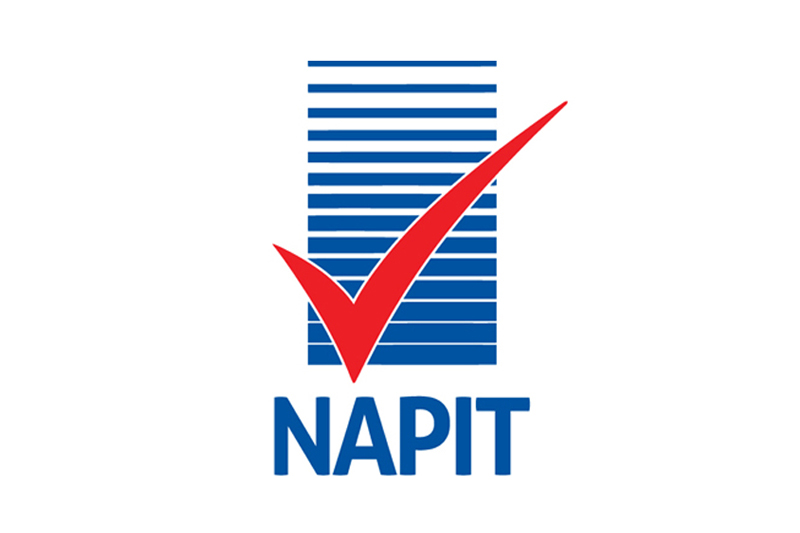
Steve Humphreys, Technical Commercial Manager at NAPIT, unravels the mysteries behind fault detection.
An electrical fault isn’t a natural occurrence; rather, it is an unplanned event that occurs unexpectedly.
When the call to attend a client’s premises due to an electrical fault is received, it’s often difficult to immediately assess the cause of the problem. The usual discussions normally start with what was going on at the time of the fault and, once user error has been ruled out, the detailed inspection begins.
After ruling out vermin or water damage, the majority of electrical faults are caused by the failure of the initial installer to correctly select and install the electrical installation to the current standards and regulations.
Therefore, poor design or installation techniques contribute to faults, and it is vitally important that the design of the installation is fit for its intended purpose.
Faults that occur in our wiring systems aren’t usually along the length of the cable, unless they’re incorrectly installed and subject to damage. Faults, however, usually occur at the equipment and/or accessories within the cable connections, where the installer has been involved, as shown in Fig 1.
We all know that BS 7671 tells us that connections must be electrically and mechanically sound, but we also know mistakes can happen.
The importance of confirmation of correct torque tightening of terminals is essential, as both under- and over-tightening can result in the failure of the connections to equipment or accessories.
For this reason, it’s important that we follow Regulation 526.3 which stipulates that every connection shall be accessible for inspection, testing and maintenance.
Designers can mitigate against the impact from faults. This can be achieved, as shown in Fig 2, by making sure we divide our installations into several circuits as per Regulation 314.1 indent (i), to avoid danger and minimise inconvenience in the event of a fault. In reality, however, the designer cannot entirely ‘design out’ the possibility of faults occurring.
There are also other factors that may lead to electrical faults in our installations, such as:
• Misuse
• Negligence
• Overuse
• Abuse
These factors can lead to faults in perfectly well designed and installed electrical systems and equipment.
We can reduce the risk of faults by ensuring that electrical installations are looked after and well maintained. This may involve a systematic maintenance regime, such as a facilities management programme, or by carrying out regular inspection and testing.
The process of fault finding can seem daunting, especially to newly qualified electricians or trainees.
However, it doesn’t need to be if they adopt a methodical approach, understand electrical circuits and are competent in inspection and testing. At all stages of the fault finding process, we must work safely, and this will include safe systems of work such as safe isolation.
Where do we start?
Fault finding can be broken down into simple steps using a ‘who, where, when and why?’ methodology.
The steps involved to successfully find a fault can be summarised as follows:
1. Identify the problem/symptom
We first need to identify what is actually happening. This could be as simple as a protective device that keeps tripping.
Once we’ve identified the problem, even at this early stage, we can start to formulate in our mind what the fault could be. It’s always good to start with the obvious as there’s no point rushing in and dismantling the electrical installation if it isn’t necessary.
2. Gather information/evidence
At this stage, we can start to gather information and facts. Having good knowledge of the electrical installation and its associated circuits is essential, and this knowledge can come from a number of sources, such as:
• People (yourself, the client, the designer)
• Manufacturer’s instructions
• Drawings and circuit diagrams
• Circuit charts and schedules
• Previous test results
Fig 3 demonstrates these points using a sample EICR form.
3. Analyse the evidence
Once we’ve gathered the evidence, we need to analyse it in conjunction with carrying out standard tests and a visual inspection.
The cause of the fault may become obvious during a visual inspection, for example, water ingress into a piece of electrical equipment.
Standard testing is useful to back up any initial suspicions or to compare against previous test results.
4. Interpret information, inspection and test results
At this stage, we’re pretty much ready to diagnose the fault based on all the evidence and the test results.
Apart from very obvious problems that could be seen on a visual inspection or very complex faults, most faults generally fall into only a few categories, such as:
• Open circuit
• Short circuit
• Earth fault or leakage
• High resistance
• Cross polarity
It’s worth pointing out that you may encounter more than one fault on a particular electrical installation or circuit. However, it’s best to identify and rectify one fault a time. This will ensure you still maintain a methodical approach and don’t get confused during the fault finding process.
Table 1 is a simplified guide and can be used as a handy basic tool during the fault finding process.
What next?
5. Rectify the fault
Having established the fault, we’re now ready to rectify it. This may involve rewiring part of a circuit, replacing any defective electrical equipment or simply tightening loose connections.
6. Carry out functional tests
We need to check that the fault has been rectified. This will involve carrying out basic functional tests, such as switching equipment on/off.
It would be appropriate to carry out some standard testing, such as continuity, insulation resistance, earth fault loop impedance and possibly RCD tests and record the results to confirm the circuit is safe for continued use. At this stage, it’s also good practice to show the client what you initially found (the fault, for example) and what you’ve done to fix it, including photographic evidence.
Conclusion
Fault finding is a task that most electricians will be required to carry out at one time or another. By adopting a methodical approach it can be less complicated and frustrating than you think and, ultimately, can be very rewarding.
Although we ideally don’t want to encounter faults in our electrical installations, identifying and rectifying them provides us with valuable experience and builds our problem solving and fault finding skills.
For more information on NAPIT Scheme Registration, click here
Find more industry technical articles here