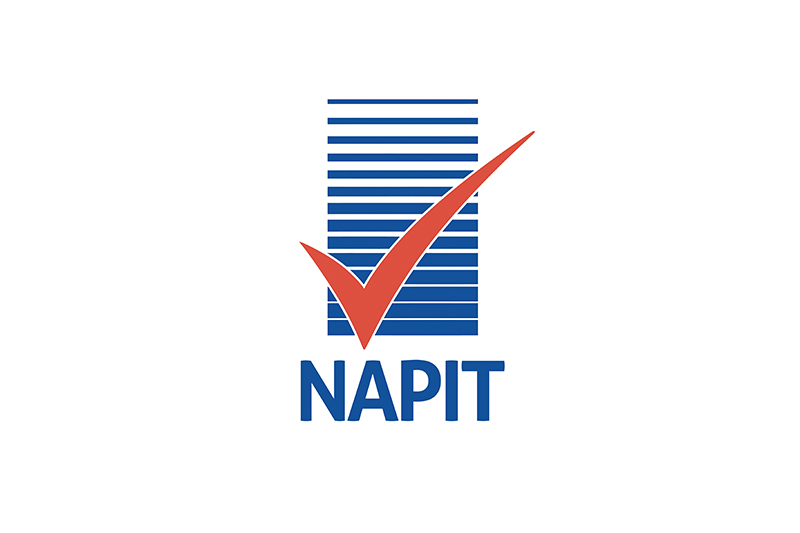
NAPIT’s Technical Development Engineer, Richard Townsend, discusses the differences and BS 7671 requirements for emergency and mechanical maintenance switches.
A switch is a switch…. isn’t it?
Often misunderstood is the topic of switching, either for emergency purposes or for mechanical maintenance. Although they both seem to have a similar outcome with simple enough requirements, they have very different implications and ultimately can have serious repercussions when incorrectly interpreted.
Switching off for mechanical maintenance (Chapter 46, Section 464)
As the name suggests here, we are looking to switch an item of equipment off to carry out some form of isolation, which may fall into one of the following categories:
● Maintenance (planned preventative – proactive)
● Repair (through damage – reactive)
● Replacement (through damage, end of useful life, or upgrade).
The maintenance carried out may well be to the mechanical non-electrical parts of a piece of equipment. We are switching, or isolating, the electrical side for the engineer’s safety.
Mechanical switching for this purpose can take many forms, from rotary isolators in an industrial setting to shower or extractor fan isolators in a more domestic setting. Fig 1 gives representative examples of these devices.
There are a few places that mechanical switching is called for in BS 7671, but one which we generally give the most credence to is Regulation 132.15.202, which requires every fixed electric motor to have a readily accessible and easily operated switching.
This Regulation doesn’t state that it is an emergency requirement or exactly where the switching should be.
As Regulations go, this one is very much aimed at industrial and commercial installations to ensure larger motors can be isolated quickly and safely if needed; this does not mean in case of emergency, see Fig 2 for examples.
Of course, from a domestic scenario, we see motors switched in accordance with this, more by accident than from a Regulation perspective. Bathroom extractors will often have their own multi-pole isolator and hob extractors will often be fed from a fused spur, as are central heating boilers, which will invariably contain a motor of some description.
It can become a little trickier where domestic extractor fans are fed from lighting circuits, but the key here is accessible.
The supplying Consumer Unit (CU) should be accessible, and that means we can switch and isolate if needed, giving us the required multi-pole, all live conductors isolation required by Regulation 464.1, providing, that is, we remain in control of the installation throughout any maintenance or repair (see Regulation 464.2 for greater clarity). This can be as simple as a lock-off kit, lockable isolator, or for more complex installations, the use of a controlled tag out system.
I must stress that this could also be different in a commercial or industrial environment, where the designer may want to isolate an individual motor for maintenance or where there are standby and duty motors in place.
So, we can see where the confusion can start to creep in – where does “switched off safely” in accordance with Regulation 132.15.202 end, and emergency switching take over, and to what extent?
Emergency switching off (Chapter 46, Section 465)
As the title suggests, we are looking to switch off in an emergency, which means there is either an expected or unexpected danger present that we need to act upon to control the supply effectively. We can see straight away that this differs considerably from straightforward switching for mechanical maintenance.
The general principles are the same, multi-pole isolators disconnecting all of the live conductors, see Regulation 465.2, but there are some subtle extra requirements and differences.
The switching devices themselves are generally marked specifically for this purpose, and a key requirement is that one action operates them (see Regulation 465.3).
When we say one action, we mean that we won’t be looking to hold a switch and then turn it, which would arguably be two actions; we are looking to trigger the device almost instantaneously. To instantaneously disconnect in this way, we use push to isolate using mushroom-style switches. See Fig 3 and Fig 4 for examples of emergency push switches.
These push to switch devices are often spring-loaded and, once close to their locking point, will use the spring power to complete the action and lock the switch.
In order to re-set the switch, there can be particular processes for this, incorporating mechanical and/or electric interlocks, to prevent inadvertent reenergisation of an isolated supply, which may give rise to danger (see Regulation 465.4).
Also, adding to these already complex arrangements, there is a need to ensure that when an emergency switch is operated, it does not directly or indirectly harm, or put at risk, anyone that is associated with or could be affected by the primary isolation by introducing a secondary danger, through the isolation of the primary fault (see Regulation 465.4).
A key area that sets out emergency from maintenance switching is assessing and carefully designing each system or process. This has to be done to prevent the potential knock-on effect mentioned earlier and clarified in Regulation 465.4.
This will require a risk assessment and desktop design process to consider all of the possible processes and outcomes; on a production line in an industrial setting, this is a colossal undertaking and is critical for the safety of the operators or anyone coming into contact with an installation or production line.
Some of the areas that would need to be looked at in a risk assessment and design process, but not limited to these, include:
● Assessment of environmental influences
● Process type and complexity
● Number of process operations
● Skill level, training and understanding of operatives
● Possible injuries from malfunction or failures
● Possible malfunctions or failures
● Level of interaction with working areas of equipment
● Historic injuries from similar industrial processes
● New innovations to reduce the danger
● Automatic isolation of previous or next operations for safety due to operation emergency isolation.
Conclusion We can see that the requirements for these two methods of switching are different and very specific. Both have safety implications, but emergency switching carries unique requirements that almost demands in-depth attention and risk assessments before installing them.
Guidance on understanding risk, what risk assessments are, and how to carry them out is given in the NAPIT publication, Risk Assessment and Management Code of Practice, which is available as an E-book.
Find out how to purchase the Code of Practice by clicking here