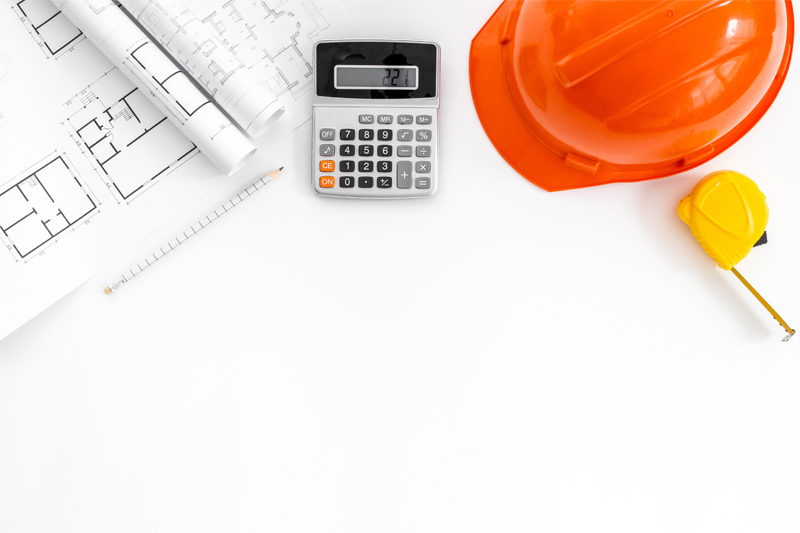
Jake Hardcastle, Electrical Design Engineer at Thornley & Lumb Partnership, identifies some of the real hidden costs of inefficient cable calculations.
Designing an energy-efficient electrical installation involves thoughtful consideration of various factors in order to minimise energy consumption and maximise sustainability.
When designing electrical installations, designers should not only design a system that meets the clients’ needs, is cost-effective and is compliant with BS 7671, but also one that is energy efficient.
This will commonly be considered through selected luminaires, lighting control, selection of energy efficient appliances etc. However, one often overlooked source of energy wastage is inefficient cable sizing, and in a bid to reduce energy costs as much as practically possible, it is crucial to consider this.
While the idea of sizing a cable to reduce energy loss is nothing new, the continuous search for cost reductions, competitive tendering and the rising price of copper mean selecting a larger conductor size doesn’t seem economically attractive and many will often fail to notice the benefits.
Reconsidering cable size
In this article I want to delve into the impact of cable sizing on energy consumption and highlight the advantages gained from selecting a larger conductor size than what is strictly necessary – something that is often not given any consideration.
By intentionally selecting a larger conductor size, we can effectively reduce wasted energy. We will examine the potential savings and long-term benefits of using a larger cable size.
Section 17.4 (Design Considerations) within Appendix 17 of BS 7671 states that: “consideration should be given to limiting the voltage drop within an installation to a level below of that required”.
These values can be found in section 6.4 of Appendix 4. By reducing the voltage drop further than what is required, we can reduce the power wasted in the form of heat through a conductor.
Selecting a cable size larger than what is the minimum required in order to satisfy BS 7671 can minimise energy wastage, providing a more energy efficient installation, and furthermore, can reduce the client’s electricity costs.
Increasing the cross-sectional area will reduce energy wastage but will increase initial installation costs. The designer should determine whether the savings over a certain time period outweigh the initial higher cost.
There are, of course, practical restrictions to this such as the size of terminations and the ability to be able to actually terminate the conductor within accessories.
Additional recommendations on the energy efficiency of electrical installation design can be found in Appendix 17 of BS 7671:2018, Amendment 2:2022.
Calculating energy wastage
To calculate the energy wastage in a cable, two things need to be known:
a) the current in the cable,
b) the resistance of that cable.
The resistance values of cables can be found in the IET On-site Guide (Appendix I) and IET Guidance Note 3: Inspection and Testing. Using an example of a 32 A EV charging point, supplied from a consumer unit 10m away, we can look at three different cable sizes and the comparisons on energy wastage.
