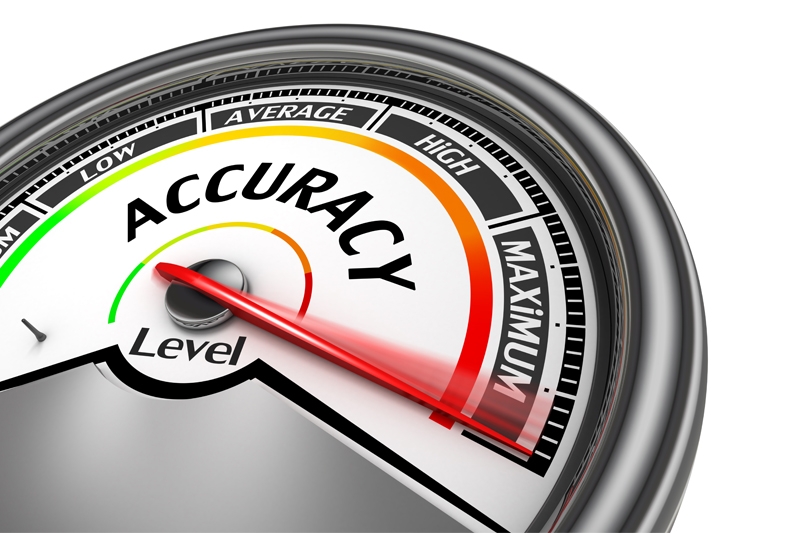
Shaky hands, fat fingers or built-in errors? The team at GAMBICA, the trade association for the test and measurement industry, looks at some of the little known causes of errors.
Those working on or testing electrical installations need to know that their equipment is measuring accurately if they are to stay safe and their test results are to be valid. You may be used to thinking that any errors are the fault of your fat fingers but is that really the case?
In its publication, Measurement Accuracy, GAMBICA has married together impartial information from all the major suppliers of test and measurement equipment, offering a thorough explanation of how errors can occur in measurement, and also acknowledging the limitations of instruments and how they affect performance.
What is for certain is that no instrument can be guaranteed to give readings that are absolutely accurate every time or provide the exact same readings as another apparently identical instrument.
So, where do errors come from?
Errors that affect the overall accuracy of an instrument such as an installation multi-function tester can come from either the instrument or its accessories, or even from the circuit under test. The two most common types of measurement that can suffer significant variation are Continuity and Loop Impedance. They each have their own sources of error which are detailed in the concise publication.
It’s not just errors you have to worry about…
BS EN 61557 is the European wide standard which defines the performance of test instruments used in the verification of low voltage electrical installations under 1000 V AC. It sets an internationally agreed minimum performance to which all instruments must conform. This includes the test range, the types of test necessary and the minimum accuracy required.
“So that’s OK then”, we hear you thinking; “If I buy an instrument which conforms to BS EN 61557, I’ll be alright!” Well yes, up to a point…
As an engineer you’ll often find yourself working at the upper or lower limits of an instrument’s capabilities. It is under these conditions that variations in resolution and accuracy have the greatest effect. Awareness of the precise limitations of your equipment is essential to ensure correct application of a test and interpretation of results.
It all comes down to range, resolution, accuracy and display count. If you don’t understand these properly, you can find yourself making poor or even dangerous assumptions.
Transparency of accuracy is vital
No instrument can provide perfect measurements in all conditions. But every instrument should declare an accuracy within which it should perform for any measured value.
This performance is checked during manufacture against stable, reference sources under laboratory conditions, and should be checked periodically to ensure they remain within their stated accuracy. Does your instrument offer the accuracy you need for your task?
Don’t confuse accuracy with display count. Some digital instrument manufacturers, especially when it comes to digital multi-meters, publish additional or alternative information about the measurement display. This is expressed as a “display count”.
A display count is useful in understanding the resolution of a measurement on each measurement range, and when the range changes up or down a decade, but it doesn’t tell you anything about the accuracy.
It is important to understand both how the accuracies of instruments are defined and the sources of error in measurement, especially where the values are at the extremes of the instrument’s measurement ranges.
For example, many loop impedance testers are used for measuring close to the source of the supply, where loop impedances can be very low – certainly less than 0.03 Ω. Using an instrument with a resolution of 0.01 Ω cannot be guaranteed to give accurate results.
Always try to make the measurement with an instrument where the expected values are well within the limits of the instrument.
Where this isn’t possible, understanding the effects of different types of error can help in assessing whether the measured results are dependable or whether other methods of assessing the circuit’s characteristics would be more appropriate, such as calculated values based on manufacture’s declared data or considering an unenergised impedance reading. Both of these methods can help to avoid an argument with the consulting engineer’s calculated values.
This article has only been able to give you a taster of the new GAMBICA Measurement Accuracy publication. If you’d like to request a free copy, please email: jacqueline.balian@gambica.org.uk