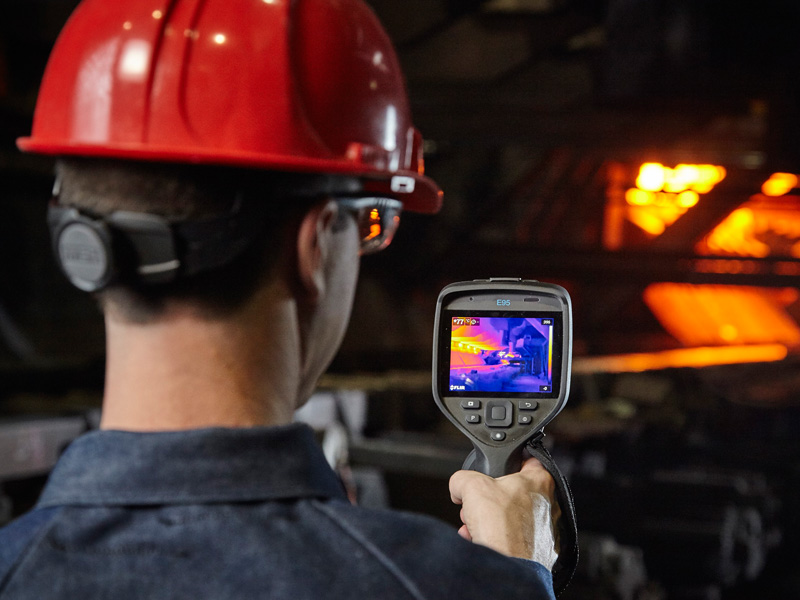
Andrew Baker, Sales Director North Europe at FLIR Systems explains how four letters can help to improve your infrared inspection technique.
When using an IR thermography camera for electrical inspection and data capture, accuracy is key. Whether the camera-operator is an experienced thermographer, or new to the technology, an important acronym to remember is ‘FORD’ – FOcus, Range and Distance.
Modern thermal imaging cameras are really smart but that doesn’t mean they can compensate for every miscalculation. Focus, range and distance are critical because none can be adjusted or corrected once a thermal image has been saved.
To ensure images are meaningful and suitable for further analysis, the camera must be in focus, images must be taken in the correct temperature range and at an appropriate distance from the target.
Just like with any camera, whether digital or thermal, it must be optically focused before an image is captured. A blurry image isn’t just unprofessional, it also produces inaccurate temperature measurements. Good focus = better measurement, it’s that simple.


Out of range – note asterisk symbol, estimating temp value & value not guaranteed to be within spec.
The temperature of the object to be measured must be within the range setting chosen. While many infrared cameras are able to detect and measure target temperature from -20°C to 1,500°C, they can’t do so within the temperature limits of a single image.
Most camera models break up the total temperature measurement specification into a number of defined temperature ranges covering intervals of temperatures that the detector is able to see and image without going into saturation.
When an image is saved, all the data within a particular range is captured. Any temperature points which fall outside of that range, however, are not. So, being in the right temperature range before the image is saved is critical. This is all about resolution, the ability to resolve areas of thermal detail on an object, but also capture enough information to measure temperatures accurately.
An infrared image is made up of pixels, individual detectors that sense infrared radiation. All infrared cameras have limits to what they can resolve of a given sized target at a given distance.
Resolution is a function of the number of detectors in the camera and the size, or Field of View (FOV), of the lens. So, it’s essential the camera operator gets close enough to put as many detectors on target as possible to ensure the best resolution of the object.
If the operator is struggling to fill the spot circle, even though he or she has moved as close and as safely to the target as possible, then switching to a telephoto lens (if available) is another option for better accuracy.
Continuous development of infrared cameras for electrical inspection has made the technology eminently affordable, easy to use and flexible to apply. Nevertheless, understanding the science behind thermal imaging is essential to its successful application, so basic training should always be considered with every camera purchase.
The FLIR Infrared Training Centre (ITC) runs free webinar content, aimed at helping end users to improve their IR inspection process. To view future webinar dates and register your interest, go to: www.irtraining.eu