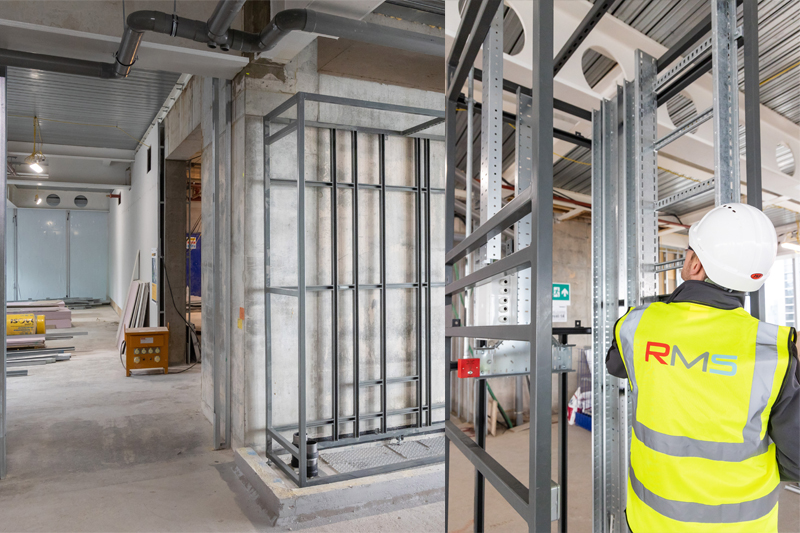
We discover more about how collaboration between RMS, contractors and the end user helped meet strict time deadlines for what is claimed to be the largest offsite manufactured electrical and building services solution in Europe.
40 Leadenhall is a £885 million 900,000 sq ft office development with some retail and leisure facilities in the City of London. It consists of several stepped blocks that includes two towers, one of which is 34 storeys tall and the other 14 storeys high.
The challenge for the electrical and building services was to find a solution that the contractors could install incrementally one floor at a time while sticking to a strict timetable to keep the project on track.
Rising challenge
Due to the scale of the project, the building needed seven main risers, three in one tower and four in the other. Four of these were for electrical services, three for telecommunications and one as a fire rated riser for alarms, emergency lighting and other safety critical equipment. The project also needed a cable management solution to run the cabling to services on each floor.
The proposed design for the main risers was for modular units that interconnect between each floor. These would accommodate a huge amount of services, equipment and cabling. Due to the complexity of constructing such units on-site, RMS decided that the best solution was for an offsite solution delivered to site incrementally to meet the build schedule.
RMS decided to prototype a riser module for testing and inspection to prove that the concept would work in practice before committing to manufacturing. Produced in just two days, the team made some minor alterations to this test module before it was signed off by the end user and the contractors.
Ben Roberts, Sales Director at RMS, says: “It is one thing to have a design drawing for a solution but for large complex projects such as this it really pays to prove that the concept will work in practice. It is better to test a concept than having to alter it on a busy construction site.”
For the main installation RMS manufactured 460 modular riser units that the contractors from LMOB installed one unit at a time. Many of these risers had services, such as electrical distribution boards installed within them. To achieve this, electrical contractors from LMOB worked on-site at the RMS factory in partnership with the company. This ensured that each prefabricated riser module with preinstalled services was quality checked before delivery.
RMS scheduled deliveries so that the riser unit modules for each floor plus standard cable tray, trunking and other cable management products all arrived one week in advance of installation as a complete package.
Each riser module connects to the module on the floor above and below it using a flexible link also designed and manufactured by RMS. These all had different heights since the concrete floors between levels have different thicknesses depending on how high each floor is in the building, with lower storeys having thicker floors.
Time saving solution
Using this prefabricated solution, LMOB reduced the time taken for the electrical installation on each floor from an expected 2-3 weeks to just three days. For the main contractors, time savings such as this can make all the difference to keeping the project on track when it comes to co-ordinating different trades.
Ben adds: “It was a major logistical exercise to ensure that the right modules and standard products were all delivered to a central London site on schedule.
“When people talk about offsite construction, they often think of complete rooms or pods that are connected together. Often, however, a manufactured solution removes complexity from the construction site to help save time and ensure a high-quality consistent build for a complex system.”
He continues: “At RMS we’re often involved in projects that combine bespoke design with offsite manufacturing at our factory with standardised cable management systems from our sister company Armorduct. It is far from a ‘one size fits all’ solution. Modern projects demand flexibility to meet the challenges of a construction site and being able to flex to meet different needs is an important requirement from manufacturers.
“Over the years we’ve learnt that the best results happen when a specifier engages with us at the beginning of a process. In this case they understood what they needed and we provided the design and manufacturing expertise to help them achieve this.”
Benefits of offsite construction
More projects are realising the benefits of offsite construction with a survey conducted by the ECA, CIBSE and SELECT a few years ago showing that almost two thirds (61%) of respondents reported increased productivity and nearly one in two (47%) reported enhanced safety. More than half (57%) saw improved quality of work and less project downtime (55%). Many respondents (43%) also had a reduction in their carbon footprint, which is an increasingly important factor for many UK businesses.
40 Leadenhall is due for completion towards the end of this year. A major part of keeping the electrical and building services installation on track was due to offsite manufacturing removing complexity from the construction site to cut time on-site. With the shortages of skilled labour available it is vital to maximise your time on-site, so the role of offsite manufacturing is set to grow.
Get more details on the RMS cable management product offering here