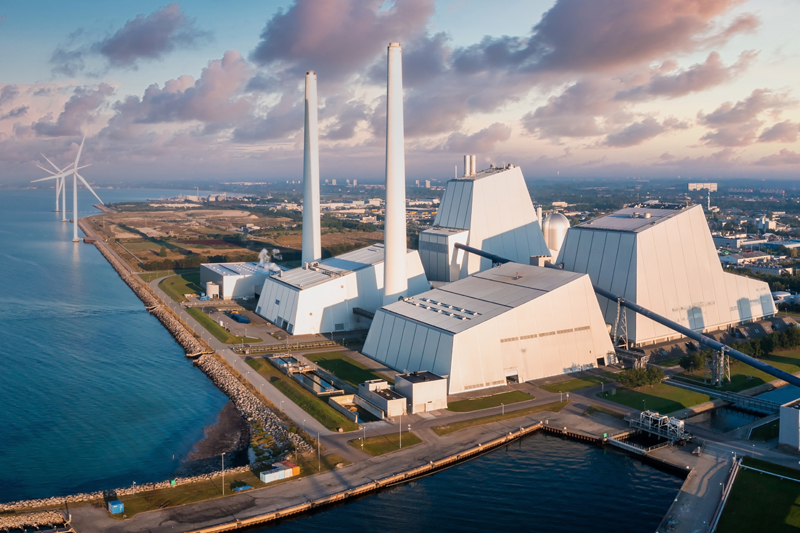
Before you install a cable management system you need to understand where you will install it and make sure that you select the right material to avoid corrosion. In this article Paul Nolan, Projects Director for the Hudson Group, takes a closer look at what factors you should consider.
We’ve all seen rusty or corroded cable management and containment systems due to someone selecting the wrong material. But equally there is little point in choosing a more expensive corrosion resistant material if you’re installing the system in an office.
And there are a lot of materials and treatments to choose from. So, when would you choose pregalvanised and what about powder coated, stainless steel or GRP? There are dozens of choices that you can make.
Clearly the first step is to understand where you will be installing it. Thankfully there is guidance and we can refer to EN ISO 12944-2 which classifies corrosion and gives examples of where you may find it (see the table in Fig 1).
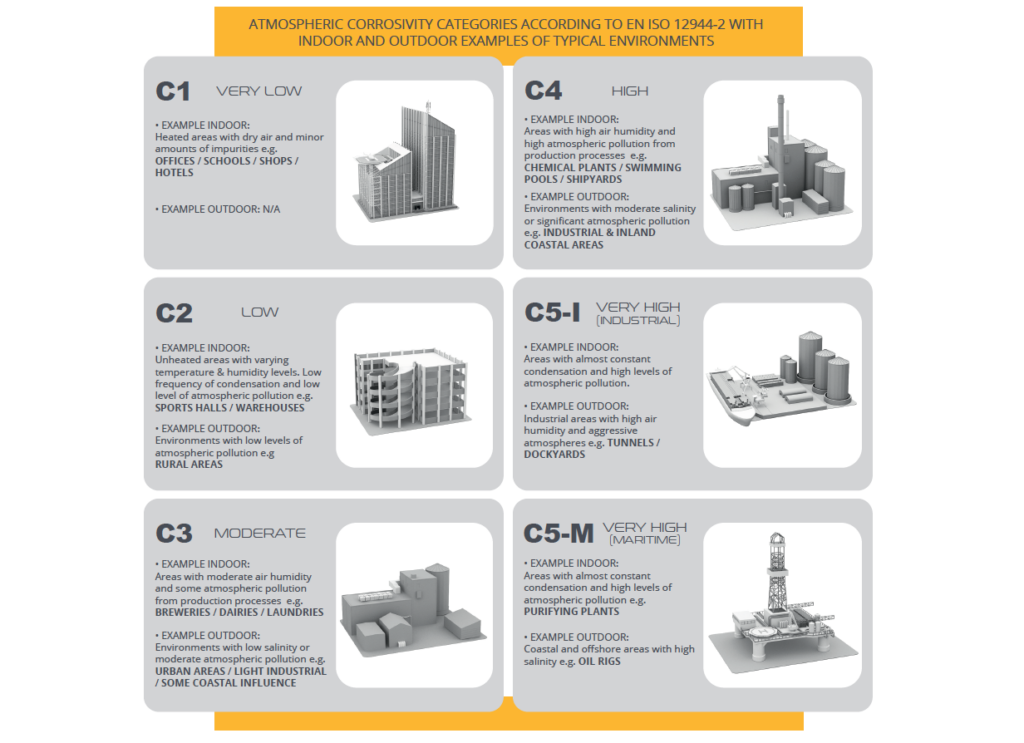
The right material for the job
Looking at the table in Fig 1, let’s go through what materials you might use.
