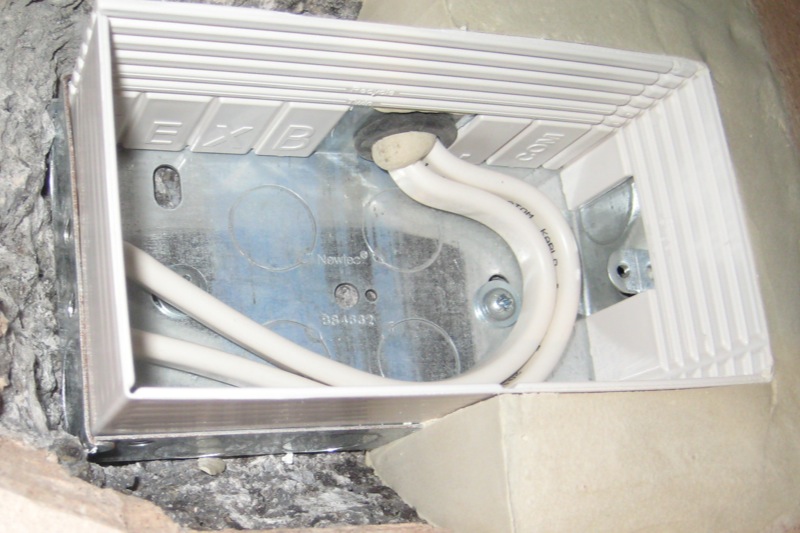
We talk to Paul Coy, inventor of the Vexbox variable extension box, to explore the reasons behind the new version of the unit and the challenges this created from a production perspective.
The word “intumescent” is derived from Latin, meaning “to swell”. The heat produced in a fire causes any product with intumescent properties to expand to many times its original volume. This in turn blocks the route of any fire by creating an impenetrable barrier of carbon or “char”.
Building on the success of the original Vexbox system and realising the importance of products which suppress the spread of fire throughout a building, we recently decided that it was a good idea to invest both the time and money needed to produce an intumescent version of Vexbox, thereby delivering all the advantages of the Vexbox system with the added bonus of intumescent properties.
Significant challenges
One of the fundamental problems to overcome was the production process itself. The original Vexbox is manufactured using an injection moulding process which involves heating pellets of plastic until they melt and then forcing them under high pressure, into a mould. The temperatures involved in this process are similar to those experienced during fire conditions and, therefore, would set off the intumescent reaction, so another method of production had to be developed.
After much research and investigation work, it was decided the answer was to create a “forme” to stamp out the Vexbox templates from a sheet of already intumescent material. Sheets of such material were readily available, however, of all the samples tested (which all proved to be to flexible) none of them had the rigidity needed to form an extension box.
Working closely with a specialist manufacturer of PVC intumescent compounds, we needed to have a brand new material developed. The new material had to be pliable enough to be cut with a knife yet at the same time rigid enough to create an extension box wall. Finally, it was also required to bend and form a hinge point without breaking. This new material is supplied in pellet form which is then extruded to form a strip 70mm wide x 2mm thick.
Testing troubles
Once the Vexbox templates had been produced, they then needed to be tested. Initially, the results of the tests were very good as the graphite expanded to fill the gap between the front of the box and the wall. However, it soon became apparent that the char being formed was just “flowing” into the gap rather than sealing it.
To overcome this problem, a web of fibre glass material, which is relatively heat resistant, was set into the extruded sheet on one side only. The fibre glass web prevents the char from flowing into the wall. Instead, the char expands sufficiently to seal the gap between the wall and the box and then concentrates the expanding char into the box, thereby becoming increasingly dense and cutting off the fire and hot gases, preventing them from entering the room.
Safety first
The act of corporate manslaughter was introduced ten years ago now and its main purpose was to make it easier to prosecute individuals who caused death as a result of not exercising the necessary duty of care where safety is concerned. The problems associated with gaps behind boxes is a good example of one of these scenarios.
By using the new intumescent version of the Vexbox system, it’s now very simple for installers to comply with the building regulations and published good practice guides. This, in turn, will also make buildings safer for occupants at the same time.
For more information about the intumescent version of Vexbox visit: www.vexbox.com