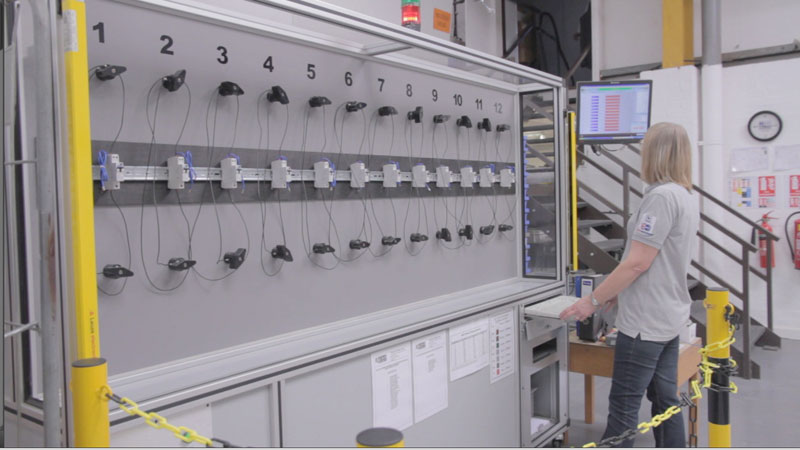
Kieran Jenkins, Factory Manager for M2 Electrical, looks at why a rigorous testing and inspection process is critical to ensuring that modern circuit protection products are safe and reliable.
There’s no doubt that the development in combining the MCB and RCD into the RCBO has changed the way we think about final circuits. Admittedly, the 17th Edition was a major driver, especially for domestic installations and, despite the extra cost of the devices, they are now widely used and specified for their combined safety and overload protection.
Design challenges
If you’ve ever looked inside an MCB you’ll see that it is a busy and complicated bit of kit. If you add the similarly busy and complicated RCD mechanism into the mix you’ll then appreciate the challenge designers were faced with when combining the two. Yet, as with most devices that involve electronic components, technical improvement actually went hand-in-hand with miniaturisation.
The initial RCBOs were of single module (17.5mm) width and the RCD components were housed above the traditional looking MCB structure. This occupying of space within the consumer unit necessitated the enlarging of enclosures to maintain wiring space.
In more recent times M2 were one of the first manufacturers to develop the RCBO into a compact format i.e. maintaining the single module width but being no taller than a conventional MCB. This enabled enclosures to reduce in size again as the compact RCBO offered 25% more wiring space over its previous taller, older brother.
Thorough testing
More technology, however, means more things that can go wrong, so testing of these devices and maintaining standards are vital.
People’s lives, after all depend upon it. When products are offered at super low prices it is no longer safe to assume that all the investment behind the scenes to ensure compliance is there. Just because a product claims a standard, it doesn’t necessarily mean it complies!
At M2 all devices are 100% tested. Initially they’ll undergo thermal bi-metal calibration, followed up with an instantaneous trip test to ensure they’ll respond in the event of a fault.
Following these, a series of batch tests are undertaken on an automatic thermal test set – a substantial investment for the business – that analyses the tripping characteristics to ensure they trip within the permitted time parameters.
Finally they’ll undergo a series of earth fault tests, including a check to ensure they do not activate at a too sensitive level (nuisance tripping).
Each device is assigned a unique serial number to provide full product traceability and the monitored returns level is one tenth of the industry standard for such products.
If such failure rates are so slight then why not relax or reduce the testing routine? Well, recent high profile recalls on similar products within the market holds the answer.
With so much being globally resourced these days, the substantial volumes involved and safety critical products at the end of the process then testing, testing, testing surely has to be the order of the day.