing the amount of containment needed by using multi-compartment solutions.
A recent Unitrunk project involving the specification for a high-tech manufacturing environment demonstrates the value of early engagement in developing the specification. Here, rod and channel trapeze brackets had been specified at 1,200mm centres but we revised the specification so that the ladder system became the bracket and containment and the trapeze components were replaced by suspension wire. By doing this we were able to achieve the minimalist aesthetic the client wanted while satisfying the consultant’s performance criteria and helping the contractor to save 20% on both materials and labour.
Manufacturers’ advice on selecting the correct finish for the specific installation environment can also be invaluable. While standard pre-galvanised cable management is sufficiently robust for most indoor installations, specialist environments with increased risk of corrosion from humidity or contaminants, outdoor installations, coastal locations and specialist considerations such as the risk of zinc whiskers in data centres, may require more robust materials.
Learning through BIM
Manufacturers are also feeding into the drive for best practice design methodologies by ensuring suitable data is available in BIM design software. The 3D visualisation facilitated by BIM enables design teams to fully manipulate cable management layouts on screen to develop the optimum specification configuration before the project reaches site.
For information about the range of cable management products available from Unitrunk visit: www.unitrunk.co.uk