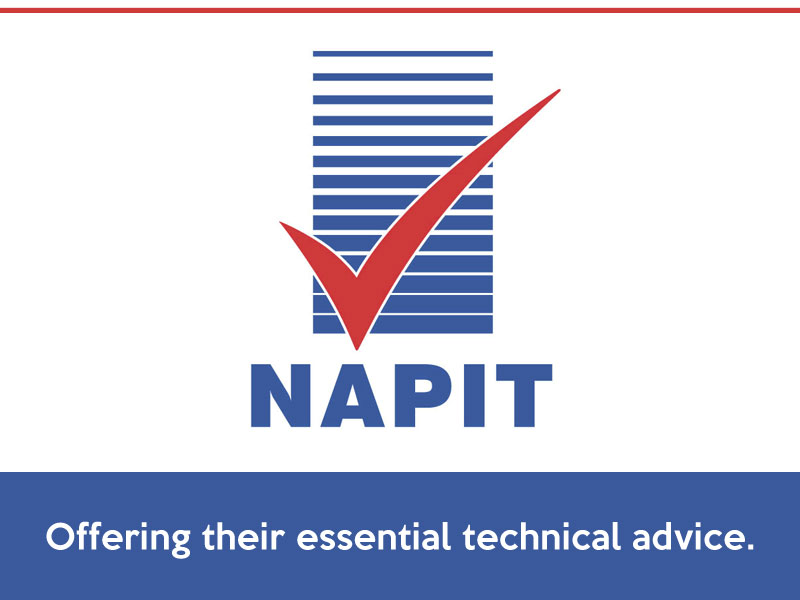
NAPIT’s Don Holmes has more essential advice for electricians.
The installation of earth electrodes is becoming an increasingly significant part of electrical installations. Examples of such installations are where the Electrical Safety and Continuity Regulations (ESQCR) prohibit the connection of a PME earthing facility to any metal work of the installation. Typical installations where this requirement may apply are:
– Remote buildings.
– Construction and demolition sites.
– Agricultural and horticultural sites.
– Caravan/camping parks.
– Marinas,
– Exhibitions, show and stand sites.
-Electric vehicle charging points.
Onshore units of electrical shore connections for inland navigation vessels.
Temporary electrical installations for structures, amusement devices and booths at fairgrounds, amusement parks and circuses.
Another example of where an earth electrode is required is where an electrical installation forms part of a TT system.
In view of the importance of earth electrodes, this article will consider some common types of earth electrodes and their methods of installation. The requirements of BS 7671 regarding earth electrodes are found in Regulation Group 542.2.
Types of earth electrode
Regulation 542.2.2 lists the types of earth electrodes recognised by BS 7671. They include earth rods, earth tapes or wires, and earth plates.
Earth rods
Earth rods are available made from solid copper, stainless steel or copper bonded steel. The most popular choice is the copper bonded steel core rod due to its combination of strength, resistance to corrosion and lower cost.
Earth rods are available in various lengths and diameters. Typical sizes are 9.5 x 1200mm (fixed) and 12.7 x 1200mm (extendable) using an earth rod coupling and driving head, as illustrated in Fig 1.
Earth rods are generally used where electrical installation earth fault currents are expected to be low, as is the case where the electrical installation is protected with an RCD or circuits with RCBOs.
Earth tapes or wires
Earth tapes or wires are usually bare copper. The usual size of copper strip is 25mm wide x 3mm thick as illustrated in Fig 2. The minimum diameter for a stranded conductor is 3mm.
Earth tapes or wires are generally used in areas where the ground consists of rock and it’s difficult to install an earth rod.
Earth plates
Earth plates are usually made of cast iron or copper and are square in shape, with a surface area about 1m2 to 2m2 as illustrated in Fig 3. Earth plates are generally used where high earth fault currents are expected, an example being where a property owner has to provide their own earthing system requiring a low resistance.
In most cases, the greatest influence on the value of earth electrode resistance is the depth the electrode is installed. Doubling the depth can often achieve a reduction of up to 40% in the measured value. Multiple earth rod electrodes can be used to achieve a lower resistance and, as a rule of thumb, the rods should be spaced apart a distance at least equal to the driven depth.
Another factor is the resistivity of the soil which is measured in ohm-metres (Ωm). Soil resistivity is dependent upon the soil’s composition, moisture content and temperature. The ideal location for installing an earth electrode is wet marshy ground (Table 1).
Earth electrode resistance area
The total resistance value of an earth electrode is made up of three main components:
- The resistance of the electrode itself, which depends on the material it is made of and the connections to it.
- Contact resistance between the electrode and the soil it is installed in.
- Resistance of the surrounding soil.
Electrode resistance
Electrode resistance will vary slightly due to the type of material used. Contact resistance between connections is where issues may arise, especially where incorrect terminations have been made and corrosion occurs.
Contact resistance
Contact resistance is often thought of as one of the main factors contributing to high earth resistance readings, but if the electrode is free from paint and grease and the soil is packed firmly around the electrode, this value will be negligible.
Soil resistance
Where the earth is of uniform resistivity, an electrode will radiate current in all directions under installation fault conditions. This current has to traverse concentric layers of the surrounding soil. Since the soil is a relatively poor conductor of electricity, and as the cross-sectional areas of the layers of soil nearest to the electrode are small, the result is that of a graded resistance concentrated mainly in the area of the soil adjacent to the electrode, as illustrated in Fig 4.
As the resistance immediately surrounding the earth electrode is greatest, most voltage will be dropped across this layer under fault conditions. Approximately 80% to 90% of the fault voltage appearing at the electrode will be dropped within the first 2.5m. This is known as the surface voltage gradient and is illustrated in Fig. 5.
Earth electrodes must be correctly installed below ground level and, installed in an inspection pit to ensure the electrode termination is accessible for inspection and testing in accordance with the requirements of BS 7671 (Fig 6).
Earth rod clamps
When connecting an earthing conductor to an earth electrode, the earthing conductor must be insulated where it enters the soil to avoid any possible dangerous surface voltage gradient under fault conditions.
The connection of the earthing conductor to the earth electrode must be carried out using proprietary earth clamps and must be suitably protected from corrosion by applying grease or paint. Remember to fit the, ‘Safety Electrical Connection – Do Not Remove’ label, as required by Regulation 514.13.1 of BS 7671.
Conclusion
It’s essential that earth electrodes are installed correctly, and that the area where the electrode is to be installed is thoroughly checked to avoid any damage to other services during installation of the electrode.
For more detailed information, reference should be made to BS 7430: 2011 + A1:2015, Code of practice for protective earthing of electrical installations.
For more technical articles click here.