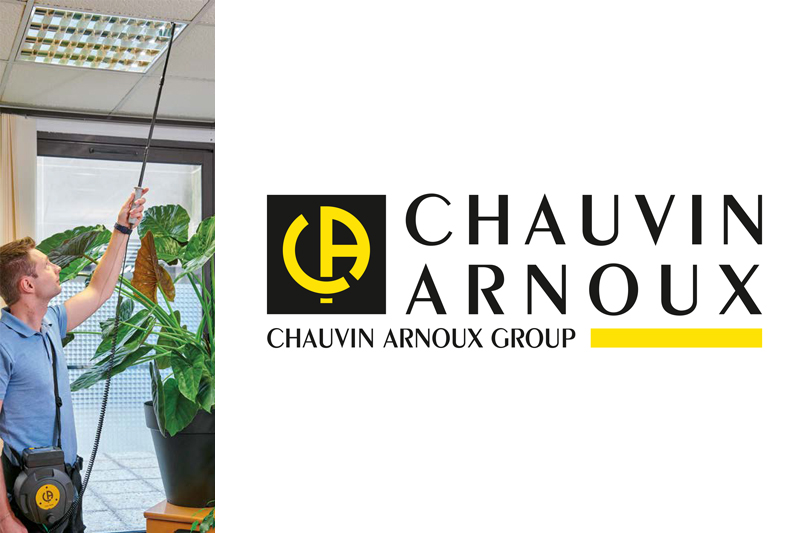
Julian Grant, Managing Director of Chauvin Arnoux, ponders why electrical professionals don’t undertake more R2 testing.
In many trades there is a natural tendency toward the long-established methods and techniques learned as apprentices that have been passed down from the generations that went before. This is especially true for electricians. While examples of the trade changing can be seen in some areas, like the wide adoption of ‘push-in’ style connectors over the old choc blocks, or the recent use of torque screwdrivers, very little change is seen in other areas. One such area that we aim to address in this article is inspection and testing, specifically testing the continuity of protective conductors.
Two testing methods
There are two methods for testing the continuity of protective conductors: a) the R1+R2 method, where Line and PE are linked, and b) the R2 method using a long wander lead. Most electricians were trained religiously to undertake the R1+R2 method and only shown R2 as an option for testing protective bonding conductors. This practice has become embedded, and many electricians now believe that R1+R2 is the ‘proper’ way to test continuity. The regulations, however, make no such statement.
Regulation 643.2.1 of BS7671 simply states that the continuity of conductors and connections to exposed-conductive-parts and extraneous-conductive-parts, if any, shall be verified by a measurement of resistance on protective conductors, including protective bonding conductors. So, there is a requirement to verify the continuity of all protective conductors and their connections to exposed (e.g. metal light fitting) and extraneous (e.g. metal mains water pipe) conductive parts. To achieve this in the majority of cases, it could be argued that the R2 method is much quicker, easier to carry out, requires little to no dismantling of the installation, requires no links to be added at the distribution board or in contactors etc., and if a suitable insulated pole is used, requires little working at height too. Remember testing is for all connections to exposed and extraneous parts – R1+R2 testing at the end of the circuit only, although common, is not acceptable practice.
The practice of mass R2 testing has been around for a long time, but is usually only undertaken by specialist inspectors from testing companies who regularly performed EICRs on huge installations like hospitals, factories, and petrochemical refineries. To these inspectors, the idea of carrying out R1+R2 testing on such installations would be laughable, and the level of dismantling required would be almost impossible in many cases. This innovative practice from companies at the top end of inspection and testing demonstrates that there could be real benefits to those electricians working on a smaller scale, especially when carrying out EICRs.
R2 testing method
The method used to perform R2 testing doesn’t require every measurement to be made by trailing a lead all the way back to the MET (main earthing terminal) – a more practical step-by-step approach can instead be used. Start by proving the earthing conductor and main protective bonding conductors and any protective conductors for submains. Then use these proven test points as a reference to test the final circuit CPCs and connections to exposed and extraneous conductive parts. When the practice of mass R2 testing was first adopted, the testing companies mentioned earlier were using specialist bespoke poles and long wander leads not available to most. But nowadays there are several manufacturers offering wander leads – you may even have one in your van that you use for testing protective bonding conductors.
It is even possible now to purchase comprehensive R2 testing kits, which include a wander lead with built-in continuity meter, belt harness and insulated pole. This type of kit makes large scale R2 testing a breeze and speeds up your overall testing time, and therefore profitability. Having a continuity meter built into the cable reel means that the person doing the R2 testing is self-sufficient and your multifunction tester can be used to carry on testing other items, again speeding up the overall testing. It is worth all electricians taking a closer look at the potential benefits of carrying out more R2 testing and with the new products available on the market, it will speed up your testing – especially when performing EICRs.
To get more technical advice and support from Chauvin Arnoux click here