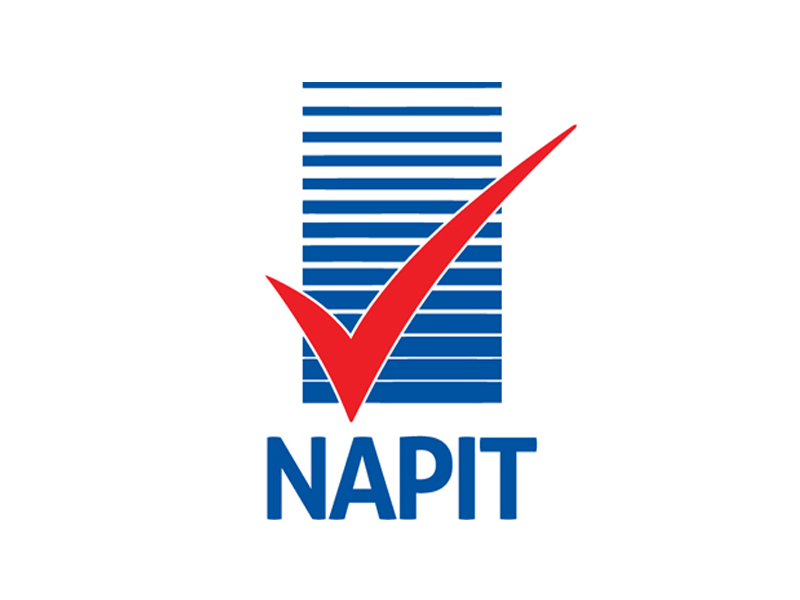
In the first of a two-part series of articles, Technical Events Manager and Technical Author of NAPIT On-site Solutions, Paul Chaffers, takes a closer look at some of the important design considerations for cable ladder and tray systems.
In some of our recent articles for Professional Electrician, I’ve looked at installation requirements for conduit and trunking systems. In this article, we take a look at cable ladder systems and cable tray systems. Ladder and tray systems differ slightly from conduit and trunking systems in that they are not enclosures, and they do not provide mechanical protection, only cable support. This means that the installation of non-sheathed conductors is not permitted as this would breach Regulation 521.10.1, which requires non-sheathed cables to be enclosed. Consequently, only cables where mechanical protection is provided by a suitable sheath, for example, PVC sheathing or steel wire armouring, can be used in conjunction with ladder and tray systems.
Structural considerations
Often, cable ladder or tray systems are installed to carry only light cable loads. As they are generally of steel construction, this is usually enough to carry the load without too much concern (providing suitable supports are in place). The cable tray is available in different widths and heights, where information on levels of deflection can be obtained directly from the manufacturer. Deflection is the degree to which a structural element is displaced under a load and can be reduced by the correct positioning of supports. Where heavy cable loads are expected, a cable ladder system often provides a superior solution and greater flexibility as it can be built and mounted in virtually any position.
Ladder systems also minimise the number of supports needed due to the sheer strength of their design, meaning they can span greater distances between supports. It is not uncommon to find a mixture of both systems that cater to different wiring routes and cable loads throughout a building. Although very similar in looks, cable ladders should not be confused with actual ladders used to gain access. Cable ladders should never be climbed or walked on as this may cause personal injury, damage to the cables, or the system itself – see Fig 1 for clarification. When fixing supports to the structural elements of a building, such as steelwork and beams, it is important to check that they are able to carry the additional load. This may involve consultation with the building designer, depending on the proposed load bearing requirements.
Channel support system
Steel channel (strut) forms the basis of many wiring containment support systems. Struts are usually available with plain or slotted bases in profile sizes 41 x 41 mm or 41 x 21 mm and formed from either 1.5 or 2.5 mm thick steel.
The main components consist of:
- Steel channel sections (struts)
- Channel nuts
- Set screws
- Steel brackets
Channel nuts are provided with either long springs, short springs, or no springs to suit different applications, usually with M10 or M12 threads. It is essential that channel nuts are tightened to the manufacturer’s recommended torque setting and the set screw is the correct length. It needs to screw completely through the nut (which is typically 6 mm to 8 mm thick).
However, set screws used for this purpose must not be too long; otherwise, they can bottom out on the channel before the screw head tightens down on the fitting. These individual component parts can be seen assembled in Fig 2, and their overall versatility is illustrated in Fig 3 as a completed system.
Trapeze hangers
Trapeze hangers can be used with either tray or ladder systems consisting of threaded rods hung from the support channel. Alternatively, suitable ceiling or beam clamps may be used as appropriate, as in Fig 4 and Fig 5. Where there are multiple levels of tray or ladder hung on the same rods, it is important to ensure that the safe working loads of the threaded rods and associated components are not exceeded.
Conclusion
Hopefully, in this first part, the article has highlighted a few areas of design that require care and attention to get right. Considering the sheer weight and complexity of cable ladder and tray systems, it is recommended to consult directly with manufacturers’ technical guides to obtain the required information to complete a safe and satisfactory installation.
* NAPIT would like to thank Legrand for the source material used in this article
For more information on NAPIT scheme registration click here