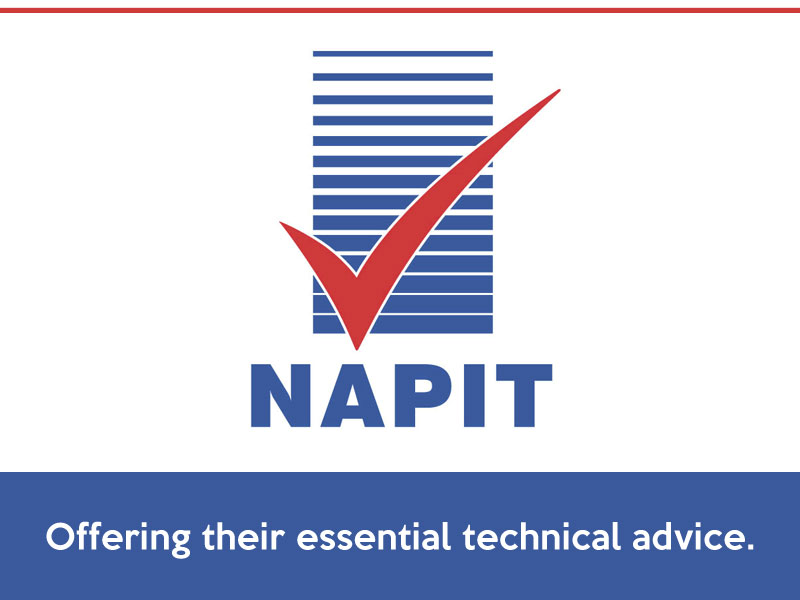
NAPIT’s Bill Allan returns this month with more essential advice for electricians.
Timber-frame buildings are now seen as a mainstream construction method in the UK for dwellings, including extensions to brick-built houses. Electrical contractors frequently have questions about how cables should be run in timber-frame buildings, so this article will deal with some of these questions.
Construction of timber-frame buildings
Timber-frame buildings consist of an internal load-bearing frame of timber treated with preservative and an outer leaf of bricks or some other type of cladding. The timber-frame is usually made in a factory to strict quality control measures and delivered to the building site on a lorry. Head plates (also called top plates) are horizontal timbers situated along the top of an external wall at the level of the eves for bearing the ends of joists or rafters. Normally, double head plates are fitted. Fig. 1 shows the framework for a single storey, timber-frame building.
The external walls
The type of materials used and the positioning of each component can vary. Fig. 2 shows a typical external wall. It shows a 50mm cavity and a 20mm service void. Fig. 2 also shows that the external wall has a breather membrane and a vapour control layer (VCL). Electrical designers and installers need to understand the purpose of each component.
The cavity
Air circulation is necessary to prevent rot and this is provided by a cavity, normally 50mm wide. The cavity must be kept clear to inhibit the passage of moisture from the outer wall surface to the inner surface. In case of fire, the cavity can act as a chimney and, therefore, it must be suitably closed around its edges.
The service void
The purpose of the service void, as the name implies, is to provide a space for installing services, including cables. It is usually 20mm deep and is constructed with battens onto which the plasterboard for the internal wall surface is fixed. The service void should be sealed at its perimeter to avoid convection of air currents.
The vapour control layer (VCL)
A vapour control layer (VCL) is typically installed on the room side of the insulation (i.e. the warm side) in order to prevent warm moist air escaping from heated rooms and letting it into cooler parts of the wall, causing the moist air to condense. Such condensation would reduce the thermal performance of the insulation and increase the possibility of damp and rot growth. A VCL can be in the form of a heavy gauge plastic sheet, a reflective aluminium foil or plasterboard containing an integral VCL. When the VCL is positioned as shown in Fig. 2, it would need to be penetrated by cables which are run down the service void when connecting the cables to wall-mounted accessories. It is essential that the VCL is sealed with appropriate tape after being penetrated. It is becoming more common to install the VCL on the insulation side of the service void so that it doesn’t need to be penetrated by cables.
The breather membrane
A breather membrane is installed on the cold side of the insulation to prevent rainwater from getting into the wall while allowing any water vapour that has found its way into the wall from the inside to escape. For maximum efficiency, all joints in the membrane should be sealed.
The insulation
Fig. 2 shows insulation – 120mm thick – which gives a thermal and acoustic performance to the building. This insulation can be in a number of forms, such as rigid polyurethane rigid foam (PUR), polyisocyanurate or polyiso foam (PIR), or a glass or mineral wool. Common trade names for the rigid type of insulation made of PIR or PUR are Celotex and Kingspan Kooltherm. The insulation is fixed against oriented strand board (OSB).
The internal walls
The internal stud walls can be either hollow or filled with insulation to improve acoustic performance. A sound absorbent quilt, such as mineral wool, is commonly placed in internal stud walls around noise sources such as playrooms, bathrooms and any party walls.
Running cables
Cables run in the service void and/or stud walls may need to be de-rated and reference should be made to Appendix 4 of BS 7671 or Appendix F of the IET On-Site Guide (OSG). Cables must be routed in the permitted safe zones or otherwise mechanically protected in accordance with Section 522.6 of BS 7671. For installations in dwellings, cables must have 30 mA RCD protection in accordance with Section 411 of BS 7671.
Fixing recessed back boxes
Recessed back boxes can be fixed to horizontal noggins set back to box depth. Alternatively, dryline back boxes can be used. It is advisable that back boxes are fitted with an intumescent back pad (i.e. ‘putty pad’), to maintain the acoustic integrity and fire resistance of plasterboard partitions. No more than one two- gang or two one- gang back boxes should be installed in the same stud cavity. Back boxes should not be fitted back-to-back in the same stud cavity.
Fire safety
Where electrical and plumbing accessories penetrate fire compartment walls and floors, fire-resistant materials (called ‘firestops’) are used to seal openings and joints and inhibit the spread of fire and smoke.
Approved Document B, Fire Safety
The installation of cables and back boxes in timber-frame buildings is currently being reviewed. With regard to the Building Regulations 2010 which apply to England, a revised Approved Document B, Fire Safety is being considered for publication later this year. It is understood that the building regulations of the other home countries are likely to include similar changes.
Conclusion
The guidance given in this article is intended only as a general guide as methods of construction and the materials
used in timber-framed buildings can differ. Discussion with relevant persons, such as the building control body, the builder and other trades, will be necessary before starting work. NAPIT wishes to acknowledge the advice of the Structural Timber Association in the writing of this article.