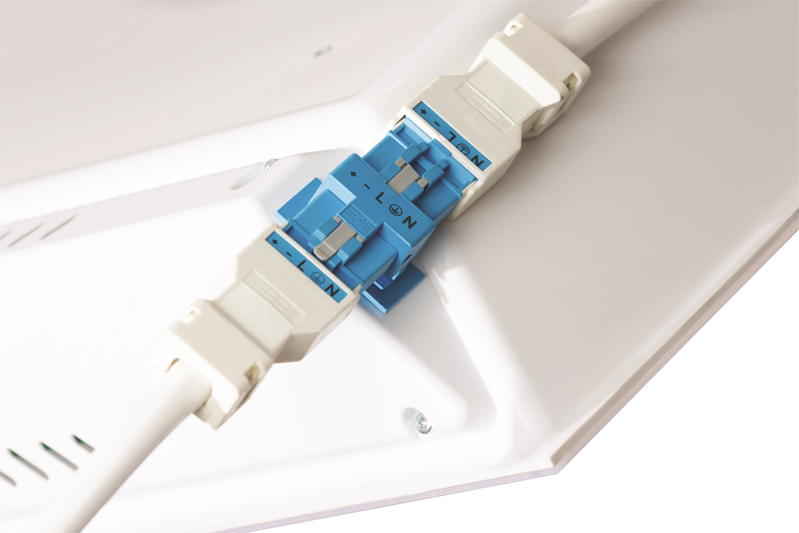
David Draper, Interconnection Product Manager at WAGO, debunks a few of the myths surrounding modular wiring.
Modular wiring is an increasingly popular solution for commercial installations. Pre-wired assemblies are delivered to site ready to be plugged together without the need for extensive wiring work. This can reduce installation time by up to 70% compared to traditional hard wired systems, while reducing errors and improving safety.
Despite the benefits of modular wiring, some installers are still reluctant to embrace them fully, perhaps because they’re not fully aware of the benefits. In truth, modern modular wiring has improved so much in recent years that these concerns no longer apply.
MYTH: The cost is too high
While modular wiring costs more to purchase compared to traditional hard wired systems, the difference is recovered by the quicker installation time on-site and, therefore, the lower labour costs. Colour-coded plugs and spring pressure connections ensure that wiring errors are avoided.
Qualified electricians are still required to supervise and carry out final wiring and checks, but plugging connectors together is a task than can be deskilled if required, further reducing costs. Indeed, spending all day up a ladder tightening screws can be tedious and tiring.
Freeing up skilled electricians from repetitive wiring tasks to work on other, potentially more complex and/or lucrative jobs is a more efficient use of labour which can help a project reach completion more quickly.
Overall, modular wiring can reduce installation costs by up to 30%, whilst also freeing up valuable time for contractors to be deployed on other jobs.
MYTH: They are unreliable
Any reputable modular wiring manufacturer will test its systems and their components, from lead to home run, in a clean factory environment before they are dispatched to site. Installations must conform to both BS 7671 as well as BS 8488, the standard for prefabricated wiring systems.
WAGO’s WINSTA pluggable connection system is compliant to a wide range of standards including IEC 60669-2-5, which allows it to be used with home and building electrical system (HBES) switches, and IEC 61535, which protects against mis-mating of connectors. Specific ranges are available for applications such as transmitting KNX, DALI or SMI signals, or for connecting LED lighting modules.
Manufacturers can provide support at all stages of the project – from design to final commissioning – either remotely or on-site, ensuring that installations are standard-compliant for guaranteed reliability.
The increasing use of spring pressure connection makes components immune to temperature cycling and vibrations, making them far more reliable than equivalent screw connections, requiring almost zero maintenance once installed.
MYTH: Modular wiring is only suitable for certain building types
All building types can feasibly benefit from modular wiring, but commercial buildings like offices, as well as schools, hospitals, retail premises and warehouses, provide the biggest benefits.
These buildings will often have several standardised room and floor layouts, allowing wiring configurations to be duplicated room-by-room, or floor-by-floor. This greatly simplifies the design, and allows it to be installed in less time, and with less wastage.
Modular wiring can reap other benefits too, particularly with the increased uptake of smart building services and building management systems. The same trunking can be used for a wide range of building services, including mains power, HVAC connections, lighting and building control cabling. All of it can be prewired and tested prior to delivery, reducing the possibility of wiring errors.
More information on WAGO’s WINSTA Connection System visit: http://global.wago.com/uk