Where there is a very low corrosivity, or C1, you will most likely be indoors in an office, school, hotel or perhaps a shop. Here you would typically choose electro zinc plated or pregalvanised steel.
Raising the stakes higher to a low to moderate, or C2 environment, you will be installing product in places such as industrial premises, sports halls, warehouses or partially covered outdoor areas. Here we would suggest you install a pregalvanised steel cable management system.
For C3 and moderate corrosivity, think outdoors or in a light industrial area, then you need to go beyond a pregalvanised solution. For these applications you would use hot dip galvanised, CPC or powder coated steel or PVC systems.
For seriously corrosive applications where there is a high humidity or significant pollution, such as in chemical plants, dockyards or swimming pools, you will need hot dip galvanised, powder coated steel, stainless steel, PVC or GRP systems. This is a C4 environment from the table in Fig 1.
And when the going gets really tough, where there is almost constant condensation and/or high pollution such as you might see in chemical or water treatment plants, heavy industry and dockyards, then you need to install a material that will stand the test of time.
Known as a C5I classification you should consider stainless steel, deep galvanised steel or GRP cable management systems for these jobs.
And finally, there are marine environments where high moisture salinity, or salt, will add to the corrosion. Here you really do need to use 316L stainless or a GRP system.
Some additional pointers
Corrosion is only one factor to consider when selecting your cable management material. We’ve already talked about balancing corrosion resistance against price, but there are some other things that you should think about.
In projects where there are a lot of electronics, perhaps in a data centre or where there are lots of computers, you need to know about zinc whiskers. These are very thin zinc strands that form on the underside of galvanised products. They grow over time and will eventually break off, causing problems for electronics.
Also, not all galvanised products are the same. Pregalvanised steel will typically have a coating of between 8 – 20 microns while hot dip galvanised will give a standard coating of between 45 – 65 microns, but this is an average and the product will not be coated equally.
For greater protection manufacturers can provide deep galvanised solutions where different carbon steels attract more zinc when dipped to provide an even thicker coating of greater than 160 microns. But if you hear the term “double dipping” then take no notice because someone is trying to fool you. Dipping steel a second time will make no difference to the thickness of the coating.
Equally not all stainless steels are the same – 316L is more corrosion resistant than 304L. The ‘L’ means that it is a low carbon version of the standard stainless so it is more easily weldable, but 316L, which is known as “marine grade”, has more Molybdenum which makes it more corrosion resistant to chlorides and therefore salty environments.
New materials and treatments
Remember also that material science does not stand still – new and better materials and treatments are constantly being developed. A good example is a new finish called Magnelis. This offers better corrosive resistance than galvanised options, it is self-healing for cut edge protection and is more cost-effective. It’s certainly something you should consider in the future.
And for really extreme environments many turn to GRP, or glass reinforced polymer, as a go-to material. Even here you need to be aware of what you’re installing since the mechanical properties of this material can vary.
Delving deeper there are four main resin types of GRP cable management products which will suit different specific atmospheric environments, but that is a whole new subject.
Getting the material right for your next cable management or containment installation is vital if you want to provide a long lasting and cost-effective solution for your customer.
There is a huge range of materials available to choose from. Remember that if you are in doubt, you can always phone the manufacturer to ask for advice, especially if they offer a wide range of different materials.
This article is based on a CPD seminar run by the Hudson Group – ‘Selecting the Correct Environmental Material’.
Get more details on the range of cable management solutions available from Hudson Group here