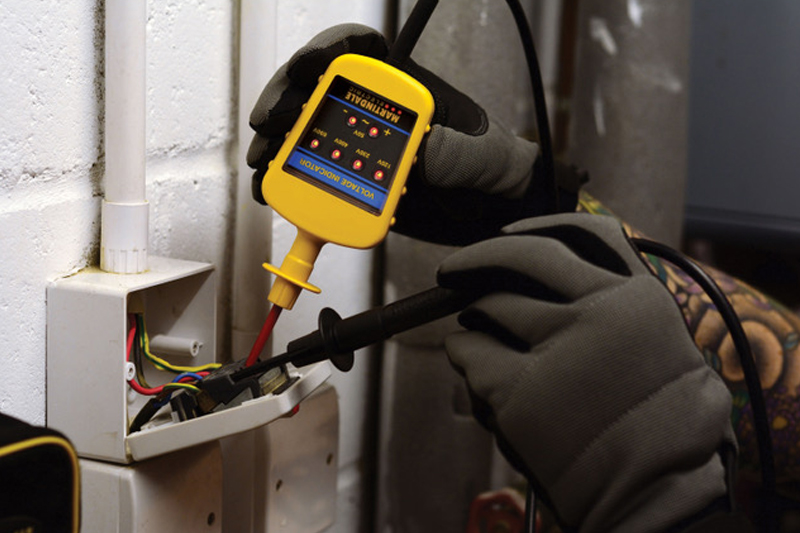
Steve Dunning, Managing Director of Martindale Electric, explains the importance of safe isolation and why using the right equipment is an absolute must.
Safe isolation procedures are necessary to ensure that workers on-site are not exposed to danger when working on or near live electrical systems. There have been incidents where failure to use safe isolation procedures has resulted in injury or, in the worst cases, death.
Selection and use of the right equipment is one of the most important parts of the procedure. Firstly a voltage indicator with the means to prove it is operational, usually by using a dedicated proving unit. Secondly, lock off items suitable for the circuit being tested and signage to warn others. Failure to use the correct equipment and procedures can result in a circuit inadvertently remaining live.
Locking off devices
Locking off devices are either supplied as individual items or, more generally, as kits. There are many kits and combinations available, however a basic starter set should always include a selection of MCB and breaker locks, a padlock with a unique key or combination, a hasp for when more than one person is working on a system, plus an array of lock out tags and warning labels.
For the locking off procedure itself, where a distribution board switch or other means of disconnection is used, this should be locked in the ‘off’ position using a suitable lock with the addition of signage to advise others of the activity. The key or combination lock should be the responsibility of the person doing the work or someone delegated by them.
It is important that any padlock must have a unique key or combination held by the person carrying out the work to prevent anyone else from removing the lock and inadvertently activating the circuit. A unique key lock provides the safest solution. Once the breaker has been locked off correctly, a warning tag should be attached to clearly identify that the circuit has been locked off and is currently being worked on. Locking off the circuit is just one part of the procedure. Next it is absolutely essential to verify that the circuit is dead before carrying out any work.
Proving dead
With a wide range of voltage detectors, multimeters and indicators available, it is essential to fully appreciate what the requirements for proving dead are, and the reasons why some equipment, such as multimeters, should not be used for this process. It’s also important to be aware of the standards for voltage indicators and ensure the tester being used is compliant. Key standards are BS EN61243-3 applicable to voltage detectors to be used in contact with electrical systems up to 1000 V AC and HSE Guidance GS38 Electrical test equipment for use on low voltage electrical systems.
Proving dead needs to be done because the circuits to be tested may not be labelled correctly (or labelled at all) and it should never be assumed that a circuit or nearby circuits are dead because the isolation device is set to off.
Best practice is to use a dedicated voltage indicator and a voltage compatible proving unit when carrying out this procedure. Importantly the voltage indicator must comply with BS EN61243. There is a variety of suitable equipment available on the market, including test lamps or more commonly voltage indicators, such as the Martindale VI-13800 or VI-15000. Both these units include a high wattage resistor in the probe to limit the current in the event of damage to the cable. It is important to note that the voltage indicator must be able to work without the need for a battery. If a device needs a battery and is flat, you cannot prove the circuit is dead.
The procedure for proving dead is to take the voltage indicator and check it against a known source, such as a proving unit, then test the circuit before testing the voltage indicator against the known source again to prove the tester has not failed during testing. Whilst you can use a known live source to test your voltage indicator, a much safer method is using a dedicated proving unit matched to the indicator being used. The reason is that the known live source will only light some of the LEDs on the tester, whereas a proving unit will ensure that all LEDs on all ranges are working, again safeguarding against incorrect readings due to a faulty LED. In addition, there is not always a suitable live source nearby and a dedicated proving unit is faster and safer.
Guidance advises against the use of both multimeters and non-contact devices for proving dead. Multimeters are not suitable for the proving dead process as it is all too easy to select the wrong range and, importantly, a multimeter relies on battery power to function fully, thus there is a high risk of making a false “dead” reading on a live circuit. Non-contact voltage detectors also require a battery in order to work and are often sensitive to other signals, such as static electricity. It’s also not possible to prove they are working correctly with a standard proving unit. Whilst these units can be used to detect live cables, they cannot reliably be used to prove dead.
Reference material
With guidelines well established and safe isolation kits readily available, implementing safe isolation procedures is neither difficult nor expensive and has been proven to save lives and avoid injury. It’s essential for compliance with Electricity at Work Regulations for safe working when installing and maintaining electrical equipment and systems.
Electrical Safety First, in association with other industry bodies such as SELECT, has produced a guidance document that covers best practice for safe isolation (Best Practice Guide 2). This includes guidance on proving isolated equipment or circuits are dead by using suitable test lamps and voltage detectors, and is an extremely useful reference document.
Get more details on Martindale Electric’s alive campaign and its range of proving devices here