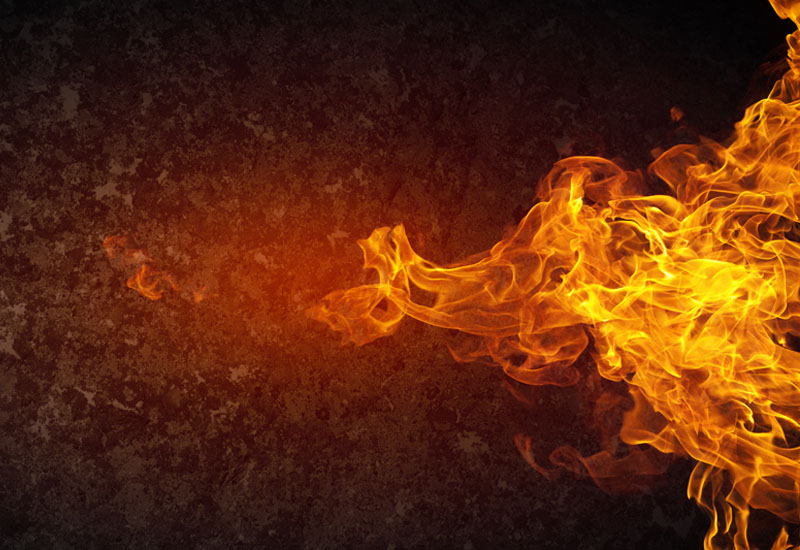
The team at Redditch Plastic Products (RPP) explain the testing and production process that electrical accessories should go through to ensure you don’t end up feeling the heat from dissatisfied customers.
23% of all insurance claims for fire damage occur due to electrical faults. Admittedly, the majority of these claims relate to electrical appliances rather than fixed wiring systems and circuits, although poor workmanship and wear and tear are also contributing factors.
All fires are technically preventable if the control measures, on-going inspections and upgrades are stringent and the correct, appropriate materials are used. The signs of the impending problem are often there: breakers or fuses that continuously blow, lights that flicker or just noticing the overloaded plug adaptor that’s hanging in the wall outlet!
Recent termination designs
Electric current generates heat, particularly if the circuit is being used towards its maximum rating or being overloaded. Over time the expansion and contraction from being under load (and then not) can loosen previously tight terminations. Whilst this doesn’t necessarily reflect poor original workmanship standards, the net result is a potentially dangerous situation. Recent designs of maintenance-free terminations helps to overcome some of these areas, but not all product standards permit their widespread use.
Recent discussions over the use of Arc Fault Circuit Interrupters (AFCI) or Arc Fault Detection Devices (AFDD) to detect arc faults and trip prior to any combustion can take place are certainly gathering pace. This will no doubt also be driven by the insurance companies themselves.
There’s also another fallacy that materials, like cables, last forever. They don’t! Whilst copper can remain functional for over 100 years, depending upon the installation conditions, it’s the insulation that can break down first. Environmental conditions such as ambient heat, moisture or occasional gnawing from vermin can also lead to trapping and pinching of cables. All these factors can increase the likelihood of a fire eventually breaking out.
Correct materials
When it comes to fixed accessories – whether used in a domestic or commercial environment – it’s essential that the correct materials are used. All UK 13A socket outlets, as well as those commonly used in PDUs, must comply with BS1363.Pt 2.
One of the stringent tests that these socket outlets should go through is to check the plastic materials for suitability should internal metal components or connections overheat to the point where ignition could take place.
To test for resistance to abnormal heat and fire (clause 23.2 within the standard), an 850° glow wire is applied to any materials that contain current carrying components. This glow wire test is in accordance with BS EN 60695-2 11:2014.
Most plastic materials will ignite under these test conditions but the test requires that any flames should extinguish within 30 seconds of the glow wire being removed and no droplets of flammable material should ignite a blotting paper situated under the test piece.
To comply with this test, many thermoplastic mouldings would be required to have flame retardant (FR) agents added to the prime material in various percentages. The trade-off in many instances is not to compromise the functionality of the component, which is particularly important where clip forms may be incorporated in the design. FR additives can reduce the strength and durability so it’s important for designers to have a clear understanding of the standards required and identify the material properties at an early stage of the product development process.
Taking a risk
Such enhanced materials obviously carry a premium on cost against standard products and this may explain why items such as PDUs have been produced without using such FR materials. Manufacturers or importers of such products have presumably either been ignorant of the standards to which they need to comply or are prepared to take the risk.
This can be a dangerous game, however, as the application of PDUs, in particular, often exceeds the standard use of most domestic socket outlets. Many are fitted in data cabinets that power servers for bank accounts and websites with 24/7 loading. Others may be sitting in office furniture or specialist lockers where, once fitted, they’re soon forgotten but invariably left constantly on load.
As a UK manufacturer RPP has always resisted the false economy of using cheaper, inferior materials, opting for materials instead that comply with the relevant standards and are completely fit for purpose. All PDUs that have been designed by the company carry the CE mark and are fully supported by the required technical files.