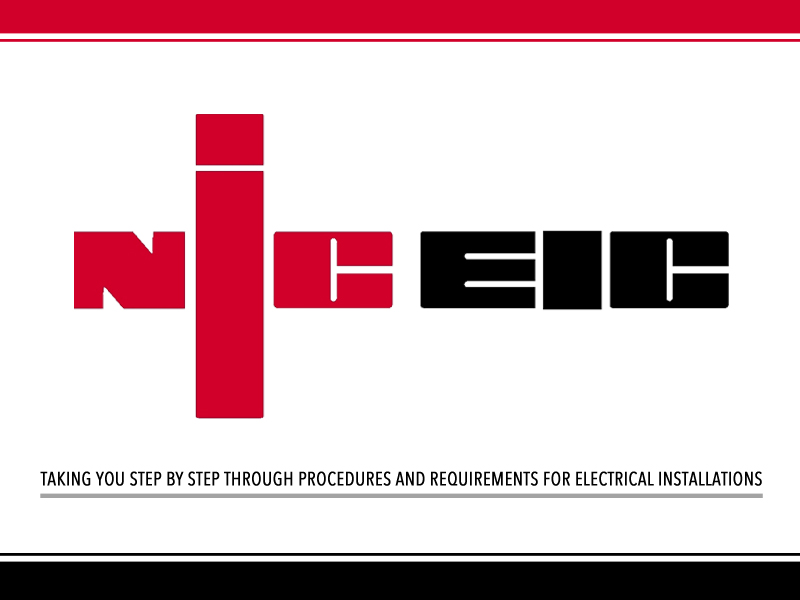
The technical experts at NICEIC & ELECSA look at the effect that thermal insulation can have on flat twin and earth cables.
This article considers the effect that thermal insulation may have when placed on PVC/PVC flat twin and earth cables within a roof space and other such areas. Also considered will be the influence thermal insulation may have upon an electrical installation when carrying out an alteration or addition.
When designing an electrical installation, consideration should always be given to the suitability of cables in relation to the effects of temperature from ambient or thermal conditions. Regulation 523.9 of BS 7671 refers to the installation of cables and the preference to avoid areas where cables are liable to be covered by thermal insulation.
However, with ever increasing requirements for energy efficiency and improved sound insulation within domestic and non-domestic premises, the retrofitting of insulation has become common practice. It is therefore, increasingly likely that existing cables within roof voids, walls and under floors will be in contact with insulating materials.
Where this is the case, it may prove problematic for a contractor when attempting to make an alteration or addition to a circuit or while undertaking a periodic inspection of an installation. It is long recognised that where PVC sheathed and insulated cables are surrounded by polystyrene insulation, the plasticiser within the PVC ‘migrates’ out of the PVC. This has the effect of hardening the PVC, leading to brittle insulation which may generate an increased risk of fire.
Current carrying capacity
Typically, the method of installation will impact on a cable’s current-carrying capacity (z). The addition of thermal insulation surrounding cables will impact directly upon the cable’s ability to dissipate heat during normal use.
Any increase in temperature may lead to a reduction in the life expectancy of the cable or, in extreme cases, cause damage to the insulation, sheath or surrounding area. However, the actual risk would depend upon the type of cable, the type and thickness of the thermal insulation and the current demand for the circuit. To ensure cables meet the requirements for protection against overcurrent (Chapter 43 of BS 7671) the cross-sectional area of the conductors may need to be increased to compensate for any reduction in the current carrying capacity due to the additional insulation.
Circuits having an overcurrent protective device not exceeding 6 A
As with many domestic circuits, and most typically lighting circuits having an overcurrent protective device rated at 6 A, the subsequent addition of thermal insulation is unlikely to have any impact on the circuit design.
Where the installation method ‘clipped direct’ applies (Table 4A2 and 4D5 in Appendix 4) and the cable is subsequently covered by thermal insulation for a length of at least 0.5 m, the current-carrying capacity of the cable must be reduced by half (Regulation 523.9). This means that for a lighting circuit, the smallest permitted conductor size of 1.0 mm2 (Table 52.3 of BS 7671) has a de-rated current-carrying capacity above that which is necessary for the rating of the protective device.
For example, using Table 4D5 column 6, a 1.0 mm2 cable has a tabulated current-carrying capacity of 16 A. If the cable is totally surrounded by thermal insulation for a distance exceeding 0.5 m, the current-carrying capacity reduces to: z = t × Ci ∴ z = 16 × 0.5 = 8 A; this still satisfies the requirement for protection against overload current found in Regulation 433.1.1: b < n < z.
