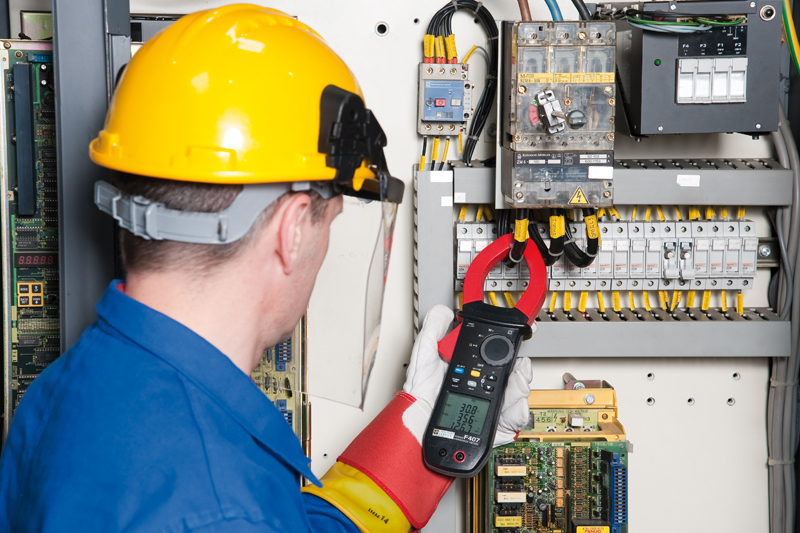
In this article Julian Grant, General Manager of Chauvin Arnoux UK, will look at one of the most important, but often overlooked, parameters associated with electrical installations big and small.
In simple terms, the ‘Maximum Demand’ of an electrical installation is the maximum amount of current it is ever likely to draw from its supply. This is expressed as a current in Amps in most cases, such as on EICs and EICRs, but for some installations it may be specified as a Power value in kilowatts or kVA.
Maximum demand is addressed in Part 3 of the Wiring Regulations (Section 311), which states that for economic and reliable design of an installation the maximum demand shall be determined. This is an interesting, but important, use of these two terms and illustrates the balance that must be struck.
Installing a huge supply that isn’t needed will not be cheap (economically) but installing a small supply when you know it will be inadequate will not be reliable. So, essentially, the electrician is tasked with determining the correct demand and then specifying the smallest supply capable of reliably delivering this. The important point, though, is how?
Determining maximum demand can be achieved in many ways and each method has its pros and cons. What they all have in common is that the more data you have about the installation and its usage the more accurate the final figure will be.
Before we look at the methods available to us, it’s worth adding a quick note on what we must avoid. Superficial and basically incorrect methods like just writing down the main fuse rating or simply adding up the current of all the MCBs are not based on the installation usage and are a sure sign that the electrician stating them has little idea what maximum demand is, or how a fuse works for that matter.
Given that maximum demand is based on gathering data about the installation and its usage, the Wiring Regulations also introduce the idea of ‘diversity’, and state that this must be used when determining maximum demand.
Artificially high maximum demand
Diversity is the concept that not all circuits will be fully loaded at the same time, and if they are it will likely only be for a very short time. It’s a sort of averaging effect and is the reason why just adding up all the MCB ratings is a bad idea, as it fails to consider diversity, resulting in an artificially high maximum demand.
The method used often depends on the point at which the determination is being made, i.e. is it a design for a new installation before construction, before an addition or alteration to an existing installation, or is it to evaluate the suitability of the supply, maybe as part of an EICR?
For a completely new installation we will have to rely heavily on calculation, using diversity values from Table A2 in the IET On-site Guide, or figures chosen by the designer based on their assumptions about how the installation is to be utilised.
Calculation is, however, likely to be less accurate than measurement-based methods, and as with all design assumptions it is recommended that these are checked by measurement after the installation is complete. This will confirm that they were indeed accurate within the tolerance required.
When assessing additions, alterations and existing installations we have the option to carry out measurements to determine the maximum demand with a greater degree of accuracy. This is achieved by measuring the current (or power) consumed by the installation.
This could be a single ‘spot’ reading taken with a clamp meter at the origin of the installation, but that will only show the current at that moment. It is unlikely to represent the maximum and doesn’t show the full picture of demand over time.
The solution is to use a Power and Energy Logger, or PEL, which can log current and voltage over a given time – say a day, week or longer, dependent on the installation. The PEL will record the installation current throughout this period and can be set to also record other parameters such as power and even harmonic content.
This will give the designer a clear and highly detailed view of the usage of the installation which can be used to assist in determining the true maximum demand. Where micro-generation, such as PV, is installed a PEL can also allow you to factor this into the maximum demand.
The current log shown with this article (below) is typical for a 3-phase industrial installation and was performed over a week. The current can be seen to peak at about 250 A. Such detailed information enabled the designer to make an informed judgment about the maximum demand of this installation, with the PEL data and graphs to back up their decision.
It is hard to imagine in a modern installation how this level of analysis could be achieved by calculation alone, making a PEL an almost essential piece of kit for all electricians.
Browse Chauvin Arnoux’s latest test and measurement brochure here