In order to calculate this, two of the basic principles of electrical engineering are to be used. We can use the two following formulas to calculate the power wasted within a cable: V=IR (Ohm’s Law) and P=IV (Power Formula).
As resistance is directly proportional to voltage, i.e., if resistance is increased, voltage will increase and therefore the higher the resistance of the cable, the greater the voltage drop will be.
As voltage and power are also directly proportional, the greater the voltage drop in the cable, the greater the power wasted will be. As voltage drop increases, the voltage available for the connected appliance decreases, resulting in reduced efficiency and wasted energy. Therefore, the voltage drop should be aimed to be as low as practically possible while striking a balance between energy savings and economic considerations.
As the current of the circuit and resistance of the cable will be known, but not the voltage drop within the cable, we can substitute V in the formula P=IV for IxR in the Ohm’s law formula. This leaves us with P=I2R. This will give the power wasted within the conductor.
The spreadsheet (pictured above) shows an example of three cable sizes used in this scenario. Assuming the minimum conductor size permitted is 4mm2, in this example we can look at two additional larger conductors to be considered in this design.
Looking at the spreadsheet it can be seen that 4mm2, 6mm2 and 10mm2 are the three cable sizes considered. Using a Steel Wire Armoured cable in this example and therefore the Circuit Protective Conductors being the same size as the Live conductors, the resistance values (mΩ/m) can then be selected from the On-Site Guide or GN3, as seen in column 2.
Total cable resistance
In order to calculate the total cable resistance, this value must be multiplied by the length of the circuit and divided by 1,000 to convert from mΩ’s to Ohms. Using the formula I2R, the current demand and resistance can be inputted to give the power wasted in the cable. This figure can be divided by 1,000 and multiplied by the hours used per year to give Kwh per year. This example is based on the usage of an EV charging point for 4.5 hours per day, five days per week over 50 weeks of the year.
This figure can then be multiplied by the Kwh per unit charge which will vary depending on the energy provider and the time of day. In this example a figure of 35p per Kwh is used.
It can be seen from the table that using a 6mm2 cable opposed to a 4mm2 cable would give an annual saving of £12.34. Using pricing found at the time of writing this article, 3 core 4mm2 Steel Wire Armoured Cable can be purchased for £2.93 a meter and 6mm2 for £4.08, meaning 10m would cost £29.30 and £40.80 respectively. This means the payback period for using 6mm2 compared to 4mm2 would be a little under one year and you would see a saving in subsequent years.
Using 10mm2 cable gives a further saving of £10.08 compared to 6mm2 cable and a total saving per year of £22.42 compared with 4mm2 cable. The cost of 10mm2 3 core Steel Wire Armoured is £6.52 per meter, totaling £66.20 for 10m, £25.40 more than 6mm2 or £36.90 more than 4mm2.
The payback period for the 10mm2 cable compared to using 4mm2 cable would be approximately 1.64 years:
Payback Period = Initial Cost / Annual Savings = £36.90 / £22.42 = 1.64 years
It can be concluded that the payback period, even for the 10mm2 option, is relatively short considering how long something such as an EV charger will be in service for.
If the client was to have ownership of this installation for a long period of time it would be worth paying the additional installation costs for the savings that will follow each year, as well as the reduced power wasted and subsequent energy-efficient installation.
Never underestimate cable sizing
By selecting a larger cable with a lower resistance, energy efficiency can be significantly improved. As well as increasing cost-effectiveness and reducing electricity bills, this contributes to a greener, more sustainable planet.
In pursuit of the most energy-efficient electrical design, the importance of cable sizing should not be underestimated. This example shows the impact of cable selection on energy consumption and while this shows the potential savings of only one circuit, consider very large homes with a hot tub, sauna, multiple EV chargers etc. – the savings could be significant.
If we then translate that to an industrial environment, the benefits could be even greater.