Where:
z = Current carrying capacity of the cable corrected for defined conditions
t = Tabulated current carrying capacity of cable (Appendix 4)
Ci = Rating factor for cables in thermal insulation (Table 52.2, 4A2 and 4D5)
Furthermore, with the focus towards achieving greater energy efficiency, luminaires incorporating Compact Fluorescent (CFL) and Light Emitting Diodes (LED) are becoming more common. Therefore, the typical current demand for domestic lighting circuits has reduced considerably over time and could now be considered to be insignificant.
Circuits having an overcurrent protective device exceeding 6 A
However, where thermal insulation is placed upon a 1.0 mm2 cable and is grouped with other heavily loaded cables, the current-carrying capacity may no longer be sufficient due to grouping factors. Furthermore, depending upon the building design and circuit loading, the thermal effects on other circuit cables within the same location and covered with additional insulation may be at a greater risk of damage.
For example, a typical bungalow having cables within a roof void for feeding circuits such as a shower, cooker and/or ring final circuits are likely to be totally surrounded by, or in contact with, thermal insulation, such that the conductor’s cross-sectional area (csa) may no longer be adequate for the connected load.
Example: A 7.5 kW 230 V AC electric shower wired in 6.0 mm2 twin and earth cable is run through a roof space and clipped to the joists. The existing thermal insulation has a thickness less than 100 mm.
The design current (b) is approximately 33 A with an overcurrent protective device (n) of 40 A. Using Table 4D5 column 2, the current-carrying capacity of 6.0 mm2 is 34 A; it can be seen that the load can be carried safely.
Assume now that in order to reduce heat loss, additional thermal insulation has been installed to the roof void giving a thickness in excess of 100 mm. In this instance the current-carrying capacity of the cable must be reduced. Using column 3 of Table 4D5, the current-carrying capacity of 6.0 mm2 has been reduced to 27 A.
With the extra thickness of thermal insulation, the shower cable is no longer adequate for the connected load and is likely to become damaged over time.
Note: Other rating factors and voltage drop are outside the scope of this article and will not be considered.
Testing and inspection
It is a requirement that every electrical installation should be inspected and tested at regular intervals throughout their lifetime as a means of identifying any damage, deterioration or dangers that may affect the electrical safety of the installation. Regulation Group 651 identifies the requirements for periodic inspection and testing and, where possible, visual inspections supplemented by the appropriate tests (Regulation 651.2).
Insulation resistance testing of conductors confirms the adequacy and effectiveness of the insulation as a means of providing basic protection. Regulation 643.3 sets out the requirements for insulation resistance testing and the options available. Where it is suspected that a particular circuit has been exposed to thermal damage as a result of heavy loading and/or additional thermal insulation, an insulation resistance test might reveal signs of damage/deterioration, which likely become more evident over time.
It is expected that the insulation resistance values of all circuit cables will be significantly greater than the values given in Table 64. Where this is not the case, further investigation will be required where the values of insulation resistance are less than those given in Table 64.
Generally, it is not usually recommended nor is it a requirement to gain access under floors, in roof spaces or within the fabric of the building during an inspection. Although, where it is necessary to gain further evidence for the Electrical Installation Condition Report (EICR) it may be necessary to extend the inspection to such locations. However, the locations should not be accessed without taking the necessary precautions, such as confirming the adequacy for safe movement and ensuring the provision for adequate lighting and appropriate walkways or boarding. Where an installation incorporates solar PV, a gas boiler and/or TV aerial booster, such access facilities should have been provided to permit subsequent inspection and testing.
Reporting defects
As in all cases, the electrically competent person carrying out the inspection must inform the customer of any defect observed during an inspection that is likely to affect the continued safety of the installation. Where it may be apparent that an existing cable has been made electrically unsound such that a potentially dangerous condition exists due to the loading conditions of the cable and the addition of thermal insulation, an observation code of C2 should be entered on the EICR. However, where there are no signs of significant thermal damage to the cables or the surroundings due to the addition of thermal insulation but the conductors have insufficient current-carrying capacity with regard to the method of installation and the nature of the load, a code C3 should be given.
Summary
Due to the reduced current demand of the connected loads through improved energy efficiency, it is unlikely that any subsequent addition of thermal insulation within domestic premises is liable to have any negative effect on lighting and ring final circuit cables. Although, where such circuit cables are grouped with other circuits carrying a greater current demand, there may be a risk of thermal damage.
Circuit conductors carrying larger load currents for significant periods of time may be subjected to negative thermal effects when covered by thermal insulation. Although it may be difficult or impractical to undertake a visual inspection within restricted areas, the subsequent testing procedures as highlighted in Chapter 64 are likely to identify any relevant issues.
Where PVC sheathed and insulated cables are in contact with polystyrene insulation, the plasticiser within the PVC ‘migrates’ out of the PVC. This has the effect of hardening the PVC leading to brittle insulation which may generate an increased risk of fire.
Wherever possible cables should be rerouted above thermal insulation.
Get more details about NICEIC registration by clicking here