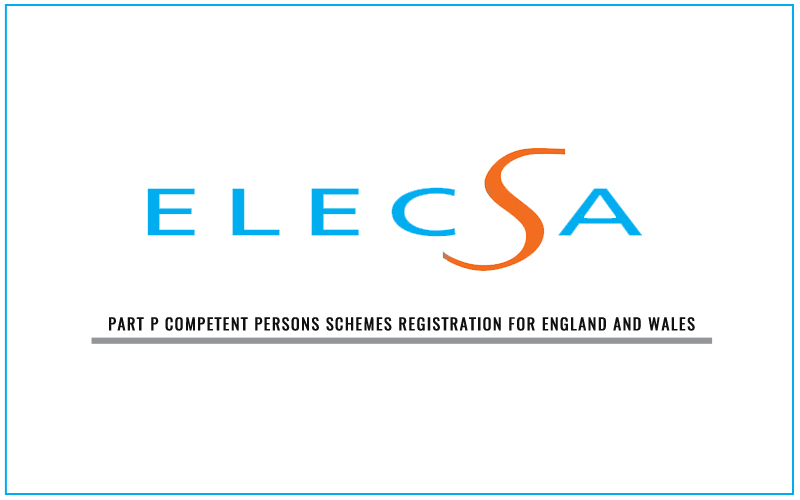
The aim of this article is to offer guidance to contractors when installing a consumer unit and/or similar switchgear manufactured from a non-combustible material meeting the requirements of Regulation 421.1.201, in a domestic installation forming part of a TT earthing system.
Introduction
Where an installation forms part of a TT earthing system, irrespective of the type of material the consumer unit is manufactured from, Regulation 411.5.2 typically requires the installation of one or more RCDs as a protective measure for fault protection.
Any RCD providing fault protection shall be erected at the origin of the installation that is to be protected (Regulation 531.3.5.3.1 refers). In an installation with multiple origins, this requirement shall apply to each origin.
Most TT installations are likely to contain multiple RCDs providing additional protection, or possibly fault protection either, protecting groups of circuits and/or individual circuits. Where this is the case these protective devices shall be selected and erected as to limit the risk from unwanted tripping (Regulation 531.3.2).
Similarly, where multiple devices are installed and there is a need to minimise the inconvenience of unwanted tripping during a fault the requirements for selectivity may need to be taken into account.
Installation of a metallic consumer unit
The installation of a metallic consumer unit complying with BS EN 61439-3 is most likely to be the preferred option for achieving compliance with Regulation 421.1.201. However, due care must be applied to the installation method where a metal clad (Class I) consumer unit is installed in an installation forming part of a TT system.
An earth fault occurring between the incoming line conductor of the meter tails and the metallic enclosure, as shown in Fig 1, will not be detected by the RCD installed in the consumer unit.
The metallic casing of the consumer unit and subsequently all other conductive parts connected to the main earthing terminal (MET) of the installation will rise to a potential approaching close to the supply voltage (230 V to Earth), creating a potential shock risk.
Under such circumstances, due to the high external earth fault loop impedance (Zs) typically associated with a TT system, which can often exceed 100 Ω, the earth fault current is unlikely to reach the level required to operate the service fuse, and even if it does the operating time is unlikely to be within the 1 s disconnection time required by Regulation 411.3.2.4.
For example, if the maximum earth fault loop impedance is taken as 100 Ω also taking into account the seasonal changes of ground resistance for a single phase supply, the earth fault current that will flow under such fault conditions can be calculated as follows:
Clearly, this level of fault current is insufficient to operate the distributors’ over current protective device and therefore, unless a low value of (Zs) can be assured and maintained while meeting the requirements of Regulation 411.5.3 for fault protection, such a fault will remain uninterrupted. For this reason it is preferred that fault protection for a TT installation is provided by an appropriately rated RCD (Regulation 411.5.2 refers).
In addition, the selection of an appropriate RCD for a particular installation shall meet the requirements of Regulation 531.3.5.3.2. Such that, the rated residual operating current of the chosen RCD shall not exceed the corresponding IΔn to the maximum value of earth resistance (Ra), including that of the earth electrode and protective conductor connecting all exposed-conductive-parts. In the example above the maximum earth fault loop impedance is 100 Ω and therefore, the maximum rated residual operating current of the chosen RCD shall not be greater than 500 mA, given in Table 53.1 of BS 7671 and is partially reproduced in Table 1.
Meter tails
It may not be possible to eliminate all the risk associated with protecting meter tails from a fault to earth typically, between the origin and the RCD protective device within the consumer unit.
However, by adopting longstanding industry practices applied by many electrical contractors, such as those listed below, the risk can be mitigated sufficiently:
– use of thermoplastic or thermosetting insulated and sheathed cables for the meter tails (Regulation 531.3.5.3.2.201 refers), and
– positioning of the consumer unit in close proximity to the energy meter, reducing the length of the meter tails and minimising the risk of damage,
– fitting an insulated cable gland, bush or similar protecting the cables from abrasion as the meter tails enter the metallic consumer unit and/or protective enclosure, as shown in Fig 2.
Additionally, in order to avoid the effects from induced eddy currents in the metallic enclosure and associated heating effects, all the meter tails should enter the consumer unit through the same entry point (one cable entry knock-out hole).
Degree of protection
The requirement of Regulation 421.1.201 is intended to ensure that any source of ignition, such as arcing caused by a loose termination occurring within the consumer unit and/or switch gear assembly is prevented from igniting the enclosure while reducing the risk of any fire from spreading externally.
It is for this reason that the entry points of all cables, including that of the meter tails, into the metallic consumer unit should not, so far as reasonably practicable, reduce the fire integrity provided by such equipment. Cable entries, such as those often used for back entry into the consumer unit must be provided with suitable sealing methods and may include intumescent gaskets, grommets and/or fire sealants to maintain the degree of fire integrity.
However, it is generally accepted that the requirements of Regulation 416.2.1 and 416.2.2 which are intended to prevent contact with live parts also help to maintain the fire integrity of the consumer unit. Such that, all cables entering the top surface of the consumer unit shall need to maintain a degree of protection of at least IPXXB or IP2X and IPXXD or IP4X applicable for elsewhere.
Where the installation of a consumer unit is to take place on or in a combustible prefabricated wall, additional precautions must be applied to prevent the ignition of surrounding materials. Equipment having a greater degree of protection will be required which must be maintained of at least IP3X (Regulation 422.4.1 refers). Using appropriate types of equipment complying with the relevant standards for temperature rise will meet this requirement (Regulation 422.4.201).
Where the installed equipment, such as an all-insulated construction consumer unit, fails to meet the requirement of Regulation 422.4.201 further preventative measures shall be applied to prevent the spread of fire. This may include the use of a secondary enclosure manufactured from a non-combustible material of suitable thickness, for the containment of the consumer unit (Regulation 422.4.202 refers).
Summary
There is a greater risk associated with the installation of a metallic consumer unit in an installation forming part of a TT earthing system. It is for this reason consideration must always be given to the location of the consumer unit and length of meter tails in relation to the energy meter. Appropriate installation methods and practices that have been applied by electrical contractors for many years continue to minimise the risk of damage to the meter tails and subsequent earth faults.
It must be recognised the need to maintain the degree of ingress protection and the fire integrity of the consumer unit in relation to the type of installation method.