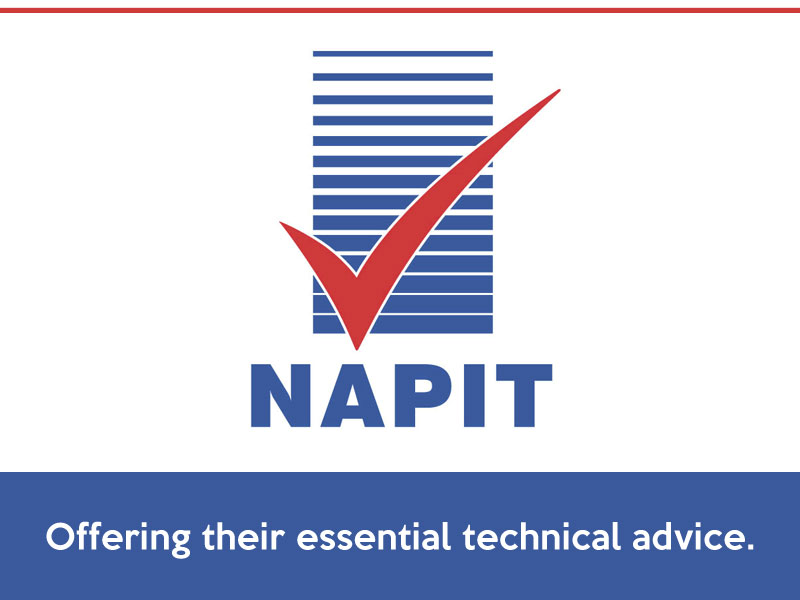
NAPIT’s Don Holmes is back with more essential advice for electrical professionals.
In premises such as oil refineries, steelworks, and other large manufacturing premises, electrical equipment is often supplied from on-site sub-stations, and the risk of receiving an electrical shock or related injury is often greater than in domestic premises – especially where live working is required.
Where these types of locations are involved, it may be necessary to consider the use of rubber floor matting. Rubber matting is used as an additional safety measure to offer extra protection in the event of an electric shock and this article will consider when and where rubber floor matting could be used.
We first need to take a general view of personal protective equipment (PPE), and what we’re required to do.
The Personal Protective Equipment at Work Regulations 1992 (PPE)
These Regulations set out principles for selecting, providing, maintaining and using PPE. PPE comprises all equipment designed to protect against risk to health and safety and includes most types of protective clothing and equipment.
PPE will only be appropriate if it: a) is suitable for the given risks and working conditions; b) takes account of workers’ needs and fits properly; c) gives adequate protection; and d) is compatible with other items of PPE worn with it
Typical items of PPE for electricians who need to work on live equipment are illustrated in Fig 1.
Identifying the need for rubber floor matting
Security, safe systems of work, control measures, job-specific safety tools, barriers and PPE can prevent or reduce the chances of any electrical accident occurring in the workplace. Using rubber floor matting is one means of providing additional protection.
If you’re working with medium and high voltage equipment, rubber floor matting will provide you with greater protection from electric shock.
Where a risk assessment reveals the possibility of danger or damage from electric shock, this risk could be reduced by the use of rubber floor matting, as it can be used to prevent contact with the floor. In many scenarios where floors are bare concrete or substrate, they’re in contact with the general mass of Earth.
The seriousness of an electric shock can vary and will depend on the level of electric current going through the body and the type of contact. A minor electric shock may result in a jolt to the body, but shocks can cause muscle spasms, loss of motion and even death. An additional hazard from electric shock is burns.
Health and safety
When working with live electrical equipment, all reasonable safety measures need to be in place. The use of rubber matting is mentioned in the following Health and Safety Executive (HSE) publications:
– Safe Working Practices for Electricity at Work document (HSG 85)
– Safety in Electrical Testing -Switchgear and Control Gear (information sheet 37)
When a risk assessment is carried out, all the dangers involved in the work to be done must be considered. The result of the risk assessment will indicate whether or not rubber floor matting is required.
Rubber floor matting
The characteristics of rubber make it an ideal material to use for electrical safety matting. Firstly, rubber is suitable as an insulator due to its dielectric and electrically resistant properties. The flexible and cushioning nature of rubber makes it an ideal material to use, to offer some protection in the event of a fall.
Where rubber floor matting could be considered
Rubber floor matting could be considered for use where the risk of electric shock is high, including:
* in front of electrical switchboards
* in front of machine control gear
* in electrical plant rooms
* in lift control rooms
* as portable protection for electricians working on live equipment
An example of rubber safety matting is illustrated in Fig 2.
BS and IEC Standard for rubber matting
January 2nd, 2013 saw the introduction of a new standard governing the use of rubber floor matting in the electro-technical sector. The European Union specification IEC 61111: 2009 harmonized standards in member countries of the EU. As a result, the British Standards Institute (BSI) withdrew and made obsolete the United Kingdom’s previous standard BS921:1976 and endorsed the new one on the 2nd January 2013 as BS EN 61111:2009.
Electrical safety matting which only complies with the superseded standard BS 921:1976 does not comply with the current safety standards and may render firms open to prosecution if an accident were to occur.
Electrical safety matting to BS EN 61111:2009 is designed to provide protection against electric shock and is tested to withstand certain specified voltages. This standard offers a voltage class selection system from 1,000V to 36,000V to enable users to select the correct level of protection against the voltages they may be exposed to.
Another feature of BS EN 61111:2009 is that all classes are colour-coded every metre on the underside of the matting as shown in Table 1. The date of manufacture is shown on the matting.
Typical widths of rubber electrical safety matting are 914, 1,000 and 1,220mm, with the surface being slip- resistant. Typical thickness is 3mm for class 0, 4mm for class 2 and 5mm for class 4.
Maintenance and support
Rubber safety matting should be inspected regularly for damage and wear. It should be kept clean and free of spillages from liquids which could degrade it. It should also be routinely tested as recommended by the manufacturer, to ensure it keeps acting as it was intended and provides electrical safety.
The last line of defence
Health and safety experts emphasise that personal protective equipment is the last line of defence. It only protects the wearer and not other employees, so electrical contractors should ensure that all other safety measures have been put in place first.
This may require a second person to be equally equipped with PPE to enable the safe extraction of a person injured during a work task.
Where there is a need for electricians to carry out live working or testing on electrical switchgear and equipment in non-domestic premises, it is essential that a risk assessment is carried out. Procedures and PPE must be identified to eliminate any hazards. This may include the provision and use of rubber electrical safety floor matting.
NAPIT’s Codebreaker publication gives detailed procedures to aid in carrying out a suitable risk assessment. It is important to remember that where a risk assessment is carried out, it should be monitored and re-assessed at frequent intervals, to ensure that any risk is correctly identified and dealt with.