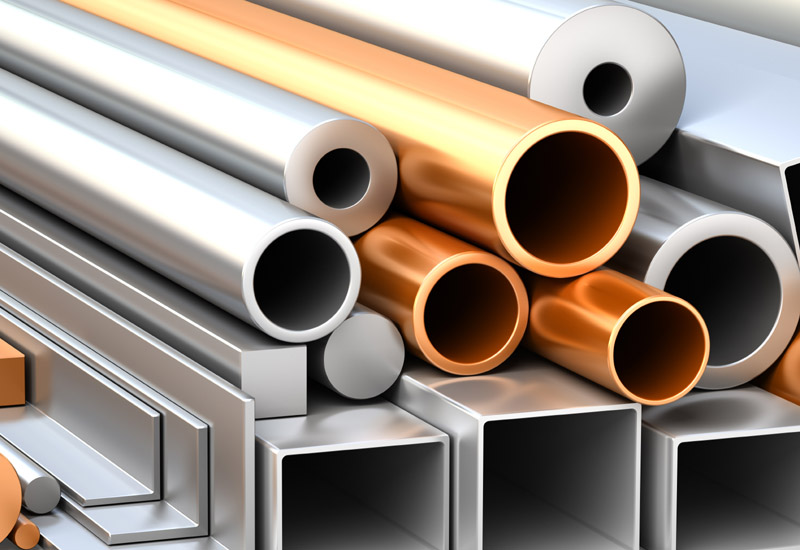
The ECA’s technical team offers its best practice guidance when joining copper-based electrical equipment to aluminium.
The following guidance note is designed to offer advice when working on and with electrical equipment of dissimilar metals that are to be connected, or joined together.
BS 7671
BS 7671 The Requirements for Electrical Installations doesn’t go into any great detail on this subject. Regulation 522.5.2 states: “Dissimilar metals liable to initiate electrolytic action shall not be placed in contact with each other unless special arrangements are made to avoid the consequences of such contact.” BS 7671 offers no additional advice or guidance on this matter.
As there are thousands of different materials available, it would be unrealistic to consider the best practices for each pair in this document, therefore the focus will be on the joining of copper to aluminium.
Generally copper is the default metal for conductors, however there are cases in which the use of an aluminium conductor is a viable alternative. Aluminium weighs much less than copper and can be easier to form, though some restrictions do apply. Table 52.3 of BS 7671 limits the use of aluminium cables to be no less than 16mm2 cross sectional area. Aluminium cables are often found on high voltage ring mains where they’re likely to be terminated onto a copper bus bar in the substation, though they can be used on low voltage installations too.
Smaller aluminium cables may be found within existing installations that were installed in the early to mid-1970s. This was common practice due to a copper shortage at the time. These cables can’t be classed as ‘dangerous’, however any alterations involving them should be carefully planned and the appropriate accessories will be needed.
The issues
Aluminium is a material that can oxidize easily, that is to say it reacts with oxygen: when it comes into contact with the atmosphere, a thin but highly resistant oxide barrier is formed. This oxide layer is an effective insulator and must be removed at any joint.
When joining metals that are dissimilar, the addition of water creates an electrochemical reaction between the copper (anode) and the aluminium (cathode), causing the aluminium to corrode. Thus, when connecting copper to aluminium, it’s vital that moisture isn’t allowed in contact with the two conductors.
The type of crimp required would depend on the nature of the joint i.e. aluminium cable to copper bus bar, aluminium to copper cable etc. If the connection is to be buried in the ground, then an appropriate enclosure filled with resin should be used.
Aluminium cables come in four main varieties, and these are:
1. Round solid conductor
2. Sector solid conductor
3. Round stranded conductor
4. Sector stranded conductor.
Prior to attempting to join cables, it’s essential that the correct crimp is available and that the correct crimp tool is used. Excessive pressure or the incorrect tool will result in ‘over’ compression or ‘under’ compression, both of which can cause the cable joint to become damaged and weak.
It’s also important to know the cross sectional area of the conductor(s), as aluminium has a larger cross sectional area than the copper equivalent due to aluminium having a lower conductivity than copper.
This can be seen from the tables in Appendix 4 of BS 7671, where comparing table 4D1A (single-core 70˚C thermoplastic insulated cables, non-armoured, with or without sheath – copper conductors) with table 4H1A (single-core 70˚C thermoplastic insulated cables, non-armoured, with or without sheath – aluminium conductors): a 50mm2 single phase conductor clipped direct carries 182A when made of copper but only 125A when made of aluminium. Indeed, to get an equivalent aluminium current carrying capacity you need to increase the cross sectional area to 95mm2, which has a current carrying capacity of 195A.
When joining copper and aluminium cables, a special compound is usually provided with the cable lug which aggravates the thin oxide layer on the aluminium, effectively removing the layer and resulting in a better electrical connection and greater conductivity. This compound also helps to reduce the chance of oxidisation further down the line.
Conclusion
Joining of copper and aluminium cables is commonplace in many elements of the electrical industry and, if done properly, should pose no more danger or threat than any other electrical joint. Use of appropriate crimps, tools and joints/resin (where necessary) will help to ensure a solid and reliable connection is made.
Consideration should also be given to the terminal that the connection will be made into to ensure that any connection between aluminium and copper is done in the appropriate fashion.