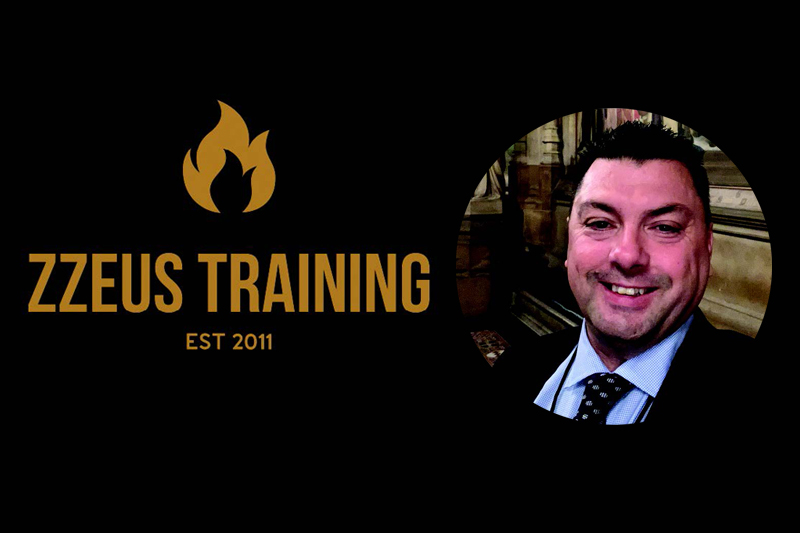
In this regular column, ‘Dr Zzeus’ Tom Brookes, MD of Zzeus Training and chairman of the FSA, will answer your questions related to fire safety compliance. This month’s covers inspection periods and processes…
Q. We’ve just changed fire alarm service companies to save money in the current climate. When I questioned why the new company was not testing voltages, batteries, and some other checks at the six-monthly service that the old company did, they said the old company were doing too much testing and that what they were currently doing met the standard. Is there a checklist of what should be done?
It sounds very much like the new service provider either does not know the standard or is trying to get away with not completing a service correctly. BS 5839-1:2017 Clause 45.3 covers the six-monthly inspections, and 45.4 covers the yearly inspection. I have listed the minimum checks that should be carried out at the six-month visit; your provider can do more than this, but not less.
Changing suppliers entirely based on price can be a wrong move; for a fire alarm company, the most expensive part is the employees’ wages, so cutting the price down often involves the engineer doing less, cutting corners or missing parts of the service.
1. Review the system logbook for recorded faults and ensure appropriate action has been taken.
2. Visually inspect for any structural or occupancy changes affecting compliance with the standards:
a. Check unobstructed and visible manual call points and any new fire exits that have been created have a manual call point adjacent to exits that lead to a place of “Ultimate safety”.
b. Assess any new partitions or ones that may have been moved within 500 mm of automatic fire detectors.
c. Ensure no storage encroaches within 300 mm of ceilings.
d. Check clear space (500 mm) below automatic fire detectors.
e. Evaluate the suitability of existing detectors for changed areas.
f. Check additional fire detection and alarm equipment that may be needed for alterations or extensions.
3. Check false alarm records, note the rate in the past 12 months, and take appropriate action.
4. Measure battery voltage with mains power on, ensuring it aligns with manufacturer recommendations before other tests (without additional load).
5. Disconnect the standby battery, activate alarms, and verify the power supply output voltage close to the nominal value. Simulate full load if necessary (minimum 95% nominal voltage).
6. Inspect batteries and connections and load test without mains power.
7. Test fire alarm functions of the Control and Indicating Equipment (CIE) using at least one detector or manual call point per circuit. Record devices used in the logbook.
8. Confirm the fire alarm signal upon at least one manual call point or fire detector operation.
9. Verify proper operation of CIE controls and visual indicators.
10. Check the automatic transmission facility for alarm signals to an Alarm Receiving Centre, ensuring the correct transmission of each signal type.
11. Test all ancillary functions of the CIE.
12. Where feasible, check fault indicators and circuits through simulated fault conditions.
13. Test printers for functionality and legibility and ensure sufficient consumables until the next service visit.
14. Service all radio systems as per the manufacturer’s recommendations.
15. Perform additional checks and tests recommended by the manufacturer for the CIE and other system components.
16. Report any remaining defects to premises management, complete the system logbook, and issue an inspection and servicing certificate.
Do you have a question you’d like answered? Email your queries to: Tom@Zzeus.org.uk