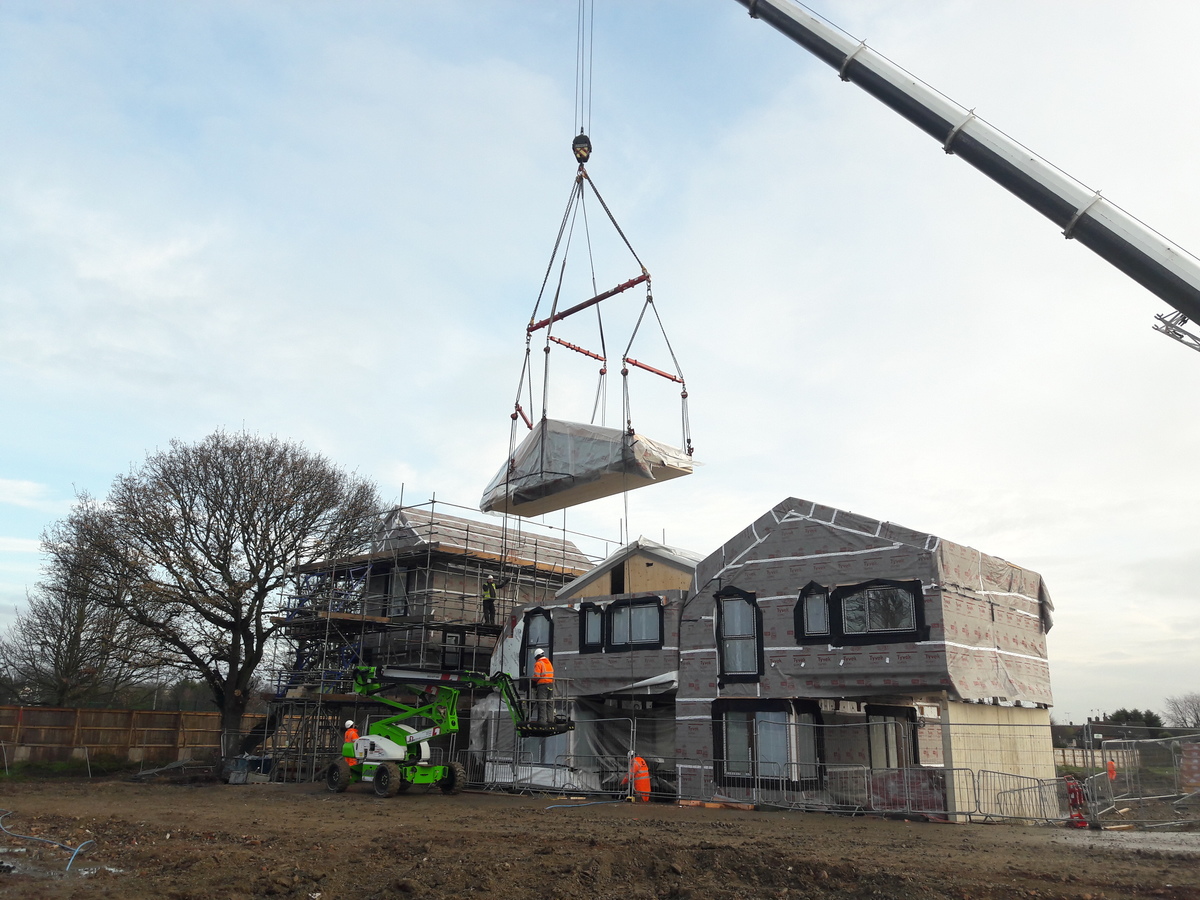
Harry Leeson, Director at Newtons Group, looks at whether pre-built, modular homes will be the answer to the nation’s housing crisis and the challenges this new method of construction is likely to present to electrical professionals.
Modular construction in the UK has now gone mainstream. Once confined to those one-off Grand Designs-esque single properties, a hotel made from shipping containers, or the Portakabin hospital, the last decade has seen a huge rise in the number of everyday houses being manufactured in the factory, rather than built on-site.
Housing crisis
One of the key reasons for this is the current UK housing crisis, with home ownership now seeming like an impossibility for many looking to get a foot on the ladder. In 2017, the government set the goal of building 300,000 new homes across the UK, achieving only 190,000 according to the most recent figures.
A lack of skilled workers has been blamed, with many UK tradespeople exiting the industry because of the recession. “During the last recession, many skilled labourers left the construction sector and simply didn’t return,” said Tom Hardiman, Modular Building Institute Executive Director. “This, coupled with developers needing to find greater efficiency, has made prefabricated buildings much more appealing”.
You only have to look towards some of the major names in house building that are investing in these new processes to see that the tide is certainly turning. Earlier this year construction giant Berkeley was given planning permission to construct a modular homes factory on a ten-acre site in Ebbsfleet, Kent. This investment, which consists of a 150,000 sq ft manufacturing facility and 15,500 sq ft office building, will allow Berkeley to produce up to 1,000 properties per year.
Additionally, a quick Google search reveals that a number of companies are now set-up to deliver these types of homes. nHouse, for example, is building a factory in Peterborough and claims to be able to deliver up to 400 homes per year, with a house taking just 20 days to be constructed off-site .
But what does all this mean for the average UK tradesperson? Whilst on-site construction isn’t likely to be consigned to the past any time soon, the push towards pre-fab has the potential to shake up the industry as we know it. But how should we, as electrical contractors, feel about it?
I run a modest construction company called Newtons Group, based in Southend-on-Sea and operating around London and the South-East. We were recently invited to undertake the electrical installations for a new development of modular homes, at a factory based in Basildon, Essex.
The company is called NU living, a division of the Swan Housing Association charity that operates throughout the South East and who have recently begun a number of large regeneration schemes throughout Basildon and its surrounding areas. Rather than turning to one of the existing companies producing modular structures, Swan Housing was one of the first Housing Associations to have its own in-house developer, allowing all profits from build-to-purchase to be reinvested.
The site is an impressive newly completed factory in Basildon, the result of a £3million investment to get production up and running. The huge factory floor space is designed as a production line system which allows CLT timber ‘modules’ to make their way around the factory (using ‘air-skates’ which are impressive in their own right) through the different stages of construction – from assembly (the CLT is cut and assembled on-site), to lining, first fix M&E, boarding and finishes and, finally, second fix and decoration – ready for delivery to site.
The process is actually more similar to factory manufacturing than construction, and of course this is the point, with manufacturing experts such as factory MD Paul Williamson on board to apply and adapt existing processes used for items such as cars, radios or toothbrushes, to the process of house building. What’s been the most engaging part about our own involvement here is the meeting of these two industries, and the thinking, designing and problem solving that has taken (and continues to take) place as a result.
Dean Macey is our Lead Engineer and has worked in all areas of the electrical industry. He’s been Project Managing the electrical installations at the factory, working with the NU living team to fine-tune the installation processes so the factory can reach full working capacity.
“On-site, wiring a house is reasonably straight forward, finding your route and wiring from A to B. But in here, you start on ‘A’, but ‘B’ is often in a completely different module!” he says.
“It’s a case of seeing the plan in sections, wiring accordingly and visualising it coming together. One of the key issues is minimising the need for cable joins – perhaps you’ve wired in the upstairs lighting but the position of the switch for the room you’re in is in another module that isn’t attached yet. Or the upstairs power circuit is wired but you can’t get it back to the DB as the ground floor isn’t attached. These are all challenges we’ve had to foresee and overcome.”
Upskilling the young ones
For apprentices, modular construction presents a perfect opportunity to practice their skills through repetition, mirroring the work of their supervising electrician. Each module goes through stringent quality checks before the next production stage so errors can be easily rectified and, with everything exposed, standard can be pushed and continually checked.
We’re only a few weeks in, but the consistency you experience when working in this way has the potential to allow for top quality workmanship.
The factory environment is something that may not suit everyone, however. We’ve been lucky to get involved in the early stages, working with our client to adapt and improve the design of the installation, which is a big motivating factor. But, of course, there will be those that see modular construction as a challenge to their industry.
Regardless, there is a clear push towards modular construction, and this is now filtering through to government level. Indeed, the Autumn budget announced that the government was “committing to use its purchasing power to drive adoption of modern methods of construction” and sees this as a way to “improve delivery efficiency and boost productivity”.
Whatever your views, modular construction certainly seems like the future of UK house building and we should embrace the new challenges and opportunities it brings.